The romantic who put it all on the line to rejuvenate classic Astons
Paul Spires, President of Aston Martin Works, limps into a modern glass-enclosed office, one leg in a brace after a sailing accident. Once our meeting is finished, he will join a pal on a helicopter test flight. Other times you’ll find him behind the tiller of his light aircraft or at the wheel of his two vintage cars: a Rolls-Royce Silver and Aston Martin DB9 Volante.
Spires has a passion for all things motive—hull, wings, wheels, whatever—and his drive has brought this factory restoration operation success after success, even amid the financial ripples that have recently rocked the Aston Martin mothership.
The Newport Pagnell, UK, facility, two hours northwest of London, is a distillation of everything Aston Martin. Tickford coach-built bodies for Aston Martin until 1955, at which point Aston bought the facility and made cars there until 2012.
The small town is now home to a service shop at which three Valkyries await collection by their owner. Rarities such as a One-77, and even a Taraf, are undergoing maintenance. Walk further through the clinically clean and brightly lit buildings and you’ll seemingly step back in time. Artisans keep busy shaping metal on an English wheel or hand-stitching Connolly leather for an interior.
Under restoration during our visit is a DB MKIII which pre-dates Aston’s time at Newport Pagnell, a selection of DB5s from as far afield as Vietnam, and, of course, the continuation cars. In a stroke of inspiration, Spires realized that Aston Martin’s back catalog was incomplete, and he set about rectifying that by building brand-new versions of cars that never finished their planned production runs. Combining modern precision machining and traditional coachbuilding techniques, he wagered, would actually improve on the original recipe. Important, too, was that Aston Martin Works stood to become a highly-profitable branch of the 110-year-old company.
Awaiting completion in the shop is the final Goldfinger DB5, while two DB4 GT continuations are also back “home” at Newport Pagnell for servicing. It is these cars, more than anything else, that will be Spires’ legacy at Aston Martin Works. And if wasn’t for his sheer determination they wouldn’t have happened at all.
Spires joined Aston Martin Works in 2012, originally hired to set up a new-car sales business at Newport Pagnell. By 2013 it was the second-biggest dealership in the United Kingdom. A year later he was invited to take over the whole operation.
“Financially we were okay, but we weren’t generating the level of returns that I felt the business could do,” he explains. “Being slightly romantic as well, we stopped building cars here in 2007, and this place actually pre-dates the internal combustion engine, with horse-drawn carriages being made in the 1850s, and I thought, what a shame that we don’t build vehicles here anymore.
“We couldn’t build a modern vehicle so I came up with the concept of the DB4 Lightweight continuation, which was supposed to be a one-make pro-am championship. It took a long time to get the buy-in from the senior team within Aston Martin to do that program. They looked at it for two, maybe two and a half years and there was a lot of skepticism, and quite rightly so. Will this hurt our heritage credentials, will it destroy the Aston Martin brand. Will people see it as cash cow?
“It was quite brave. I won’t mince my words, I put everything on the line. If it didn’t work, I wasn’t going to be here.”
With the board in agreement, Spires and his team began the job of completely recreating the car from scratch as well as the process to build it.
“It allowed us to not only invest in the place and our processes, we brought in a much younger, very dynamic engineering team into the business to deliver that car, none of whom were even born when the DB4 GT was around so it was a completely clean sheet of paper,” he says.
State-of-the-art three-dimensional scans were taken of original cars so that new jigs could be fashioned with unparalleled accuracy, blueprints were tracked down and CNC machines used to fabricate components from raw metal, while the bodywork and interior were hand-crafted in the traditional way. “It was completely new; there were no old bits on it, every component was new,” says Spires.
“We delivered that project in an unbelievably quick period of time. In nine months, we had a fully functioning prototype car running. Then literally the week after we finished the car Jeremy Clarkson took it on his Grand Tour.”
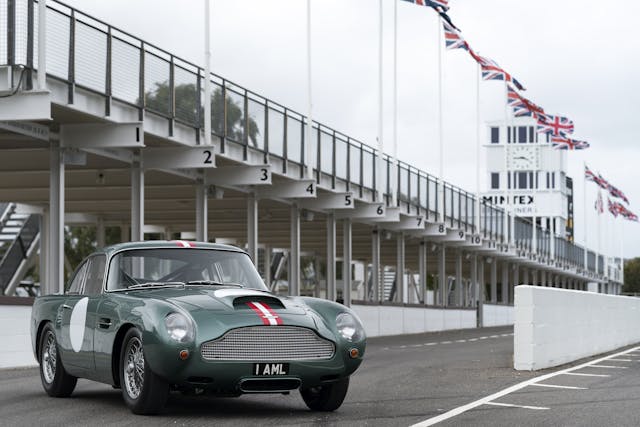
As well as surviving Clarkson, the DB4 GT was tested at Silverstone and driven flat-out at Nardo in Italy by Aston endurance racer Darren Turner. Spires’ reborn DB4 GT took a beating and never gave up. The mix of modern engineering accuracy and traditional craftsmanship was a winning formula. “From the moment that car started to the moment we sold it to a customer in America, that car has never failed to proceed, which is unbelievable,” he says proudly.
“That car really made a big difference. We sold 25 in three weeks at 1.5 million pounds plus taxes, plus options.”
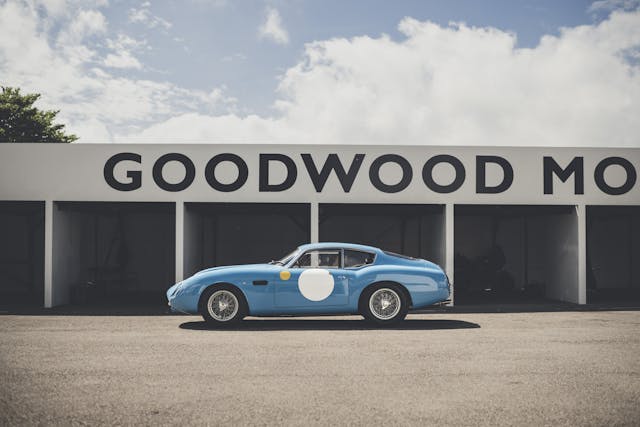
Next came the DB4 Zagato continuation, which at the time it became available in 2019 was the most expensive production car in the world, costing £6M (about $8M).
“It was a natural progression and I thought we’d do three or four cars, but I went to see Andrea Zagato and he got super excited. He said, ‘Let’s make it our centenary car and make another 19 like we did originally.’ Again, we sold those all over the world.”
Now, the last of 25 Goldfinger DB5s is almost complete, marking the end of Aston Martin Works’ most ambitious continuation project to date. Working with the special effects team at EON Productions, Spires and his engineers were able to build an immaculate DB5 reproduction, with all the gadgets that made it the most famous car in the world. Unlike during filming, circumstances during which each gizmo need only work for a take or two, DB5 Goldfinger owners expect their cars to perform on the button every time.
“We ran every single gadget though five thousand continuous cycles on the bench to make sure we have that robustness in the car.”

Customers also expect the car to drive exactly like a DB5, so the modifications needed to be kept as light and compact as possible. The car’s Kevlar bulletproof shield (which really is bulletproof) is housed within a carbon-fiber cassette, for example. For authentic drivability, Spires insisted the car should run on cross-ply tires and have no power steering.
“It’s very pure. It’s got the look, the sound, and the smell. When you put the 2023 car next to a 1964, sometimes even I can’t tell the difference,” he admits.
When Goldfinger production is finished, Spires says, there will be another model to follow. But he’s in no rush.
“You have to have a good story behind it and a value proposition, but it’s been an amazing journey and it’s not finished yet. We always have something up our sleeve.”
***
Check out the Hagerty Media homepage so you don’t miss a single story, or better yet, bookmark it. To get our best stories delivered right to your inbox, subscribe to our newsletters.
Beautiful Aston Martin’s.
1.5 million pounds and “that car has never failed to proceed, which is unbelievable”.
Setting the bar rather low, aren’t we?
This is Aston Martin, after all. That’s a high bar.