Reinventing the Ford Model A four-cylinder
Is your Ford Model A crying out for emergency underhood attention? Thanks to a Campbell, California, entrepreneur, you can now update your car’s powerplant with 21st-century design features created using the latest engineering and manufacturing methods.
Enter Terry Burtz, a retired Lockheed mechanical design engineer and 60-year Model A enthusiast. “I believe Ford Model As are the backbone of the antique car hobby—a pastime I definitely want to endure,” he says. After rebuilding several Model A engines, Burtz identified their many weaknesses, including the materials they were originally made of. By inspecting engines that had been modified for oval track competition and Bonneville speed record attempts—plus a few used to power aircraft, where reliability means the difference between life and death—Burtz was able to develop major design improvements.

“Over the years I discovered that only one in twelve Model A engine cores are suitable for rebuild because of rust, water jacket cracks, and/or poor machining by past rebuilders.”
Burtz currently owns half a dozen Model As, and he takes great pride in his $4000 upgrade kit, which consists of a fully machined block, new connecting rods, and a crankshaft incorporating features Henry Ford never dreamed of.
Using computer-based design imaging called Solid Modeling, Finite Element Analysis to measure stress and strain, 3D printing to make core patterns, and CNC machining methods, Burtz created a replacement cylinder block and various internal parts incorporating this wish list of modern features:
- 5 main-bearing supports instead of the original 3
- Larger, 2-inch-diameter crank and rod bearings
- 5 bearing journals to support the camshaft
- Shorter-length bearings to facilitate a stiffer crank configuration
- Commonly available bearing inserts to replace the antiquated poured Babbitt bearings
- Replaceable cam bearings
- A fully pressurized lubrication system with drilled oil galleries feeding 17 main, rod, cam, and thrust bearings—and the ability to add a full-flow oil filter
- 8 crankshaft counterweights to provide primary balance
- A new radial-lip rear main seal
- Thicker block webbing and sidewalls for improved rigidity
- Larger streamlined intake ports for better breathing
- Steel exhaust valve seats to increase longevity
Burtz’s simulations proved his design tough enough to provide 150 hp at 5000 for hours on end. In a 2020 road test, a 5-window Model A powered by the new engine ascended 1700 feet of elevation in just over 7 minutes on a five-mile Colorado mountain run.
In his efforts to improve the A’s engine, Burtz was careful to replicate Ford’s original factory appearance with its exterior. “Having judged at several Model A national conventions and other events,” he says, “I learned that no owner wants an engine or component part at odds with original appearances.” Furthermore, this new gray iron block is machined with all the interfaces and dimensions needed to bolt on original factory components.
Premium materials, including a modern alloy for the cylinder block, forged connecting rods, and a nodular iron crankshaft and camshaft, combined with induction hardening, help assure high-mileage longevity in tough applications such as trailer towing and mountain climbing. “Model A owners want enough power to accelerate well on freeway entrance ramps and sufficient cruising speed to avoid impeding traffic,” Burtz says
“Another notable discovery of mine was that a new Model A engine cannot be affordably made in the USA. I learned the hard way that West Coast foundries are not up to the complex block casting process. Like several OE brands selling vehicles in the U.S., we turned to China for this engine project.”
Burtz’s strategic partner is John Lampl of Leesburg, Virginia, who brings over 30 years of Asia-based manufacturing and product development to this project. Burtz and Lampl shook hands in 2019 to begin collaborations. Lampl had already successfully created a remake of the four-cylinder engine built by Willys and Ford for WWII and postwar Jeep use. Using that experience and the same Asian manufacturing operations greatly accelerated the fruition of the new Model A engine project.
The new parts are being produced in several factories that combine an entrepreneurial spirit with modern manufacturing methods. To date, more than 460 “New Engine” kits from several production runs have been delivered.
In addition to the $4000 block, crank, and connecting rod package, Burtz offers new 30-pound flywheels for $375, cylinder heads with a 6.5:1 compression ratio for $400, and replacement camshafts for $400. All parts are covered by a 1-year limited warranty, so long as they’re not used in motorsport or aircraft applications.
“Our combination of quality, reliability, price, and factory appearance means that we have no direct competitors,” Burtz says. If you’re looking to keep your Model A humming sweetly, now you know where to look.
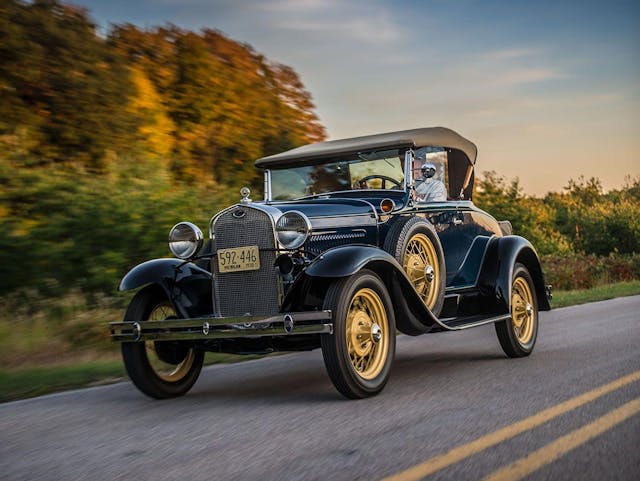
***
Check out the Hagerty Media homepage so you don’t miss a single story, or better yet, bookmark it. To get our best stories delivered right to your inbox, subscribe to our newsletters.
As an ex ‘A’ Model Ford owner I can relate to this excellent product’s need .
Very few people know how to properly tune, maintain or hop up the stock engine, my ’31 5 window coupe had a balanced crankshaft and ‘B’ Model head for more compression it easily went 80 MPH, I added “brake floaters” because the original roller brake shoe design was terrible .
The only real problem with speed in an ‘A’ Model is the tire’s contact patch ~ once you get the brakes properly sorted (stock the have a rear bias) it’s an easy thing to lock up all four wheels, this ability and knowledge of how to use it allows proper brake modulating .
I had four ‘A’ Model Fords, all were excellent cars and were used in Los Angeles as daily drivers including freeway speeds of 60 MPH =/- .
-Nate
So sad that these improvements can’t be manufactured in North America. I wonder if enough effort was made to search out suppliers. Making these in China just seems wrong.
This is great news for the model A people. How about something for the old Pontiac straight 6 cylinder crowd
Lots to like here. I, too am dismayed that this cannot be produced in the USA. Can such profitable industry be brought back to the USA? I hope so.
Very interesting discussion about the Deere Foundry/GM Iron Duke connection as I’ve lived near that foundry since it was built and know many Deere people. I’d not heard the $33 price quote.
I’m an old hot rodder, automotive machinist, Model A lover, and knew a guy that ate lunch with Henry Ford.
Sorry, Henry would NOT have spent the money to make it better. It took decades (and his grandson’s leadership) to get them right.
Henry owned the industry in 1918 and GM took it away from him easily mostly because he was such a cheapskate.
I’d LOVE to have a Model A with juice brakes, better tires, and a better motor. 80 hp would be enough. Volvo? Cummins? Burtz?
Wow all the reply’s from people who do not own or grew up with the model a’s and even flown airplanes with one in it like I have. Model t blocks hardly ever cracked. Model a blocks almost always cracked. Just give me a stock dimension B block cast out of 356 aluminum. To get away from the cracks and be easy to weld repair if it did. My model A has a model B that spent 1000 hours flying in my airplane hooked to a 5 speed transmission. Drives like a dream with juice brakes and improved stearing gear.
Pretty boring – no information on the vehicle, engine, performance – just a drone shot of a car driving. Waste of time.
Where do i buy the engine or the new parts. I have a 1928 ford model a
Maynard Rome cell 303-263-1612 maynardrome1000@gmail.com
It’s great to see these old machines being not only kept alive but brought into the present for more people to experience. Best wishes for your success!