Inventing a New ICE in an EV Age: The Waissi Engine
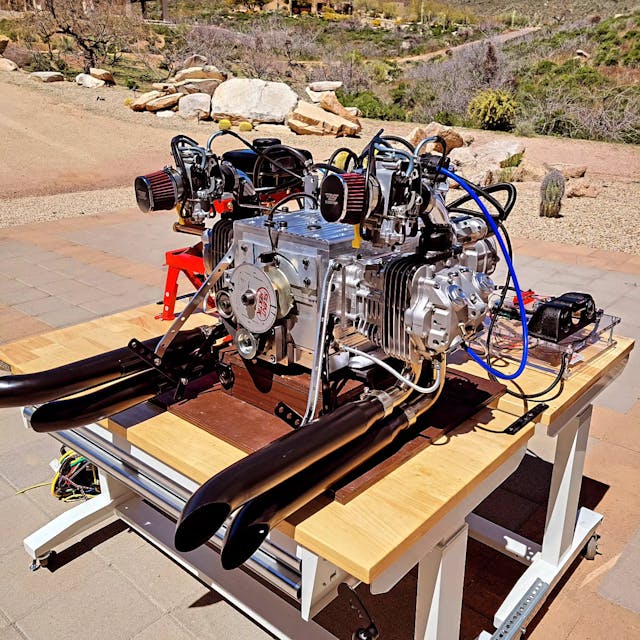
I admit to being a bit of a romantic when it comes to inventors, particularly independent ones who are pursuing their dreams without the resources of a large corporation, government agency, or university. There’s something special and quite human about seeing a connection that others don’t see and keeping at it. Clessie Cummins made more than 3000 prototypes while developing his fuel injector for diesel engines.
Sometimes the story ends up in failure and obscurity, other times in generational wealth and celebrity. More often than not, the success lies not in business or fame but rather in increasing human knowledge. Of course, sometimes you learn that something simply doesn’t work. For most inventors, that’s not a reason to give up but rather to consider alternative solutions. Like Thomas Edison said, “I have not failed. I’ve just found 10,000 ways that won’t work.”
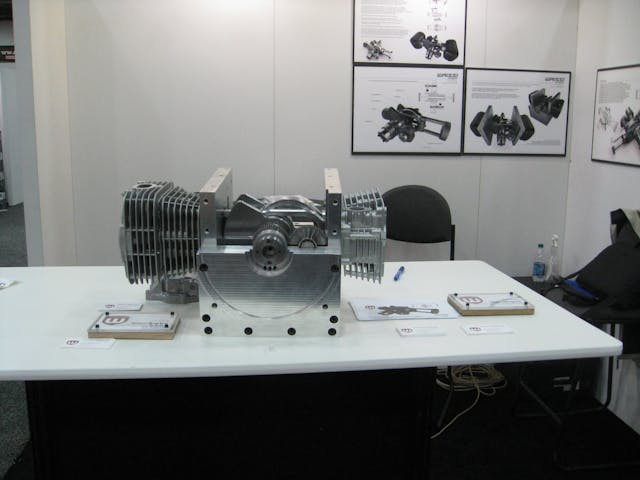
About 50 years ago, engineering professor Gary Waissi was teaching a course in physics, and during his lecture he doodled a sketch of a disc mounted eccentrically on a shaft and realized that a piston could push directly on the edge of that disc, converting linear motion to rotational motion. Eliminating connecting rods and much of the crankshaft would have advantages in terms of reducing friction and weight in reciprocating-piston combustion engines, possibly making an engine based on the concept more efficient than conventional designs.
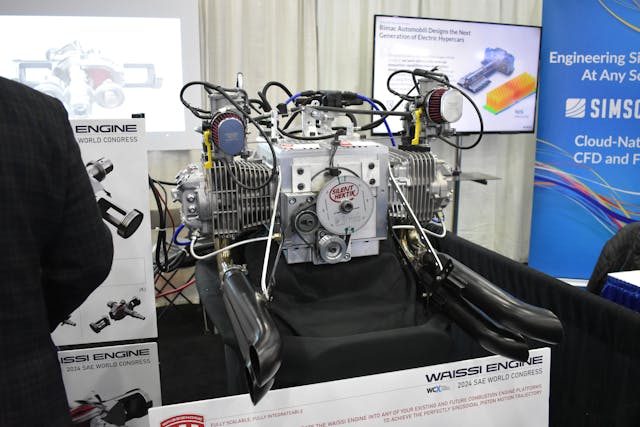
In the mid 1990s, then at Arizona State University, Waissi started working in earnest on the engine concept, based on a horizontally opposed two-cylinder design. The two pistons are linked together and move in tandem as they push on the disc and it rotates. Compared to a conventional engine, where forces from the connecting rod tilt the piston at an angle to the cylinder walls and create friction, the ganged pistons travel perfectly parallel to the cylinders. Later refinements put a circular ring around the “crankdisc,” upon which the pistons acted and within which the crankdisc spun. Additional development determined that flattening the sides of the annular ring that are in contact with the pistons further reduced friction.
You can read Waissi’s technical description at bottom.*
To be honest, it’s easier to understand it with drawings and animations, but the bottom line is that it’s a very elegant idea.
Ten years ago, Waissi came to the Society of Automotive Engineers World Congress, where he displayed drawings, animations, and some engine parts, but the engine had not yet run outside of the digital domain. Since then, he’s built two running versions of the engine, with the current motor, which Waissi describes as “Version 1.9999 repeating,” being the sixth-generation design. That engine is now on display at this year’s SAE convention, and I got a chance to discuss the project’s progress and trajectory with the professor.
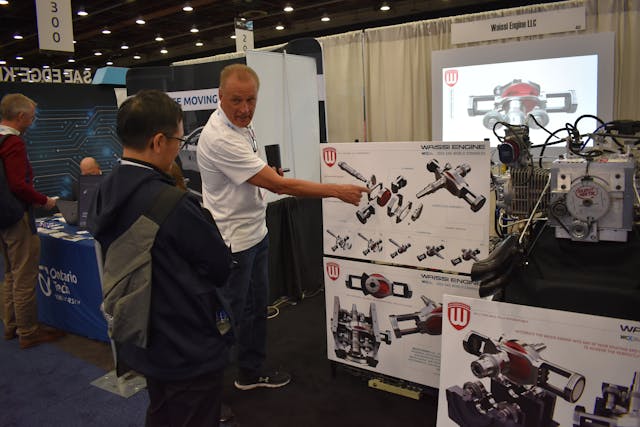
The concept will work with both spark (gasoline) and compression (diesel) ignition. I didn’t ask but I’m guessing it will work with Atkinson as well as Otto cycles.
The project has been pretty much self-financed and now reaches into six figures. Waissi Engines is a two-man operation. Gary Waissi is now retired from teaching and devotes much of his time to the project, with son Robert, also an engineer (who works in audio by day), helping. Gary says that the annual outlay has been between $10,000 and $20,000 a year, depending on what components they need to have made.
Anyone who has owned a Honda motorcycle or a car with an air-cooled OHC engine will recognize the cylinder barrels and heads on the prototype. As a matter of fact, that’s what drew a Honda engineer to the Waissi booth, texting photos of the motor back to Hamamatsu. Engineers from Ford, General Motors, and a handful of Chinese automakers also expressed interest. The overhead valves are operated via chains driven by auxiliary shafts geared to the main shaft. The animation above also shows some counter-rotating weights, also on auxiliary shafts, which Waissi said were intended to prevent rocking of the engine but in practice were found to be unnecessary.
As shown by the use of production Honda components, the Waissi engine is compatible with current automotive industry manufacturing and assembly methods. There are no exotic materials used, and all components unique to the engine can be made with conventional manufacturing processes.
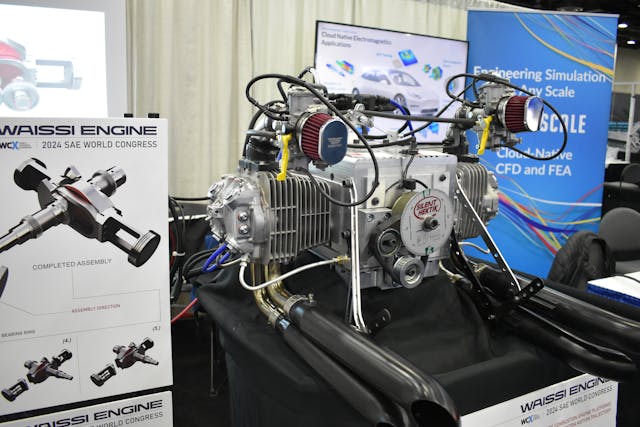
Waissi says there have been “nibbles” from major manufacturers. Beyond its applicability as a primary powertrain component, because of its compact size and light weight, the Waissi engine could see duty as a range extender in a hybrid system.
Personally, I think he needs to put it in the back of a vintage VW Beetle as a publicity stunt. Waissi has given some thought to possibly powering a VW-based dune buggy with the opposed-piston “V-180 degree” twin. With just 677 cc of displacement, the 175-pound engine is calculated to put out about 80 horsepower, though that figure remains to be tested on a dyno. Eighty horsepower out of less than 700 cc displacement is impressive in terms of specific output. What I found even more impressive is the fact that the engine can run at 10,000 rpm or higher.

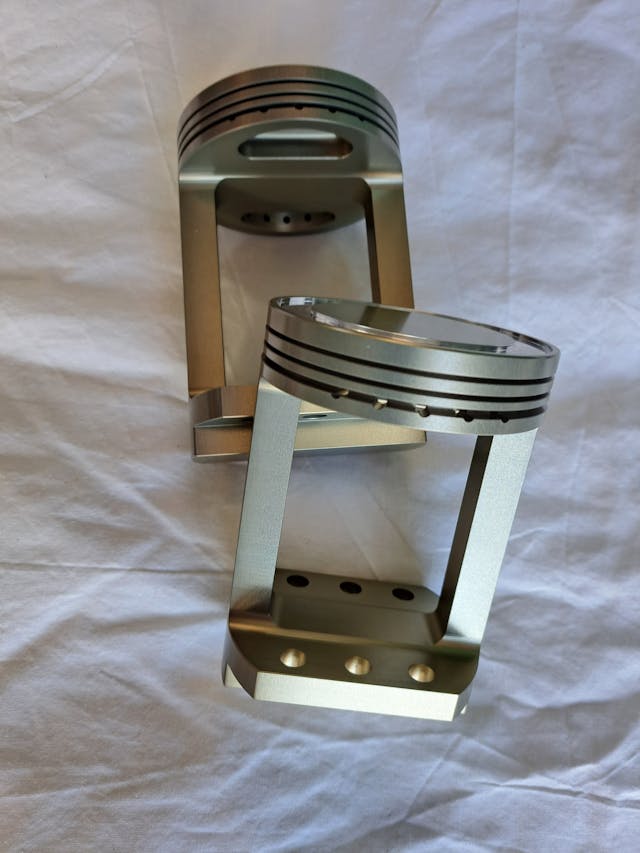
While the Waissis have not yet run emissions or fuel-efficiency tests, it’s still a piston-based, overhead-valve engine with a more or less conventional combustion chamber, so unlike thirsty and relatively dirty Wankels, it should be as clean and at least as fuel efficient as conventional piston motors. Even if those specifications are only equivalent to conventional engines, it would be cheaper to build, as it has fewer parts to assemble.
Since the most powerful engine that VW put in the Type I weighed 244 pounds and put out just 60 hp, a Waissi-powered Bug or dune buggy should probably scoot pretty well. Actually, a production version of the Waissi engine would likely weigh even less than 175 pounds, as the prototype crankcase is milled from a big rectangular billet of aluminum, with no attempt made to reduce the finished weight.
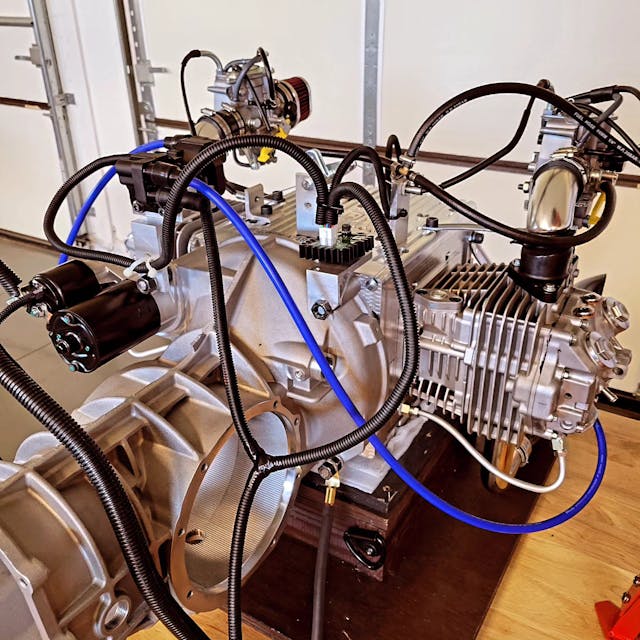
The Waissi engine isn’t the only new take on piston-driven combustion engines to have been displayed at the SAE World Congress in recent years. Nautilus Engineering showed a novel compression-ignition engine with multiple combustion chambers, intended to improve the emissions performance of lawn equipment, but the company appears to be defunct, and the domain name for the company website is for sale.
When Gary Waissi had his minimalist booth at the 2014 SAE convention, Scuderi Engine had a large and expensive open-floor display with a cutaway example of its split-cycle engine inside a plexiglass case and another version mounted in a midsize sedan. Scuderi Engine was founded by the children of refrigerant compressor pioneer Carmelo Scuderi about 20 years ago to develop and license the engine that he patented. Scuderi Engine released a video of the engine running on a test bed in 2012, but the company has been mired in legal difficulties with the Securities and Exchange Commission, and with Toyota’s Hino division. As yet, the Scuderi engine has not come to production. The company still exists, apparently to manage a portfolio of hundreds of patents. A related company, Scuderi Clean Energy, rebranded as ESG Clean Energy, is ostensibly in the business of selling power generation while putting a lot of emphasis on the carbon capture market. The combination of the lawsuits, the emphasis on patent management and licensing, and buzzwords like “carbon capture,” coupled with ESG never publicly showing a running version of the engine (to the best of my knowledge and research), have made a few people skeptical about the Scuderi ventures.
Compared to Nautilus, which had a team of engineers and backing, and Scuderi, which worked hard at selling stock, cultivating investors, and putting on an impressive show, Waissi Engine is a modest venture. The LLC doesn’t even have a website. At 75, Gary Waissi doesn’t seem to be looking to make a fortune off of his idea, but rather to make a working engine and prove his concept. At this point, he seems to be succeeding. Perhaps there’s a lesson to be learned from that.
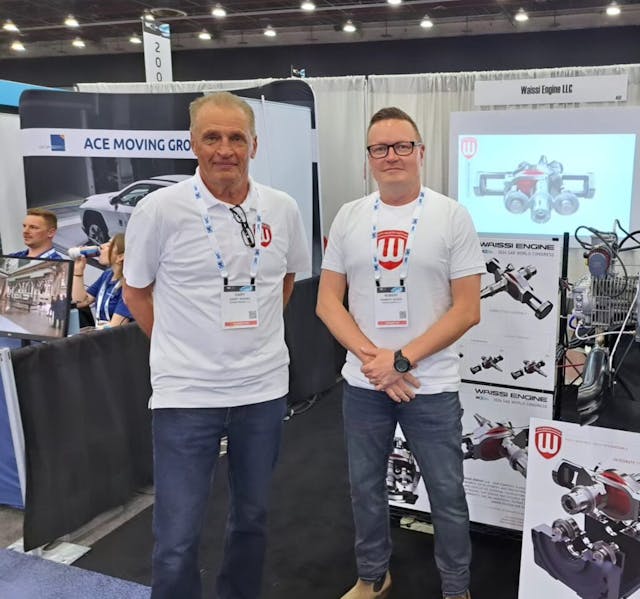
Asked why he’s devoting his time and not insignificant amounts of his own money to developing a new internal-combustion engine at a time when the industry, amid considerable government pressure, is moving quickly to battery-powered electrics, Gary Waissi said that ICEs will still be around for a long while.
“We have to consider the entire life cycle of an electric vehicle and its total environmental impact (from mining to electric grid to use to heavier impact on roads to replacement of batteries to disposal, etc). I think the future will not be one or the other, but some combination of technologies, and the internal-combustion engine will be in that mix. Also, alternative fuels and their research (including hydrogen, etc.) show great promise.”
Words of Waissi
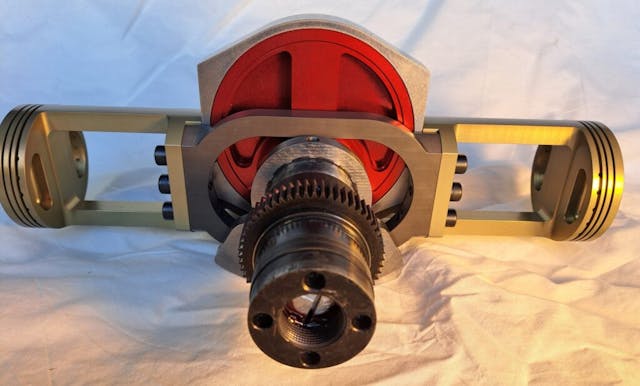
*GW: In the earlier version, we allowed the bearing ring (a perfectly circular ring) to slide under hydrodynamic conditions (oil pumped from inside the main shaft through channels inside the disk to under the bearing ring) on the top surface of the crankdisc. We noticed that allowing the bearing ring outer surface to slide/roll against the piston base created a higher-than-calculated (and expected) friction between the outer perimeter of the ring and the piston base. So we decided to change the outer perimeter ring shape to have a flat (or convex) surface against the piston base flat (or concave) surface and pump oil through the ring to that outer surface. This created a hydrodynamic condition between the outer part of the ring (non-rotating ring) and the piston base. This lowered the friction to the same level as friction inside the bearing ring against the crankdisc (to similar level and conditions as in the main journal(s) of a common crankshaft with cranks and piston rods). Theoretically, the inside surface of the bearing ring serves the same function as the big end of a piston rod; and, correspondingly, the outside surface of the bearing ring against the piston base serves the same function as the small end of the piston rod. The rigid piston structure does not allow the piston to tilt, and the piston side supports distribute the force against the cylinder walls over the combined length of the pistons, whereas in a regular combustion engine, the piston rod pushes the piston, in an angle, sideways against the cylinder wall. Our design significantly reduces all these main friction components.
***
Check out the Hagerty Media homepage so you don’t miss a single story, or better yet, bookmark it. To get our best stories delivered right to your inbox, subscribe to our newsletters.
Intriguing, but it seems to have a lot of rotational mass swinging around for an engine that is supposed to eliminate rotational mass. B52s are still in service because sometimes you get it right the first time and it takes a lot of time and revolutionary thinking to come up with a better mousetrap. The internet is loaded with various piston drive configurations, rotary valves, so on and so forth, but the tried and true piston rod engine still seems to be the right answer for ICE after all this time. Maybe this guy is on to something, but even then he will still have to nudge his way into a very competitive, highly optimized market
Funny, but this is not new… There was Rhombic Drive, and perhaps the most interesting engine, the Dyna-Cam aircraft engine, a cylindrical form,12 cylinder (6 bores, two ended pistons moving fore and aft against a drive plate, arranged in a revolver like cylindrical shaped block, not unlike the opposed cylinder concept pictured here, or a modern A/C compressor) engine with full FAA approved aircraft engine certification, that has yet to make it into production (through no fault of the engine itself). The engine exhibits exceptional power output, and a compact, jet engine or gas turbine form that would make it easier to package into an airframe.
Transferring the movement of a piston directly to a drive shaft/plate is not a new concept, and the Dyna-Cam engine design has made it through FAA testing and certification, just like your Lycomming 540. Both the Rhombic drive and the Dyna-Cam, don’t have problems of side thrust of the piston in the bore, and transfer piston motion directly to the drive disc.
Anyway, FAA certification proves to me that the concept is viable, but is it worth the trouble to produce or develop it for automotive use? Is it, in real life, a better system than the reciprocating piston engines that we have today, or just an incremental improvement over what we know to be reliable and proven but perhaps obsolete technology? Or… Is it simply impossible to put such a design into production with existing financing solutions?
Perhaps this question doesn’t matter, as the Waissi engine, like the Dyna-Cam, which was a proper aircraft engine, with proven performance and production tooling), became mired in problems with investor schemes and SEC as well. It seems as though valid concepts like this (or, in fact, fully tooled, production ready and certified engines), where outside funding is required, always seem to fail spectacularly, embroiled in SEC related lawsuits. It always ends up with the original designers, betting it all and losing, while the tooling ends up in the hands of investors with no ability or need to produce or promote the product.
I often wonder if these concepts came from someone with the necessary assets in place to achieve production, would be successful. You know, like Tesla.
When the description of the financing problems is longer than the description of how the engine actually works, and its supposed advantages, there is a problem.
I admire the innovation and the fortitude to build and pursue a novel design. But, this design appears to create more problems than it solves and with a great deal of complexity. It also has far greater friction surface area overall and it looks bloody expensive with its many machined parts and complex surfaces. Many novel ICE designs have sought to reimagine the valves, introduce variable compression ratio or displacement and reduce part count. This engine has conventional pistons and valves and I see no way for it to distinguish itself. Nevertheless I’m fascinated by the effort to make it a reality.
Natty design and a labour of love. I was thinking of one side of a steam train connection rod without the rods! It’s going to need a high grade oil.. thicker to allow for the opposing forces to push pull the pistons on the ‘concentric cam’ as it were. It won’t solve the emissions ruse though, but who cares. It works, that’s the main thing. Hope it doesn’t need an extra balance shaft as it looks pretty shaky, but maybe that’s just a mounting issue?
I wonder how they will solve the emissions issues with air cooled. That is what doomed the GM and VW air cooled.
This would make a good light aircraft engine.
I wondered about that too. With modern forced induction 4 cylinder and even 3 cylinder engines they run very lean, on the edge of detonation. Hence the need for EGR valves and even EGR coolers on variable valve timing engines. It’s a very interesting idea but it all depends on fuel efficiency and an engine that has to run 11 to 1 fuel to air ratio will never be practical in today’s automotive world.
They use VW engines in many cases. ie. Turbulent and home built’s. They are at least proven designs and I think pilots will prefer a tried and tested Block?
Methinks you’ve not seen the displays at Oshkosh or Sun-n-Fun.
As a SEL pilot, this is almost the opposite engineering principle of anything bigger than an ultralight.
Ultralights are dominated by Rotax 900-series engines. Mostly because they’re solid designs. I’m not saying this isn’t, I’m just saying at 1,500′ you don’t want to be pondering if it is.
In relation to SEL aircraft, it’s virtually the opposite. My Lycoming in my PA-28 (an O-360) is 361 lazy cubic inches, that weighs a ton (for it’s size), is ridiculously overbuilt, and designed to just slowly wear out, not explode. Ever. For which I’m thankful when I’m cruising around at 8,500′.
I’ve had cylinder jug scores, deep ones, causing compression losses in my Lycoming that you don’t even feel because it’s designed big, lazy, and relatively impervious to damage.
Plus, if you think EPA standards are tough to get this motor certified, wait until you meet the FAA.
I wish these guys a lot of luck. Truly hope as a hybrid/generator powerplant, or a light replacement for my 2CV/a Beetle it’s an option!
I’m psyched for these engine pioneers and hope for their success. I also admire their style and pray that they are more honest than other in the industry.
And to the writer, Thank you for profiling the lavish excesses of the Scuderi Group. Scuderi Group investors gave the family close to $100 Million with some people taking second mortgages, and others being persuaded to move money from retirement funds and depositing them into Scuderi Groups coffers. Now, having never benefitted from a promised IPO and never receiving a penny from the rebranded ESG Clean Energy, investors no longer receive any invester newsletters or other information, except for PR Newswire releases. Some investors even died without a return, and worse yet, no information.
Hey Ronnie. Why’d you already edit the article?
Surely, the Bourke engine is simply being rehashed here.
The Bourke engine, or the even earlier Scotch Yoke as used in locomotives and other reciprocating mechanisms, but with some interesting friction-reduction adds.
Yes. I thought “Scotch crank” right away. Old GF used to call me that.
The downfall of the Bourke engine was that it was 2-stroke. The scotch yoke idea is sound for a 4-stroke, but you need case compression if you want to use case pressure for induction in a 2-stroke. Pistons shuffling back and forth in tandem don’t do that. This design may hold some promise.
Ronnie, what happened that made you edit your article and temper some of your comments?
AB and LD: I made the edits. Scuderi’s numerous tribulations with the SEC and others, while noteworthy and well-documented, are not the primary focus of this piece, and these changes were initially intended but slipped through. That’s on us, not Ronnie.
Once an article is published, I have no ability to edit things beyond sending an email about it to my editors. Can’t even fix a typo by myself.
As it happens, I actually raised the possibility with my editor of editing the Scuderi material when I submitted the article so I’m cool with the changes. Like Eddy said, it’s not the main focus of the piece. Still, with new inventions, ventures, and entrepreneurs’ promotions, it’s appropriate to maintain some level of skepticism, at least until you actually see the gizmo work.
Interesting, clearly a day late and a dollar short, but interesting. Worthy of note . Perhaps some future design may have its inspiration in this, for something we’ve not yet considered.
@All
Before we muddle the airwaves with a bunch of reactionary posts and thoughts, I recommend, Just so that everyone is clear on our core technology, to please visit our Facebook (https://www.facebook.com/WaissiEngine/) and Instagram (https://www.instagram.com/waissiengine) accounts in order to understand what it is that we are working to develop. We hope to have our website up and running soon, which will provide complete insight to your questions and thoughts. That said, Our company is engaged in the development and prototyping of a new and innovative internal combustion engine, the Waissi Engine. Our engine has secured four patents and currently has an additional patent under review for 2024. The applications for our engine are numerous from AEROSPACE, UAV, LIGHT AIRCRAFT, AUTOMOBILE, TRUCK, MOTORCYCLE, MARINE, AUXILIARY POWER UNIT etc… We look forward to hearing your thoughts in the coming months as we move to DYNO testing and published metrics. Thank you Ronnie for stopping by our booth again this year, Its always good to see you. And obviously we appreciate the write-up. Talk soon.
I was in a couple of your courses while at ASU. Glad to see you’re still at it.
While the Scuderi Engine may not have been the focus of the article, those of us nerds who believe in engine tech and automotive innovation have been reading articles like these for decades.
If you want to be a reporter, then report. If you want to mention the Scuderi Engine, the SEC reports, or lawsuits…dig. Call em. Research it. Where’d it all go? Otherwise, if you’re just interested in superficial “oh, look at this new shiny thing” stories, you may as well just write about Maybelline.
“Maybelline, why can’t you be true?”
And Rob. I believe in you. I’m all for the innovator who can prove the ICE has a place in the future. When you’re able to take on small investors, post it, and I (we) will be there.
Infinitenergy aka. ie. Some times we should realize that combustion is not the only way to achieve the pressures needed to roll a singular direction expanding cylinder through its range of motion. For example. Liquid nitrogen when released into a vacuum expands over 700 times it’s liquid particle state. And then if a person ,place, or entity utilizes the percussion of a volume rapidly accumulating a negative pressure then opened to full atmospheric pressure at 2/3 way down it’s stroke / range of motion. The positive pressure when overfilling for that brief second prior to reaching the 7/8 of stroke would allow for accumulate in a inline 6 of 300 ci 50 total cubic inch/ cylinder a max potential of 14.xxxx psi x 30 cubic inch single directional relief by motion senario stroke engine of requiring no spark no fuel fired. However a little drop of liquid nitrogen properly timed would boost higher. Pressure s as d more torque when needed. But my math tells me? I’ll be surprised if any one can follow the inertia of such a 2 stroke device. If so eone does. My e mail is infinitenergy79@gmail.com
This appears to be a great potential for alternative fuel sources; particularly Hydrogen. It’s my hope that this ICE can be developed with Fuel Cells to reduce overall emissions from manufacturing both the Battery and ICE industries. The current Battery processing waste, from mining through finished product to disposal is amazingly atrocious. Once alternative fuel infrastructure is solved, this engine design looks to be another way to eliminate multiple ICE manufacturing processes because of reduced components used to reduce the requirements using much more powerful ICEs for similar results. All the best to these fellows to get this up and manufactured.
Best of luck. Please keep me updated on the progress of this engine development.
Thank you Ron Kessler
Excellent description.
I would love to see follow-ups.
BTW, I am a battery engineer, and I would love to synergize my technology with this type of engine.
I see a lot of potential there. The vibration looks to be the most significant drawback. Both pistons are moving in the same direction at all times along with their connecting piece, unable to cancel any of it out as in a conventional opposed engine. I wonder, how about two complete engines, fastened concentrically along their bores, and timed opposite one another? An extremely long contraption but so much smoother. Fascinating discussion for this armchair designer, I wish them continued improvements and success!
If you check out the first photograph, it’s a four-cylinder and the cylinders are operating in different planes. I think this takes care of the issue which you mention.