6 Tools We Hate to Reach For
Most of us treasure the time we spend working on projects. The mental flow state that comes with forcing our minds to mellow out and focus on solely the task at hand can be therapeutic—in the right situation. Every bright light casts a shadow, and every garage holds some tools we hope never to use.
These are the devices that mean our time in the garage is not going well. The steel canaries in the horsepower mine. Projects go sideways just as many times as they go flawlessly, and many of us have various gadgets that serve no purpose until all else has failed.
Here are a few tools that we love to have but hate to reach for.
Tool #1: Tap set
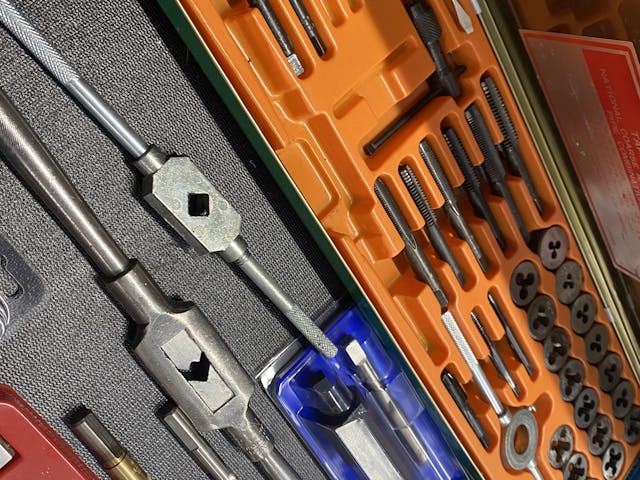
More often than not, forming—or re-forming—threads in a part or piece follows the destruction of those spiraling channels. You’ve probably broken a piece of hardware—or, worst of all, an easy-out. Toss in the fact that taps are very hard, and thus brittle, and you have a very volatile evening of work ahead of you.
When used properly and carefully, a tap set can be a reset button on the life of a part. Even drilling up one size and tapping so that a fastener can have appropriate holding power may be better than replacing the fastener. Sometimes it’s all about perspective.
Tool #2: Spring compressors
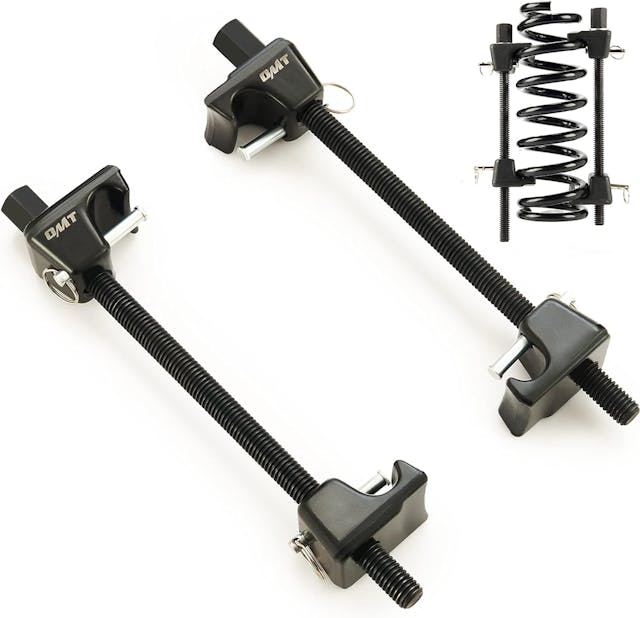
The sudden release of potential energy describes a lot of scenarios: The explosion of a firecracker, the expansion of an airbag, and the release of a compressed spring. Each of those can have serious long-term health effects if it happens too close to your person. There are two groups of people who work on automotive suspension: those who are uncomfortable, and those who ignore the forces at play.
Springs and suspension still need to be serviced, though. Carefully inspect and service spring compressors before using them to ensure there is no damage or problems that might pop up. Sometimes just that bit of added confidence is enough to soften the fear factor.
Tool #3: Camshaft locker
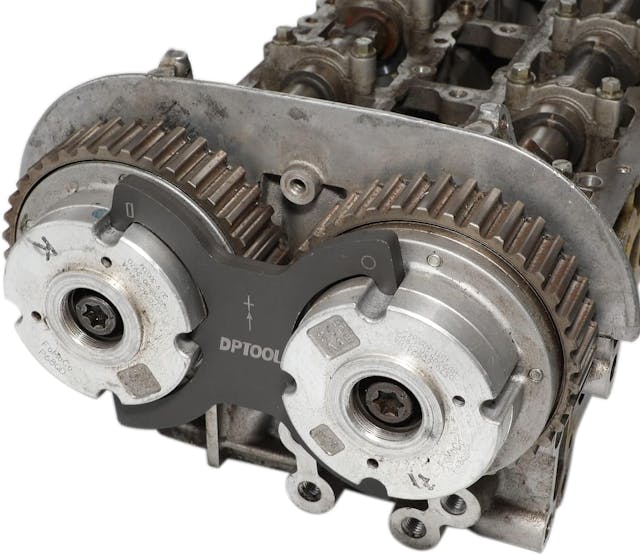
It’s not that this tool is so bad; it’s that the consequences of human error when using it are high enough to make us uneasy. Variable camshaft timing has unlocked horsepower that comes with minimal compromises in fuel economy and also drivability. Unfortunately, the technology also makes for more complicated service; replacing a timing chain or belt often requires careful alignment of multiple points while also holding tensioners and gears in proper orientation. The job can be fairly painless, but that doesn’t mean it’s fun.
Tool #4: Air hammer
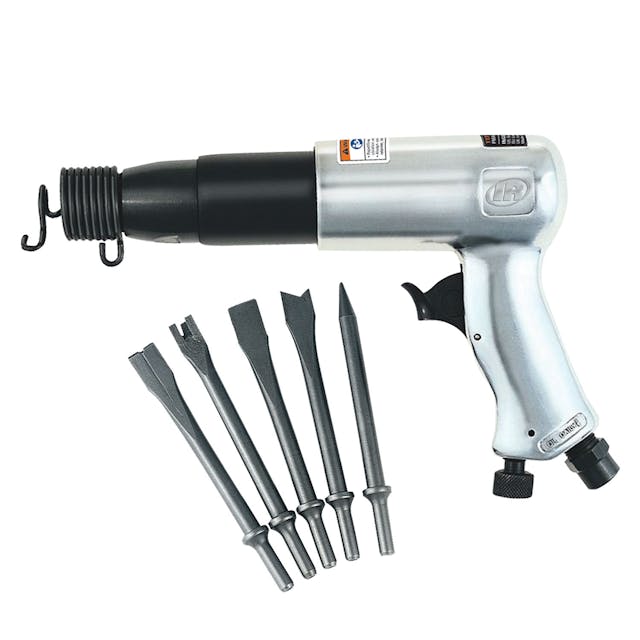
Percussive force breaks the bonds of rust, and it hammers eardrums just as thoroughly. The compromise can often be easily overcome with a good set of earplugs or over-the-ear muffs, but using an air hammer still isn’t a pleasurable experience. Compared to using the torch, and the chance of lighting everything on fire, it is the lesser of two evils. We don’t love you, air hammer, but, after all these years, we haven’t let you leave the toolbox.
Tool #5: Impact driver
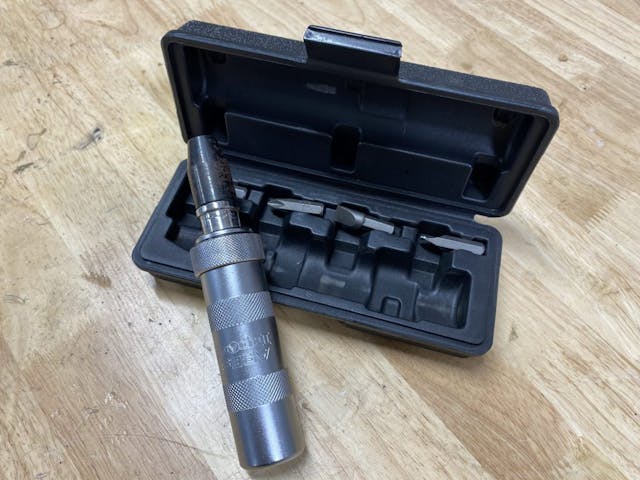
Stripped hardware is the bane of any DIYer’s existence. Even with the proper tools and experience to handle stripped screws and bolts, we don’t want to spend the limited time we have in the garage dealing with them. The combination of driving and turning force delivered by an impact screwdriver can take quickly solve the problem of a partially stripped screw. It can also result in hitting your wrist with a hammer, or create an even bigger problem by snapping a bolt off where you can’t grab it. Often, our opinion of an impact screwdriver is based on how well it worked the last time we used it.
Tool #6: The Big Hammer
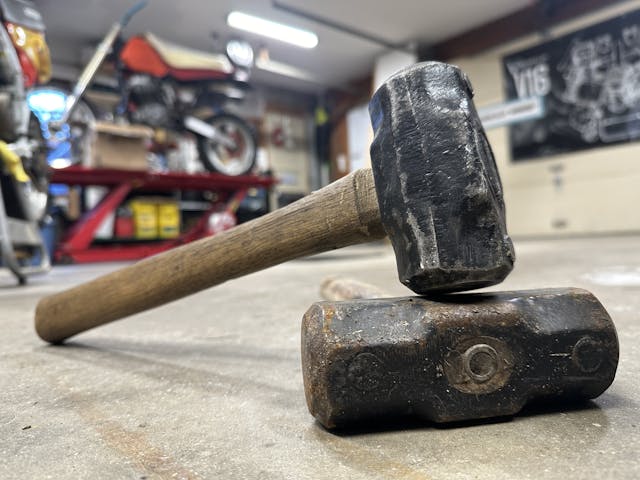
You know the one. The handle is slightly stained, and the face features a few chips from that one time you got a little carried away on that ball joint. You probably started addressing the problem at hand with a couple of smaller hammers and, when you realized that things were not going your way, and that you were tired of talking nice, opened the drawer to grab The Big Hammer.
This list is all a matter of opinion and personal experience, so we may have missed one or two here. If you’ve got a tool you avoid reaching for but might not be able to put a finger on why, leave a comment. Consider it an unofficial survey.
***
Check out the Hagerty Media homepage so you don’t miss a single story, or better yet, bookmark it. To get our best stories delivered right to your inbox, subscribe to our newsletters.
2 items in my mind, but some may disagree they are technically tools: anti-seize, not because it is a bad tool, but because it somehow miraculously gets on everything; or (the biggest tool in the arsenal) calling my buddy who is a professional mechanic to borrow his expertise or shop (or both), it gets the job done when I find myself over my head, but I invariably end up owing a big favor.
The big hammer reminds me of when I was apprenticing, I was installing some stellite bushings for a project we were doing for Stelco Lake Erie works. Being an apprentice and this being a prototype job I went easy and used the little hammer to tap in the bushings which were not co-operating. Along comes the plant manager who watched for a bit, he was also an engineer and from Georgia. He then said, “Ricky you’re forcing it, get a bigger hammer”! So I get the bigger hammer, much like the one in the picture, give it one good wack and the bushing was seated! The manager then explained the big hammer gets the job done with one or two hits and that damage is usually done by repeated hits to the part. Lesson well learned! Last fall the neighbors son was doing the back brakes on his pickup and had trouble getting the drums off using a “small hammer” and drift! I quoted that engineers line and give the drum a good wack with that same hammer. The son had the same look I did 45 years ago!
I inherited all my dad’s hammers when he passed. I have about 27 by now…
Anything that has anything to do with body work or paint. Sandpaper, grinders, rust converter, dent removal tools, etc. I like to make things go fast and fix them when they break but still can’t and don’t make things pretty
Oh, this has been fun to read! Thank you contributors.
I wrench on my (past and present) BMWs and a Benz, 1982-2017. The big hammer, air hammer, die-grinder and dremel abrasive disks, taps, dies, ez-outs, vice grips, channel locks, monkey (stilson?) wrenches, ball joint splitter forks, wood splitting wedges, oxyacetylene, propane, mapp torches, extensions, etc. are our friends that allow forward progress in the face of adversity in the garage…
I didn’t see the nutcracker (wedge driven by a big screw in a metal loop) but maybe I missed it. Also, the cousin of the helicoil, the PEM nut and PEM stud. A nut or stud that presses into a metal piece, usually sheet metal but can be thick.
In the end, however, my favorite loved-and-hated tools are the ones I make. These, usually, to extract and install suspension bushings and parts. From ball-joints, control arms, rear thrust bearings, through-the-shock-hole spring compressor (rear 525 E39 wagon), disk pullers, spline axle end pushers, rear carrier bushings, etc., The work a lot like a hydraulic press (and indeed the bottle jack can be put to use between 2 big plates held together with threaded rods to fashion one). However they can be deployed for parts on-car, go through holes in bushings, etc. I have made many. Armed with asst. lengths and sizes of hardened threaded rods, big nuts, grease, lots of washers, pieces of pipe, iron pipe fittings, ranges of aluminum plate from 1/4″ to 1-1/2″ thick, band saw, drill press, metal blade in the table saw, grinders, etc., large sockets, you get the idea. On a branch of this home-brewed tool tree, are modified standard tools. A wrench ground thin, notches put into sockets, sockets welded together, combination wrench arms and screwdrivers heated and bent… Yes there are often rent-able or purchase-able tools, and I do have some, but mostly it is part of the challenge and satisfaction to make these gizmos.
The tool I really fear is the engine/suspension hydraulic table needed to drop the GLS 63 front suspension/engine/transmission assembly. That will be a test of character. Darn it (!) if I will be paying the dealer to do this for the better part of $8K to change or service the turbos, or any of a pile of things on this beast. (what I need is a look at the one benz uses so I can make the cradle!)
On the topic of spring compressors. 1) If possible, always do it out of the car. Yes, it is often not possible, or a great pain to pull out the strut, but it is so much easier and safer to do outside of the car. 2. Once, using the side threaded compressor type (pictured in the 6 tool story) without the little safety pins shown in the picture, they both spin around to one side of the spring leaving this arched angry spring for me to gingerly release. I may have roped it, I may have had it in the bench vise, I don’t remember. But unless there is some compelling reason to do so, I will never use those again. H-F has the hinged gizmo with safety pins, it does the trick, safely and quickly.
One side note on coil springs: The manufacturers (at least those from the fatherland) have all moved from big fat steel wire to a much thinner high-tensile alloy. This saves weight (OK, some of it effectively unsprung I guess!), however this material does not have the longevity of the fat wire springs of days gone by (how often did one used to have to service broken coil springs?). I have changed a fair number of failed coil springs on 10-15-20 year old BMWs. It is my theory that corrosion likely has a lot to do with weakening the high-strung lack-of-yield-headroom newer coils. Being from the northeast, that winter road-salt water gets under the spring’s coating (powder, ?) at a nick or blemish, finds/makes itself a little crack, and from there the weakened wire snaps. So, the upshot of all this is to be careful of that coating when replacing coil springs. (fun fact: coil springs work by twisting the wire as they are compressed. That is where/how the energy is stored.)
Happy hammering, use the abrasive wheel, even the little one on the dremel tool, to split the most stubborn of nuts. They don’t put up much of a fight when they are in 2 pieces!
-Hugh
kyle, thanx for the article. and thanx to everyone and their comments. although most everything has been said (and if bored), here’s some more reading material…
great words on a bumper sticker: “if it jambs, force it. if it breaks, it needed a new one.”
a boss from years ago called his short handled baby sledge hammer, little bam-bam.
i don’t have a problem reaching for any tool other than maybe the door knob to the garage door. it’s the job itself that i might not like to do, which is seldom.
last summer i attempted to remove 2 broken exhaust manifold studs thru the inside wheel well on my old nissan truck. the fancy left-handed drill bit & extractor worked ok on the first stud. on the 2nd, well, the extractor broke off (my fault – should’ve backed off much sooner). concluding that rather small drill bits (for drilling around the extractor), a die grinder with carbide tipped cutter, patience with finesse, and more room was needed, i removed the engine. although the cutter didn’t become dull, it took a looong time to get it out. yup, i had to install 2 heli-coils, and it took several hours of patient work. being repaired, and properly, it was worth the time. i looked forward to use some proper tools others might not like reaching for. to sum it up, here’s a famous quote: “there is nothing either good or bad, but thinking makes it so.”
a couple weeks ago i replaced both rear coil springs and lower outer control arm bushings on a 2000 benz c-class, using a spring compressor mentioned earlier. there’s one or two steps i’m a little uneasy. but, following common sense safety procedures i’ve been taught and learned on my own over the years, i’m ok performing this job. same applies with the bushings where i ended up using an air hammer. patience goes a long way.
had to use a tap set on the stabilizer bushing bolt on a roadmaster wagon whose original bolt on one part had stripped out. was a pita because i didn’t have a lift so doing it from underneath in a cramped spot was tough. first and last time i’ve had to use one… so far.
When I was in college, I worked at a tool and diemakers shop. We made all kinds of unusual things. One day I was tasked with threading holes in an aluminum housing for a firing computer for an MBT (a tank).
after a while, I got careless and snapped off a tap in one of the holes. After a minute or two, (to build up the nerve) I spoke to the foreman and owned up to my mistake. Rather than fire me (which I fully expected) he said, “not a problem.”
He took me over to the EDM (Electrical Discharge Machine) I had no idea a machine like that existed.
The foreman put a piece of copper wire in the chuck, aligned everything, and hit the start button.
The tank around the part filled with oil and the only way I can describe it is, a controlled lightning bolt erupted from the machine below the oil and BURNED its way through the offending broken tap.
At that moment I fell in love with that machine.