6 Tools We Hate to Reach For
Most of us treasure the time we spend working on projects. The mental flow state that comes with forcing our minds to mellow out and focus on solely the task at hand can be therapeutic—in the right situation. Every bright light casts a shadow, and every garage holds some tools we hope never to use.
These are the devices that mean our time in the garage is not going well. The steel canaries in the horsepower mine. Projects go sideways just as many times as they go flawlessly, and many of us have various gadgets that serve no purpose until all else has failed.
Here are a few tools that we love to have but hate to reach for.
Tool #1: Tap set
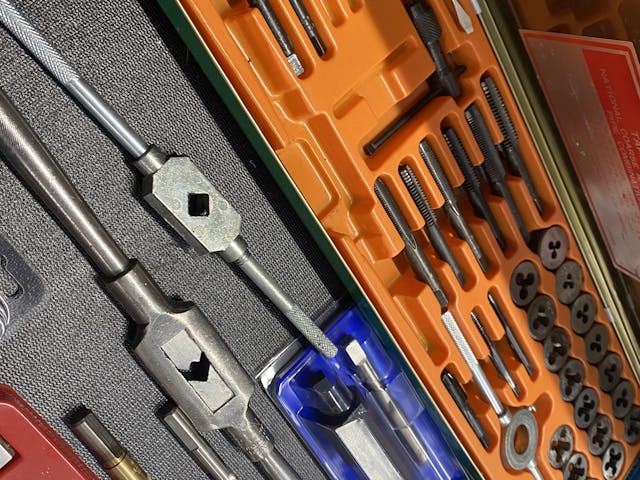
More often than not, forming—or re-forming—threads in a part or piece follows the destruction of those spiraling channels. You’ve probably broken a piece of hardware—or, worst of all, an easy-out. Toss in the fact that taps are very hard, and thus brittle, and you have a very volatile evening of work ahead of you.
When used properly and carefully, a tap set can be a reset button on the life of a part. Even drilling up one size and tapping so that a fastener can have appropriate holding power may be better than replacing the fastener. Sometimes it’s all about perspective.
Tool #2: Spring compressors
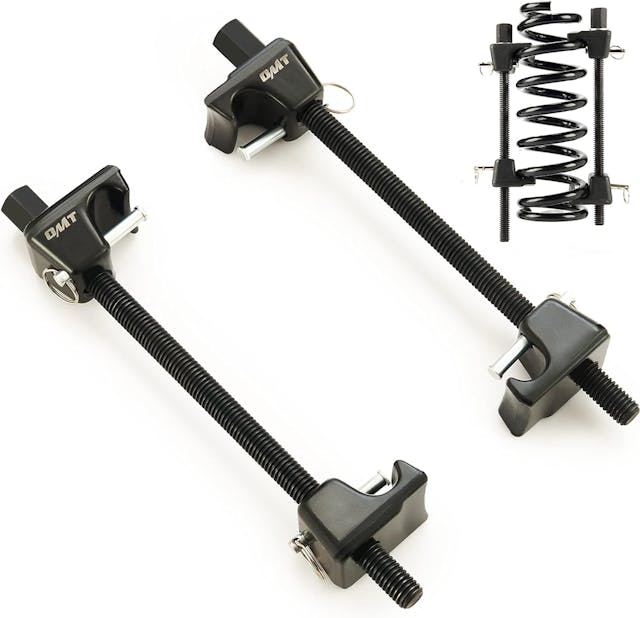
The sudden release of potential energy describes a lot of scenarios: The explosion of a firecracker, the expansion of an airbag, and the release of a compressed spring. Each of those can have serious long-term health effects if it happens too close to your person. There are two groups of people who work on automotive suspension: those who are uncomfortable, and those who ignore the forces at play.
Springs and suspension still need to be serviced, though. Carefully inspect and service spring compressors before using them to ensure there is no damage or problems that might pop up. Sometimes just that bit of added confidence is enough to soften the fear factor.
Tool #3: Camshaft locker
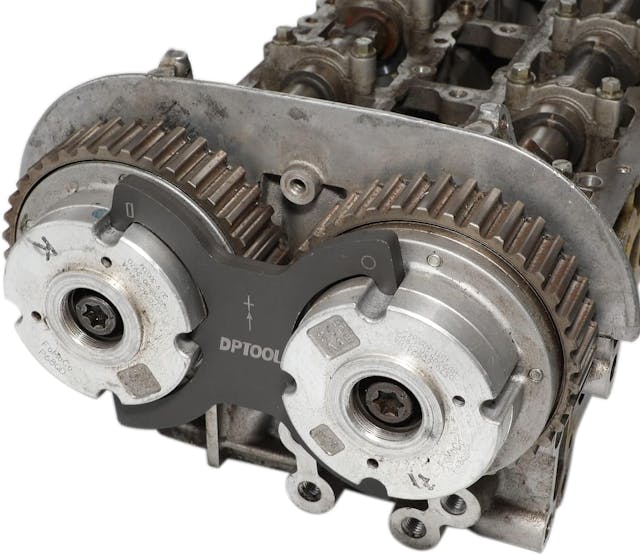
It’s not that this tool is so bad; it’s that the consequences of human error when using it are high enough to make us uneasy. Variable camshaft timing has unlocked horsepower that comes with minimal compromises in fuel economy and also drivability. Unfortunately, the technology also makes for more complicated service; replacing a timing chain or belt often requires careful alignment of multiple points while also holding tensioners and gears in proper orientation. The job can be fairly painless, but that doesn’t mean it’s fun.
Tool #4: Air hammer
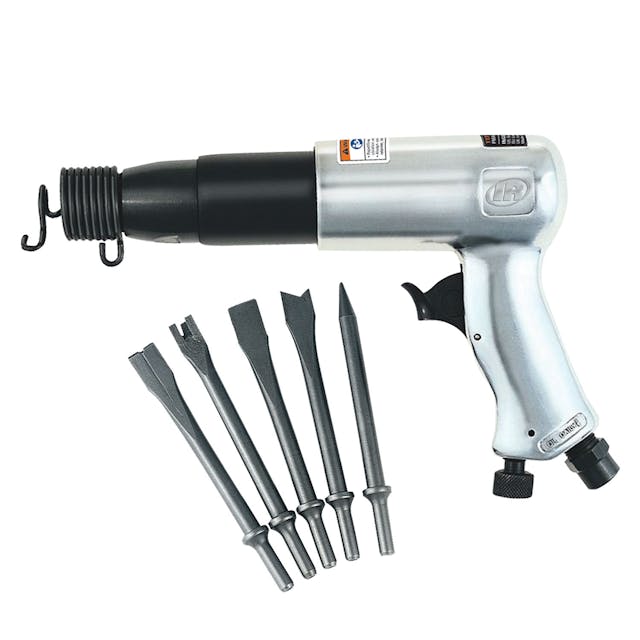
Percussive force breaks the bonds of rust, and it hammers eardrums just as thoroughly. The compromise can often be easily overcome with a good set of earplugs or over-the-ear muffs, but using an air hammer still isn’t a pleasurable experience. Compared to using the torch, and the chance of lighting everything on fire, it is the lesser of two evils. We don’t love you, air hammer, but, after all these years, we haven’t let you leave the toolbox.
Tool #5: Impact driver
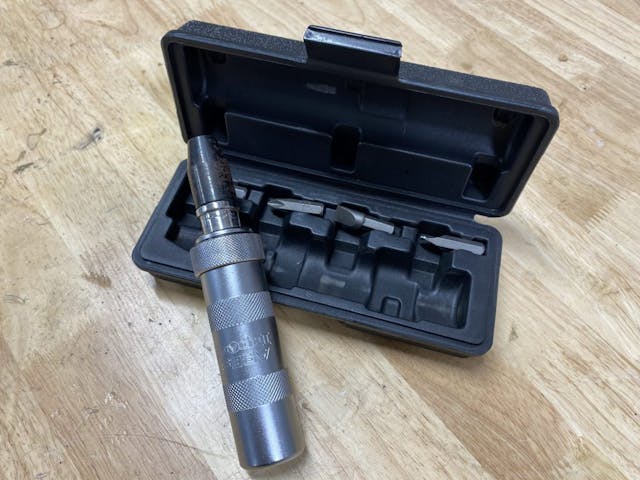
Stripped hardware is the bane of any DIYer’s existence. Even with the proper tools and experience to handle stripped screws and bolts, we don’t want to spend the limited time we have in the garage dealing with them. The combination of driving and turning force delivered by an impact screwdriver can take quickly solve the problem of a partially stripped screw. It can also result in hitting your wrist with a hammer, or create an even bigger problem by snapping a bolt off where you can’t grab it. Often, our opinion of an impact screwdriver is based on how well it worked the last time we used it.
Tool #6: The Big Hammer
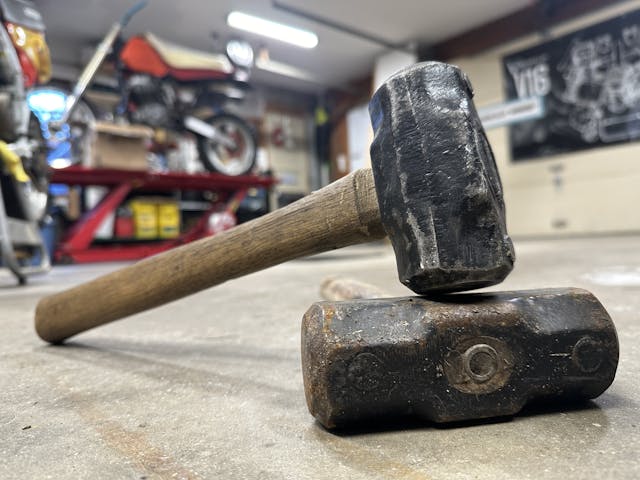
You know the one. The handle is slightly stained, and the face features a few chips from that one time you got a little carried away on that ball joint. You probably started addressing the problem at hand with a couple of smaller hammers and, when you realized that things were not going your way, and that you were tired of talking nice, opened the drawer to grab The Big Hammer.
This list is all a matter of opinion and personal experience, so we may have missed one or two here. If you’ve got a tool you avoid reaching for but might not be able to put a finger on why, leave a comment. Consider it an unofficial survey.
***
Check out the Hagerty Media homepage so you don’t miss a single story, or better yet, bookmark it. To get our best stories delivered right to your inbox, subscribe to our newsletters.
To be honest I have favorites and some not favorite tools.
But the one I hate to use is the one I need and don’t have. Life can be tough if you run into something you need to fix and you know there is a tool for it but it is not one that is in your box.
Note this happens often at 12:30 AM and you have a race the next day.
To be honest I do not have all the trick tools but I find it funny how I will buy a trick tool and all of a sudden I need it and get to use it. I have had more wins vs losses.
I know it is not going well when I get out the oxy-acetylene torch or even worse the cutting torch. It is bad day when vice grips are used to remove a broken screw.
You got that right! I was going to post that they left off the torch and vice grips but you beat me to it. A broken tap extractor is another tool you don’t want to reach for….
Drum brake pliers. Especially the cheap ones you buy off Amazon (even though you KNOW better) since “I’ll only be using them once”.
I heat the area around the center axle protrusion lightly with a propane torch & it always pops free.
“And it always pops free” , What planet are you from ??
Rail42. Good answer. Drums seldom pop free with that little amount of heat. Too bad all drums aren’t thicker and with threaded holes so bolts could push the drum off the axle like a few are.
My 48 Fiat Topolino has those threaded brake drum holes–makes drum removal a snap!
if you sit there and use about 10 bottles of propane it will work most likely.
i think ron was referring to the drum brake pliers that remove the brake lining springs
larryc is Obviously not from the rust belt !
There you’ll need ALL the ” Dreaded Tools ” we hate to reach for and then some,,,, LOL
Note all those listed above are a blessing if you really need them to finish a job.
Had a friend inMemphis named Arnold Bonner back in my drag racing days in the 60s. He had a big sledge that was his last resort. He’d say “I’ve tried three hammers, I guess I’ll have go get ‘Old Monday’!
The Persuader!
They were called speed wrenches at Sears Auto Center in the 70’s.
If the hammer you’re using doesn’t do the job, what do you do? Get a bigger hammer!
“don’t force it, get a bigger hammer”
Hammer of Thor
For those particularly stubborn jobs I reach for what I lovingly call the “BFH” or ” Big Bubba” , a big old post maul .
When it does come out you’d darn well better be Thor though , it weighs in @ 40 lbs with a 18″ handle and it’s best not to miss with it .
It is quieter than a air hammer though , unless you miss, then the cussing is WAY LOUDER than any air hammer known to man .
Wanna ask me how I know,,,,? LOL
People tend to scatter when that beast comes out , For Sure and it has a bad reputation around my shop.
The only time the vice grips come out are when things are going badly
A wise policy, for sure. Vice grips are a crude expedient and should indeed be a tool of last resort. Problem for me is that, all too often, more elegant solutions to my problem are unavailable in the moment.
And there you have it: elegant solutions and in the moment are mutually exclusive.
Electric impact guns can save the day or ruin it! I’m especially careful with my 1/2 drive or 3/8 and have had very few bad instances as they have saved the day or into the night!
100%
Even looking at them i hear my dad’s admonishing words about the right tool for the job!
With you on that one Ringo. I call mine bertha
I was surprised to not see them on this list.
I was going to say “the 10mm wrench I dropped but didn’t hear hit the ground.” God knows what’ll busy your knuckles when you reach for that tool.
I agree with the big hammer (BFH). Also hate to break out any torch for a repair be it propane, oxy-acetylene, or the plasma torch. Usually means something is broken, seized, or totally corroded.
Totally agree any flame making tool should be in the list. You don’t know if it’s going to work and you must act quickly after heating because the parts cool fast -and worst of all, you can easily destroy something (like a CV boot) that you didn’t notice was right behind the part you’re heating!
How many of you have seen that chemical on TV called Superzilla? It does indeed loosen rust. I like it so much; my second purchase was the gallon size. There are no harsh chemicals and it’ll clean as well as de-rust nuts, bolts and more.
The oxy-acetylene torch, the plasma torch, or a MIG welder with an appropriately sized bolt or nut should be on the list. All three have saved me over the years when a corroded threads are to blame. How do you avoid this? Heat stuck or suspect threaded fasteners with an induction heater first. No fire or sparks and the chance of damaging thermally sensitive components nearby are nil. It may take a minute, but a busted stud can take orders of magnitude more time and effort than the time it takes to heat with an induction tool.
I got a 25lb sledge. His name is Burt and we call him “The Persuader”. If Burt comes out somethings gonna break or it’s already broke.
Last time Burt cut loose was on a drive axle shaft in a front wheel bearing. It wasn’t pretty. The axle shaft did not survive. The wheel bearing was already terminal. God bless Burt.
I’ve got a big sledge too
Too funny, I have a sledge and I call it “The persuader” I got that name (and the hammer) from my father. I can tell you how many times I have missed hitting a chisel with it and smashed the side of my hand. Then I call it a lot of things.
Hold chisels with vise grips and keep your hands safe.
best use for vice grips.
As a retired master mechanic, I couldn’t agree more. I would be happy to use any of listed tools. A lifetime of using one and I never warmed up to the blue wrench.
Punny, that one!! The “blue point wrench” comes in handy a LOT when working on “old iron” up here in the rust belt. Also means you fon’t need the “persuader” as often – ir the only tool that ever did me serious damsge – that nasty air chisel/air hammer. I have a finger that is still sensitive to cold and about 30% wider than it’s mirror image from a run-in with the air hammer over 40 years ago. Always had a lot of respect for it, but my respect for it doubled or quadrupled that day. Turned the end of one finger to bone meal, and broke the one next to it into 3 pieces. Thankfully missed the joint but earned me 8 weeks off work and another 8 or 12 of light duty.
What’s a blue wrench?
It is a popular slang name for an oxy-acetylene torch. The cone of the flame near the tip of the torch is blue when dialing in the proper gas mixture.
Two grade 8 bolts and nuts solved a front wheel bearing problem that the BFH couldn’t budge. But after learning the 2-hammer rotor removal trick I’m no longer intimidated by brake jobs.
The screw/bolt extractors often called EZ-Outs . There is nothing easy about them and if you have to use them a screw/bolt has broken off while attempting to remove it or over tightening it . Or in the case of my 71 Chevelle SS(summer of 75)the engine shifted due to a broken/worn motor mount and the clutch linkage pivot bolt broke off flush in the engine block necessitating engine removal to drill a hole in it to use said EZ-Out . I’m also more than familiar with impact drivers since early 70s Japanese motorcycles used Phillips head screws everywhere and one of those was a must have in your toolbox .
I think anything in the bolt extraction/thread repair region is evidence things didn’t go according to plan
Indeed.
I agree with TG. I had expected broken tap extractors to be at the top of the list; not taps & dies. Similarly, those left-handed extractors that sometimes work on sheared-off bolts, but usually break, leaving a bit of hardened steel in the middle of your sheared-off bolt.
As hyperv6 wrote above, the tools that you did list might be heavy-duty, but they’re also a blessing when you really need them.
I was also surprised spiral extractors were not at the top of the list!
Taps and dies are no problem at all. Just cleaning up the thread so it runs smooth! But if I have to go for the extractor my day has already gone sideways.
And, speaking honestly, my success rate with extractors is only about 25%. The rest of the time it’s so seized up that I have to drill it out and probably oversize it. (Don’t care for helicoils)
Yeppers, have broken bolts in a head from PO, and now one with an extractor broken in it. That was with PB blaster in it and met gas tourch.
Nothing more true.
Honda, Yammer-Hammer, and others called them “cheese head” screws… aptly named.
I wrenched on my Honda Enduro bike in the 80’s and quickly got an impact driver. I used it often and it is still in the tool box! 🙂
Yup. There are things where I simply go right to it, as it is the “easy button”. The screws which hold brake rotors in place would be a prime example.
Yeah, Back in those days we never heard of JIS.
The Japanese Phillips head is actually JIS. JIS stands for Japanese Industrial Standard. They generally have a dot stamped on the head between the “legs” of the cross. And take the “generally” literally. But just about any “Phillips” head on a Japanese made vehicle is JIS. Don’t quote me on that, again “generally speaking”… the lead angle and depth of the point of the driver are just different enough that a “normal” Phillips doesn’t seat “perfectly” and POOF stripped head. I believe you can get JIS bits and/or drivers at Harbor Freight. I got mine from Amazon. Note the JIS bits are different sizes much like Phillips 1,2,3 etc.
Yeah, I thought it was a BS story until I got the bits and sure enough, they engaged into the screw tighter than a “insert your favorite term here”…
Since I’ve got them bits, haven’t stripped a screw head on my Japanese bikes and cars. Oh yeah, get bits and drivers as the bits can be used in an impact driver. But not that we like using/needing them per this fine article.
High quality JIS Phillips screwdrivers are made by Vessel Tools. Look for the “Megadora” line. Best screwdrivers I’ve ever used. Better than Snap-on. The nice thing about JIS Phillips screwdrivers is they also fit and hold SAE Phillips screws better than a common SAE driver. Oh, and Vessel also makes excellent JIS Phillips (and Robertson square drive screwdriver bits for your drill/driver and impact driver.
when you use harbor freight quality,as in taps,extractors,specialty knock offs,you will pay the price!
That impact driver became a stapple in my toolbox too when I owned a Honda 550. It seems a great feat of strength was carefully needed when servicing that beauty.
I agree whole heartedly about EZ outs. They are usually anything but easy for me. Really makes it a bad day when you drill into a broken off bolt and then break the EZ-Out off inside the bolt. Maybe I am the only one this has happened to.
The sheer amount of times I’ve had to find a way to remove a broken off EZ Out would amaze you.
And…what was your solution. Think I need someone with a mig welder to weld another bolt and nut to it?
I have a set of ez outs with 3 missing, a test time today to the times they didn’t work ….. hate the damn things.
The EZ out should be #1 on the list.
Japan has their own Phillips spec it’s JIS or Japanese industrial standard. Bad news you have likely been using the wrong bits or drivers your entire life. Believe it or not float bowl screws come right out with JIS bits. The screws have a dot to signify JIS.
I sold tools a lifetime ago, and therefore was lucky to have access to hard to find tools. And a slightly misguided love of older than me cars. I have a set of fluted extractors. They have worked well when I screwed up (!)
I could never get spiral extractors to work
The Japanese do not use Phillips head, they are JIS or Japanese Industrial Standard. If you look at the slots in the head they are slightly off-set. Start with the right driver and there are fewer problems. Also, sometimes I start with the impact screwdriver to break it loose. I got a set of JIS years ago and it was well worth it.
They are called EZ outs because they only get the easy ones out.
Ah, but they aren’t actually Phillips head, they are JIS and take a screwdriver made specifically for them.
Wife: you bought another tool ?
Me: yes dear I needed it😂
I always thought the EZ-Out was the most cruelly named tool. EZ it’s not and while your using it, Out is only one theoretical possibility. I also get mild PTS with the smell of WD-40.
“I’m also more than familiar with impact drivers since early 70s Japanese motorcycles used Phillips head screws everywhere”… I hate to be the one to tell you this, but… those were NOT Phillips head screws. That was your problem.
Ez-break is more like it. I can’t tell you how many “Easy Outs” I’ve broken and have to get them “hard out.”
The BFH and impact driver are go-tos in my shop. The trick with the impact driver is to use it BEFORE you booger the screw all up
In my Diesel mechanicing days, the impact driver was a banned tool in the shop I spent most of my career in. Makes you appreciate the BFH that much more
I note the missing taps in the orange tray of the Harbor Freight tap and die set – mine is identical and missing about quadruple that amount. Bought it years ago as an impulse “cheap-o” buy. Then, after breaking all the ones I needed, I finally wised up and bought a more robust (and expensive) set. Broke two of them the first time I used them…
Sharp eye, but that’s not a set from the Hazard Fraught. It’s older than that, came from the basement of my grandparents home when it was cleaned out a couple decades ago. They are about the same quality though. Cheap tools have been around forever. Now I buy what I need individually from trusted sources.
And, there are different taps for different applications. Hand taps have a long taper. Plug taps have shorter taper, and are designed to be used with a power drill. Bottom taps have almost no taper ( maybe one or two threads) and are made for blind holes which must be threaded “to the bottom”. I was a tool and die maker, and this information, sometimes, was learned the hard way.
I agree, there’s a lot of technique when hand tapping. I’ve snapped my share. Correct tap drills and tapping fluid are essentials.
Just remember when you use a tap , oil is your friend – use liberally. And follow to the letter, the recommended drill size befor tapping – it is printed on the tap …..
Never broken a single one, Andy when reassembling any part I have painted, or it has been out of use for a while I run a tap through each screw hole.
Note often most unfavorite tools are the ones often not used properly or for the right reason. They screw something up or they damage the part.
Like a hammer it can be used properly to loosen something or used to hard to break something.
The difference it the mechanic touch as one teacher taught me.
I have really come to discover the air hammer for many uses. I work on a lot of hotrod GM trucks, so frame rivets, ball joints, A-arm bushings, you betcha. Also, a great addition is the hammer head bits for air hammers. lotsa uses with that. Also, with a chisel bit, you can use it as a jackhammer for breaking up small concrete jobs and landscape brickwork. I literally have the one pictured.
My medium BFH, I had to weld a steel handle on it after the first 2 broke. It’s been on there the better part of 20 years. My favorite BFH is a 10 pound sledge on a standard hammer handle that came from my wife’s grandfather. Great for getting suspensions apart.
We also have to mention my favorite tool, the cutoff wheel.
“Just because it’s fairly painless, doesn’t mean it’s fun” – Great line!
I recently had to remove a round concrete cover on my patio to get to the drain for a slow drain issue. That cover was almost cemented in so here comes the air hammer chisel. Once off, I used it some more to clean up the bad concrete that stuck to the side of the hole. Now, the cover is easy to remove, and I hope it stays that way. Thye lesson learned is that dirt and other stuff works its way into the cover and sort of “cements” itself in. I have two of these covers in the back of my property and I can use them for an RV dump.
The air chisel saved my butt as the steel tube on the shock eye rusted to the upper shock stud, which was not removable. “luckily” the rubber came off the tube so i could get the shock out of the way, but as I recall a pry bar, maybe a small pickle fork and some choice words to get the shock off and out of the way. So had to use the chisel to slit the tube, sprayed the crap out of it with penetrating oil and used the chisel in the slit to rotate the tube and “sliding” it off the stud. The “hey, let’s replace the shocks this morning” turned out to be another harrowing tale of DIY
Your writing always makes me smile. The one tool I would add to the dreaded tool list is Vice Grips. They have destroyed many bolts and nuts over the years but are sometimes the best “tool of last resort.”
My least favorite is the long pipe that goes over a breaker bar handle to remove an over-torqued or rusty bolt/nut. Usually ends up with a stripped/snapped head or a broken breaker bar.
I have to agree on the long pipe. To add to the problem of a broken bolt or breaker bar is the fear of where I’m going to land once all h**l breaks loose.
I learned not to have your head inside the wheel well when your working with the “optional pipe handle”.
I had dual rear wheels off of a class 8 drive axle to access a shock bolt. Needless to say the pipe extension on a 3/4 drive ratchet slipped and I kissed the one hub spoke. Good for 6 stitches down the top of my nose.
A pal was struggling with an extender on a very large pipe wrench, removing some suspension part on my 3/4 ton Dodge truck when the pipe wrench broke. He woke up about a half hour later, lying on his garage floor. Then he finished the job and seemed ok when I picked up the truck. And so we learn.
Or damaged knuckles/fingers…
I respect, but do not fear, the spring compressors. I use them just enough to force the spings/struts out while leveraging to lower control arms.
The frustrating thing is that you almost never have the clearance to get them 180 degrees away from each other producing a leaning tower of compressed energy staring you in the face.
I use a spring compressor that was designed use on Mercedes. It telescopes thru the center of the spring. I’ve used it on the front springs of my Chevelle, my 37 Chevy that had G-body suspension and my 92 GMC. It was the only way as they all had lowering springs and there isn’t room to get a “regular” spring compressor in between the a-arms. There are plates that go between the coils and the “compressor” goes up thru the center of the spring engaging the plates and pulls the plates together compressing the spring. Still a little scary but the only solution in the cases that I needed. Certainly better than chain and a jack. Not that I know anything about that!!!! Saw that on a YouTube video. Oh wait, was there YouTube in the 60s and 70s.
In which case I use 3 compressors as close as possible to 120 degrees apart.
anyone using the cheap ass spring compressor pictured ,, I would recommend going to H/F and buying 8 pairs of vise grips ,, put one pair on either side of each block to lessen the chance of them slipping on the spring
This seems like a solid tip. thanks for sharing.
Only because I’m of Scottish/Irish decent have I NOT thrown out all the EZ Outs I have (WE never throw ANYTHING away…) but I stopped using them decades ago!
Left-hand drill bits__and a reversible drill motor__are the WAY TO GO! The drill bit (9-times out of 10) will “bite” into the remaining stud and walk it out as pretty as you please.
On that rare occasion that the remnant bolt doesn’t back itself out, well you needed the hole to proceed anyway, so nothing is lost, but DO make sure you’ve started your drilling in the center of the stud (and “guide bushings” make short work of that).
Friends don’t let friends buy cheap taps, or cheap cutting tools of any kind!
My brother and I claim sometimes that Patterson is ancient Gaelic for “packrat.”
The beloved & toolbox mandatory telecopic magnet!
Pull it out & it means you’re fishing for something you shouldn’t have dropped or shouldn’t be there… like the other half of the cheapo ez-out that just snapped and fell into the intake…
The long flexible and telescopic magnets. Save the day (or night)
They certainly have. I have occasionally lost a spark plug in one of the front cylinders of my Porsche flat four engine. These plugs are changed sight unseen. The intake manifolds were designed to make this a job by braille. The plugs always hide on top of the cylinder. The flexible magnetic wand makes it, actually, quit easy to retrieve the plug. Then of course you need to try it all over again. Its like diminishing fun that morphs into increasing anger.
I went to a hardware store and asked if they had left handed drill bits. The response was “why, don’t you just flip the switch on the drill?”… ahhh, where are the muffler bearings, right next to the blinker fluid,etc
Still looking for a metric adjustable wrench……anyone?
Left hand or right hand? They’re right next to the cans of compression at Auto Zone. LOL
😂😂😂