The easy repair that got hard: Fixing broken wires inside a harness
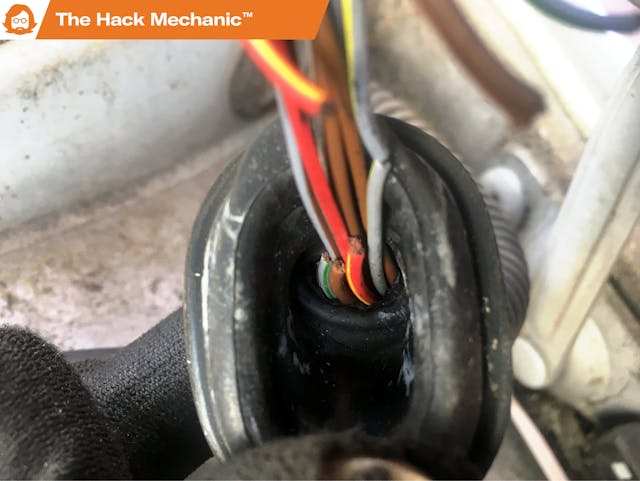
Although I have a demonstrated track record of undertaking and completing lengthy challenging projects—swapping the drivetrain and installing fuel injection in the 3.0CSi, retrofitting air conditioning into multiple cars, taking six years to rebuild the engine in the Lotus Europa—I have a particular fondness for simple “quick hit and run” repairs.
I’ve long said that in a world of intractable problems, few things are as satisfying as diagnosing a problem in a car, then fixing it. Clear beginning, clear metric for success, clear end—it really doesn’t get better than that. Routine maintenance like changing the oil doesn’t really qualify for this merit badge of satisfaction, but doing something like replacing the windshield washer pump—taking something that was driving you nuts because it wasn’t working and make it work—certainly does. Sometimes, the more trivial the thing you fix and the less time it takes to do it, the more you enjoy the end product, as that maximizes the effort-to-reward ratio.
So, with that in mind, I’d been saving an easy repair for the right moment. For the entirety of the nearly eight years I’ve owned my daily-driver 2003 BMW E39 530i stick sport, the trunk lock actuator hasn’t worked. This meant that in order to open the truck, I had to use the key; I could use neither the pop-the-trunk button above my left knee, nor trip the microswitch behind the soft rubber panel on the trunk lid itself. The trunk release on the key? Fugetaboudit. I was reminded of this every time I needed to pick up or drop off someone at the airport—I had to shut the car off, pull the keys out of the ignition, get out of the car, and walk around to the trunk to unlock it so they could get their luggage out. Actually, I was reminded of it every time I started the car, as the failure generated an incorrect “truck open” message on my dashboard.
I’ve replaced several door and trunk lock actuators over the years. The ones for the trunk are generally easier, as you don’t need to remove a door panel. Pop off an electrical connector, remove a few screws, disconnect a rod, installation is the reverse of disassembly, yadda, yadda, yadda … maybe 10 minutes, done. And the part is usually reasonably priced—for the E39, an OEM actuator costs $42, with no-brand aftermarket parts under $20. With the calendar rapidly ticking off the fall days, I decided to reward myself by eating this bit of candy. I ordered the $42 VDO actuator.

On a 60-degree day in late October, I opened up the trunk and removed the three clips holding on the access panel. On this car, the trunk latch mechanism had to come out before you could unscrew the actuator from it, but that was just three Torx-head fasteners. It took perhaps 20 minutes, not 10, for me to install the new actuator, but hey, I didn’t need to crawl under a car to do it. I was positively giddy in anticipation of the utterly trivial act of remote trunk unlocking.
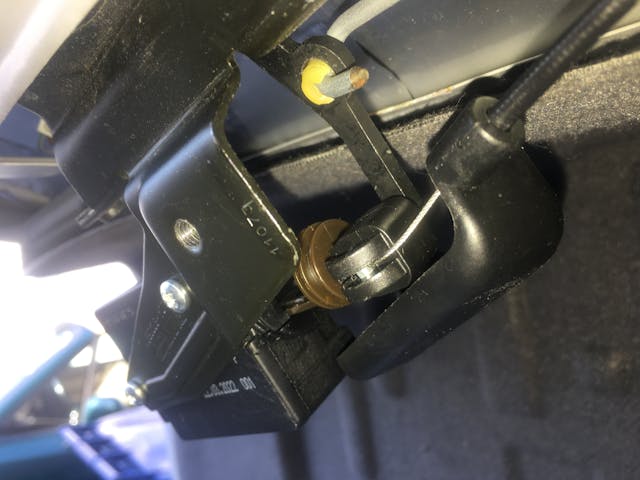
Ready to savor my easy triumph, I closed the trunk and reached for the rubber-padded microswitch on the underside of the lid.
Nothing.
I went inside the car and pushed the trunk release button under the dash.
Crickets.
Hmmmmn.
I thought that perhaps a fuse had blown. I looked at the fuse card and didn’t see one specifically for the actuator, but I saw three for the central locking system. All were fine. I did some reading and verified that the car doesn’t have a “valet mode” that disables the trunk actuator.
As I poked around inside the trunk with the lid up, the light bulb went on—that is, the one in my head. In a remarkable instance of symmetry, it was triggered by the fact that the light bulb in the trunk did not go on. My mind suddenly shot to the “trunk open” message I’ve seen on the dashboard for eight years. I realized that the actuator not working wasn’t the only issue. The problem was systemic, involving all things on the bendy little wiring harness connecting the trunk lid to the body.
Oh crap. So much for the joy-enabling quick-hit-and-run repair.

To appreciate how badly I’d gotten this wrong, I need to rewind the tape to a few months ago when I was giving a talk about automotive electrical systems at the Larz Anderson Auto Museum in Brookline, Massachusetts, and discussed the five types of circuit failures. In the talk, I said that while it’s possible for wires to break in the middle, it’s far more likely for an open circuit to be caused by a connector pulling off a component, or by a wire pulling out of the back of a connector. However, in the talk I noted that the exception is in wiring harnesses that experience a lot of flex such as those connecting doors, trunk lids, and hatches. I’d never experienced broken trunk lid wires before, but I dealt with broken wires in the hatch harness in both my BMW E39 and E46 wagons. And now that I realized that the actuator and the trunk light and the latch warning indicator all weren’t working, when I pulled back the rubber boot on the sheath leading to the trunk lid, I wasn’t surprised what I found.
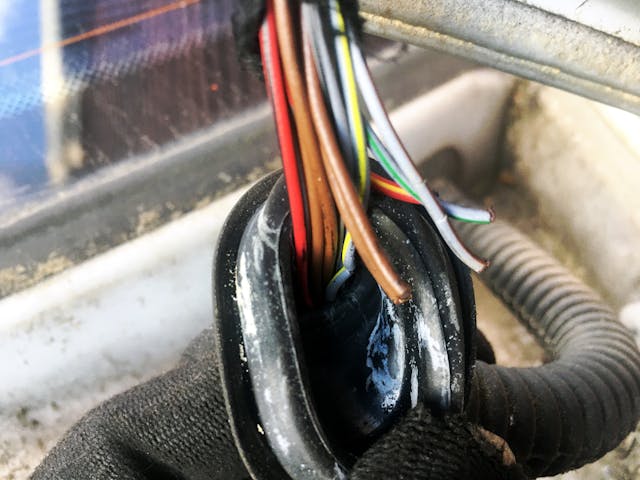
Using a small pair of scissors, I carefully slit open the rubber sheath, revealing the extent of the problem. Five wires were broken up near the top.
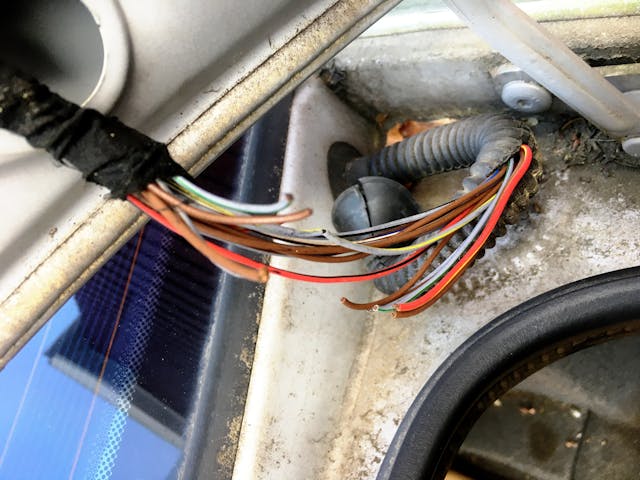
But wait! There’s more! To be certain I had fully scoped things out, I looked at the bottom end of the rubber sheath and found one more broken wire and three more whose insulation was cracked 360 degrees around.
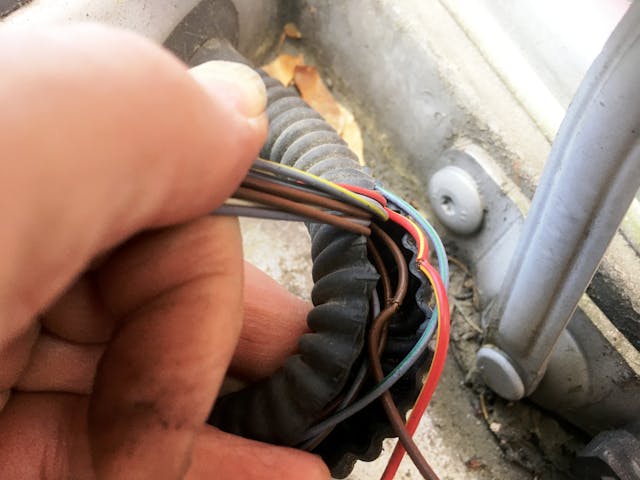
When wires are broken at a connector, you simply strip the ends and crimp on new connectors. But when they’re broken in the middle like this, they need to be spliced. That can be done by using crimp-on butt-splice connectors, by using heat-shrink solder-splice connectors, or by soldering the wires manually. I wrote about this in detail in the electrical book I wrote when I worked at Bentley Publishers, but here’s the short version.
The quickest way to repair a broken wire is by crimping a butt-splice connector between the pieces. Strip both ends, insert them into the connector, crimp, done. The advantages are speed, no soldering, and the fact that it preserves the length of the wire since you don’t need to overlap the ends. The disadvantages are the physical size of the connector, their rigidness, and lack of weatherproofing.
Heat-shrink solder-splice connectors (a piece of transparent heat-shrink tubing with an internal solder ring that melts when heat is applied) also work well. Strip both ends of the wire, insert them into the connector with both ends inside the ring of solder, and heat it with a heat gun until the solder melts. The integrated heat-shrink tubing makes the connection weathertight, as well as making it smaller in diameter than a traditional crimp-on butt-splice connector. A disadvantage is that needing to overlap the ends of the wire inside the solder ring shortens the wire slightly.
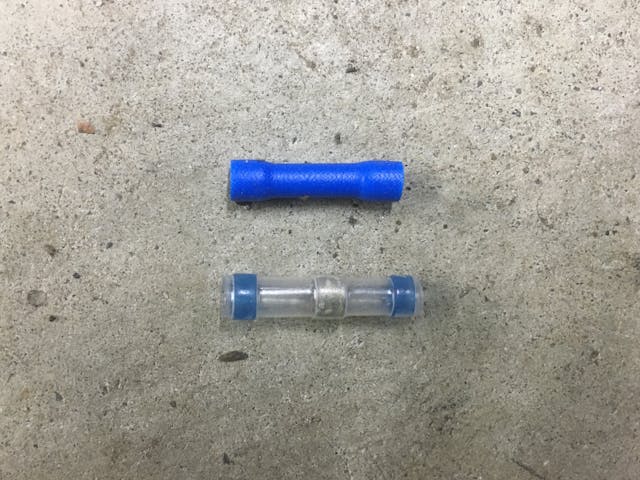
In a case like mine, where multiple wires in a harness are broken, butt-splice connectors like the one pictured above aren’t a great solution due to their physical size and rigidness. At a minimum, they’d need to be spaced out from each other and surrounded with heat-shrink tubing to keep water out. Heat-shrink solder-splice connectors can work, but because they shorten the length of the wire, you’re likely to need to splice in a few extra inches of wire, meaning that you’re making not one but two splice connections on each wire.
When I’ve encountered this situation, I tend to splice in a few extra inches of wire, manually solder each end, and cover the solder joints with heat-shrink tubing. Despite writing an electrical systems book, I don’t do this kind of work often, so you’re welcome to laugh at my soldering skills, but here’s how I do it.
- If you’re splicing in extra wire, identify the gauge (thickness) of the wires you’re repairing, and make sure to use wire of at least the same gauge. In my case, I found that two of the ground wires were actually of a thicker gauge than the rest.
- Cut the requisite number of splice wires all to the same length and strip their ends. It’s up to you whether you use different colors of wire or not.
- Strip one end of the wire being repaired and slide a piece of heat-shrink tubing over it and several inches past it.
- Bend a right-angle hook in the ends of the broken wire and the splice wire, put them together, fold over both hooks, and smooth it down to as small a diameter as possible.
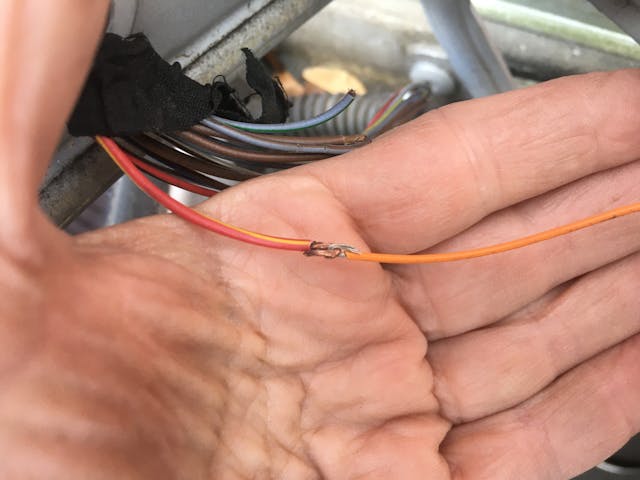
- Heat the little bundle of wire with a soldering iron and touch the solder to the wire until it flows into the strands. As with any soldering, you don’t want to “cold-solder” it so the solder sits on top instead of flowing in.
- Note that, in the case of old wiring with a coating of oxidation or corrosion on it, it may be necessary to use flux on the wires in order to get the solder to melt and flow.
- Note that some people like to “tin” the ends of the wire first with solder, then twist them together, then flow solder into them.
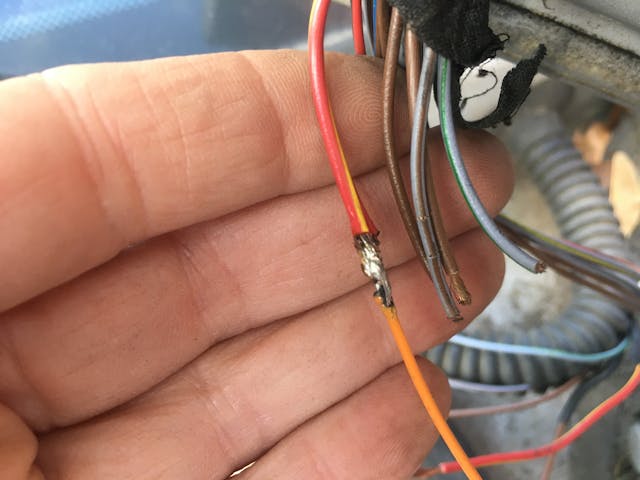
- Once the splice has been soldered and has cooled, slide the heat-shrink tubing down over it, and use a heat gun to shrink it in place.
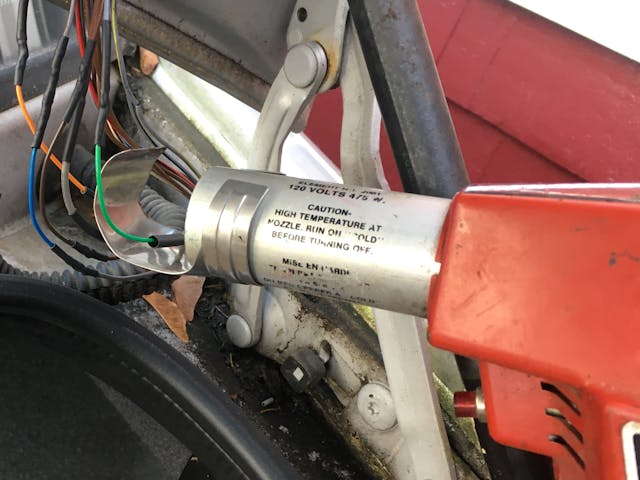
- Repeat for the other end of the wire, then for any other broken wires.
***
I don’t do work like this often, so I proceeded slowly and broke the work into two sessions. I also ignored advice on BMW forums to cut and splice all the wires (meaning including the ones that aren’t broken) to keep them all the same length. The solder melted easily on the new spliced-in sections, but not on the 20-year-old stripped-off wire ends that I was trying to reattach. Using flux and having it carry the solder into the joints was essential to making good soldered connections.
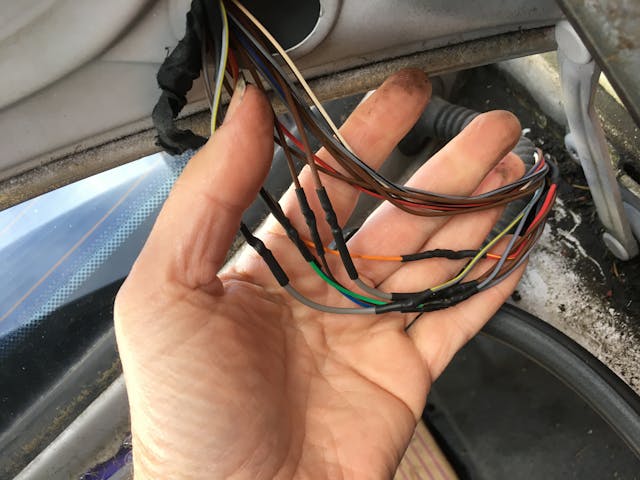
With the wire splicing complete, I gently closed the trunk and curled my hand under the lid to trigger the rubber-padded release button.
Pop!
I then did the same from inside the car.
Pop!
And yes, the trunk light went on.
Lastly, I stuffed the wires back inside the now-slit rubber sheath, wrapped it in the stick-to-itself cloth tape that wraps old BMW wiring harnesses, and fit the sheath back in place. I still need to seal up the still-slit rubber boot with some adhesive or tape.
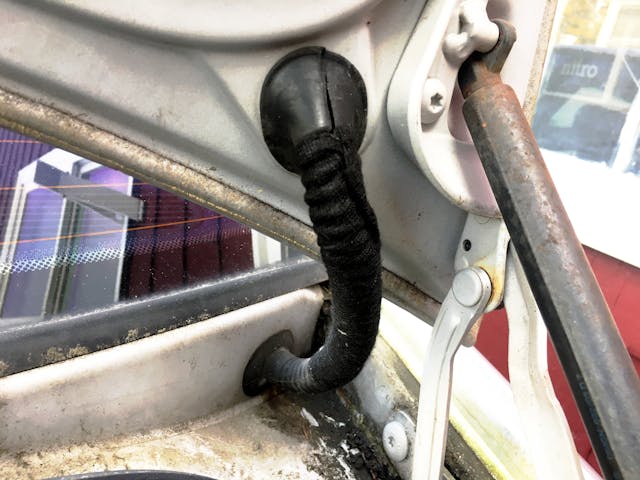
The next time I drove the car, I got the cherry on the sundae of the repair—when I started the car, for the first time in the eight years I’ve owned it, the “trunk open” message didn’t appear.
So it wasn’t the “quick hit-and-run” repair I’d envisioned, but it was still extremely satisfying. The wiring repair cost me two additional repair sessions, but no money.
And yes, I’m as curious as you are if that actuator I replaced was, um, actually bad. Hey, 42 bucks is 42 bucks.
***
Rob’s latest book, The Best Of The Hack Mechanic™: 35 years of hacks, kluges, and assorted automotive mayhem is available on Amazon here. His other seven books are available here on Amazon, or you can order personally-inscribed copies from Rob’s website, www.robsiegel.com.
Check out the Hagerty Media homepage so you don’t miss a single story, or better yet, bookmark it. To get our best stories delivered right to your inbox, subscribe to our newsletters.
Good work Rob! I’m a wiring fanatic and was hoping you would reject the crimp splicer and the pseudo-solder butt connector. Your handiwork left nothing to desire. Nice touch with the pro heat gun and deflector shield. Soldering is always the best way to connect or repair automotive wiring. Degreasing the wire before soldering may have helped as some wire insulation builds up an oily residue inside on the copper wire. And yes, a little rosin flux or tinning rosin flux can go a long way to making the job easier and faster.
Oh the time it takes to find and repair electrical gremlins. Let’s step back a bit to a Cadillac sedan de ville cera 1979. Illuminated entry would not shut off, draining the battery from day one. Towed in, where do you start? I soon learned there are junction blocks distributing power throughout this vehicle. I could isolate different parts of the car. Moving forward literally I , creeped removing trim as I went, the problem was not beyond the B pillar ( rear jam of the front doors). When I removed the A-pillar trim the lights went out! When I reinstalled the A-pillar trim the lights came back on ! A revelation! Upon closer inspection, the wiring harness was sitting on top of a welding nub (remains of mig weld wire) that would puncture the harness when the trim was installed. There is no other way to find these problems then having to dig deep, which means time and expense.
Dennis, the illuminated entry on 70’s Cadillacs is a common problem after 50 years. There is a controller/relay behind the kick panel next to the emergency brake that is exposed to moisture. It is true when it fails the lights do not go out when you get out of the car if the Illuminated entry has been engaged. On several of my cars, when I got out of the car I would have to open the front passenger door and close it to get the lights to go out. You can by pass the relay behind the kick panel and it will defeat the illuminated entry and you will not have the problem of the lights staying on and running down the battery. Just something to check.
Did you cut and splice the wires that were not broken but had insulation damage around the copper, or did you wrap these with tape and job done?
If there was cracked insulation on a wire that I was already splicing, and it looked like there wasn’t any breakage of the stranded wire, I slid a piece of heat-shrink tubing over the cut end and shrunk it in place. If I didn’t already have a path to slide heat-shrink tubing or there was visible stranded wire breakage, then I cut it and re-soldered it.
1990 Buick Reatta convertible had many electrical problems. Door locks, interior lighting, and the top cover latch not working . Turns out the wiring running under carpet tended to hold water and short out. After removing seats and carpet, finding the bad wires resoldering everything came to life. It was around a 10 hour job but so satisfying to see the results well worth the time and cost was below 20.00
I need to do this job on my E34 Touring. Since I have the car registered as an antique, there is no inspection, but I would prefer the reverse lights, CHMSL and rear wiper to work if nothing else.
For sealing up the rubber wire boot, consider using silicone tape. It bonds to itself and is very waterproof once it’s sealed. I’ve nearly attempted to use it to “temporarily” seal a cracked tie rod boot.
The best part is that it doesn’t eventually dry out or turn into a sticky mess like most electrical tapes out there.