Eight Fresh Seats and Nowhere to Sit
I’ve been measuring the progress of the rebuilds for the pair of Honda XR250R engines on my home workbench in fractions of an inch. It may sound like the whole situation is going nowhere fast, but the project is going quite quickly: After fitting and sizing new valve guides into the cleaned and prepared cylinder heads, it’s time to take a seat—or eight.
For me, the cylinder head of the Honda XR250R is the gift that keeps on giving. Back in 2020 I brought home an absolute piece of junk that immediately dropped a valve and made a paperweight of the piston. Back then my goal was simply to have a running motorcycle, so the engine got a new piston, along with a a new valve and some fresh gaskets. I didn’t know what I didn’t know, so I shoved that new valve into place and crossed my fingers that the engine would work properly. Somehow, it did.
The further I get from that project, the clearer it becomes that the engine ran again because of pure luck.

The two engines on my bench now are a far cry from that project. Four years on, I understand the importance of the smallest aspects of an engine and know the risks that come with throwing an engine together with half used parts, half new parts, and zero real preparation. This pair of cylinder heads has taught me to do things the right way, to understand not only what I am doing but the proper way to do it, and which tools to use along the way. With a fresh set of valves sitting on the workbench, my most recent job was to mate each set of four valves to their seats: four ring-shaped surfaces in the hardened metal of each cylinder head.
The second stroke in the four-stroke cycle is often underappreciated. So much of the power potential in an engine comes from compressing the fuel and air mixture before burning it. Leaky valves bleed off that compression, and leaks are often due to bad valve seats. When functioning properly, seats help limit wear and tear on the valves, which open and close thousands of times per minute.
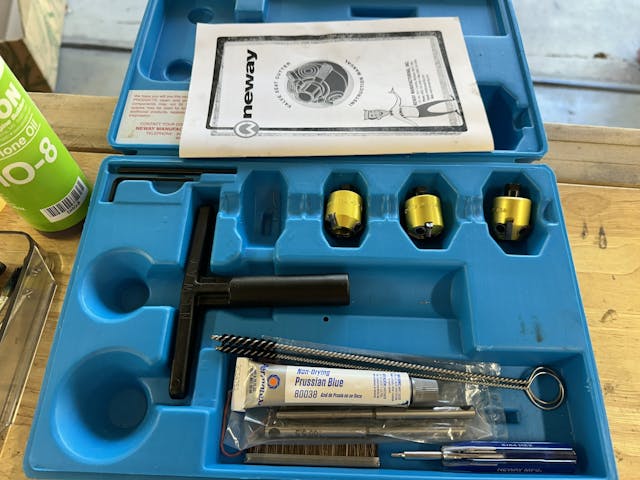


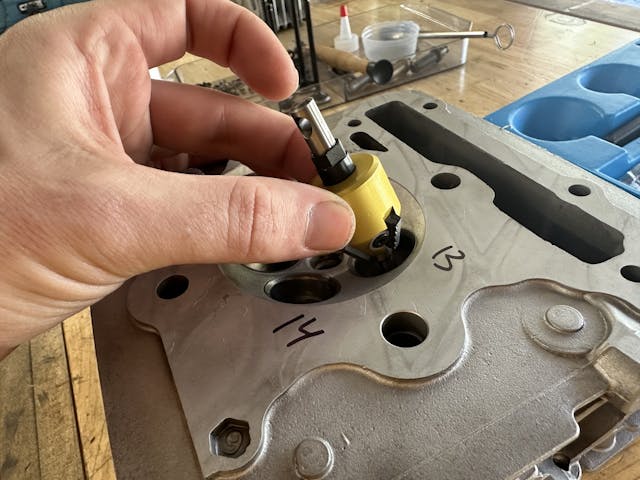
The tools for cutting valve seats can be relatively affordable all the way to wallet-draining. I elected to go on the more affordable end of the price spectrum and picked up a kit from Neway Manufacturing. After trying it out by refreshing a very poorly running engine, I was impressed with how simple the three cutters made the process of cutting the perfect valve seat: Install the pilot into the valve guide with a light twist, dab a bit of oil onto the pilot to reduce friction, slide on the first cutter, use the T-handle to rotate the cutter clockwise just a few turns, slide the cutter off and check the work.
I quickly developed a feel for how much material was removed by each clockwise rotation of the adjustable carbide cutters. Setup took seconds, then it was two quick passes with the 60-degree and 30-degree angle cutters to establish the rough geometry before sliding the 45-degree tool in place and dialing in the surface against which the face of the valve would actually sit.
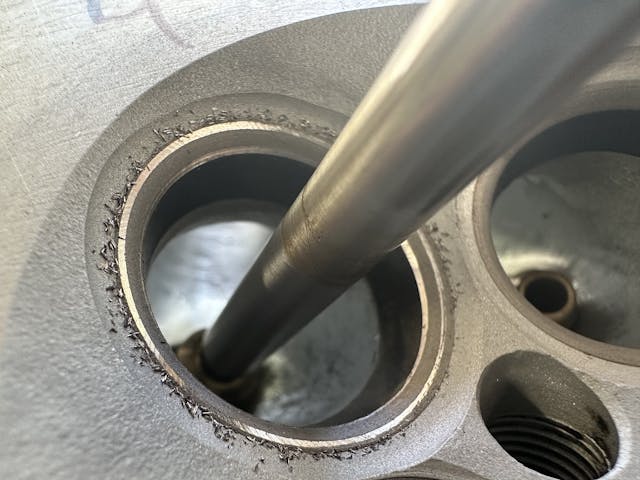

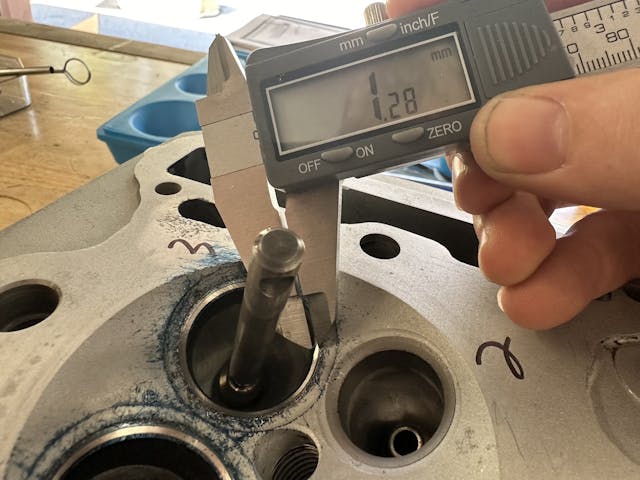
A three-angle valve job is more or less the bare minimum for valve seats these days. A machinist would have happily lightened my wallet and added two more angles, and the additional cuts would help airflow, but a five-angle valve job is overkill for the agricultural nature of the Honda XR engines. I was able to do a three-angle job at home, and the performance of these engines will likely be very close.
After marking the seats with Prussian blue and checking the width of the 45-degree seat after the final cut, everything got cleaned before I re-blued and lightly lapped the valves against the fresh seats to check the contact on the valve faces. Once everything fit perfectly, the only thing left was the final cleaning and preparation for installing the assembled cylinder heads on the engines.

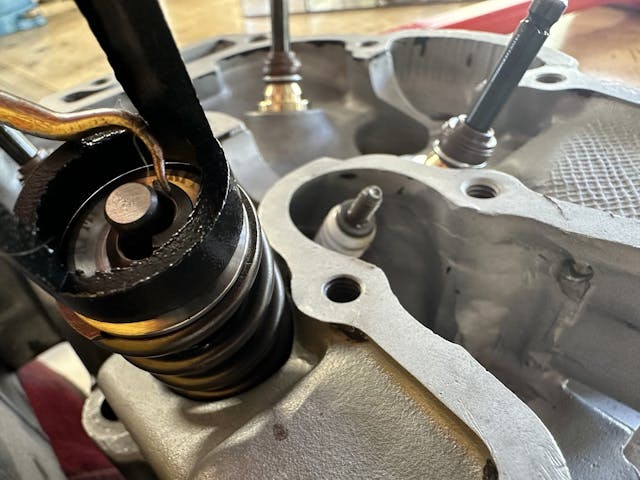
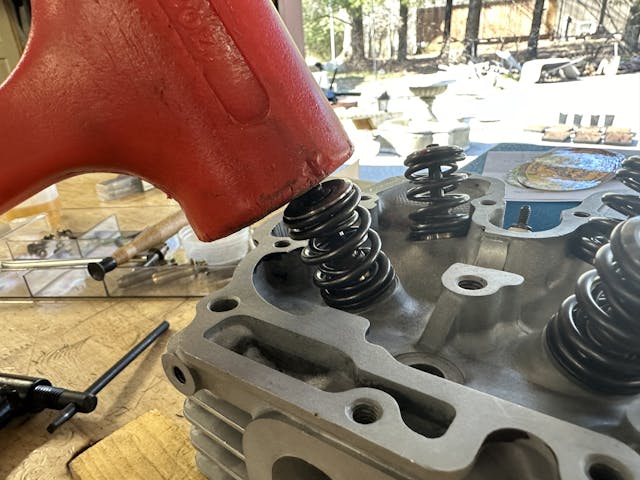

This marks the end of an adventure that was at times a nightmare but in the end was so rewarding. Every step of the top end of these engines was done right, by my own hands, in my own shop: Disassembly, parts selection and replacement, fitment, assembly, and soon break-in. Just four years after stumbling through a rebuild hoping the engine would run at the end of it, I am now staring at the possibility of two rebuilt engines that are stronger than they were before I worked on them and that, because of that work, will last longer than I can probably imagine. The contrast makes me laugh at who I was then, and that person would likely laugh at me now, panicking over a fraction of a millimeter of additional valve seat width. Neither is more correct than the other: We were both just having fun making broken engines work again. Neither completely right nor completely wrong, just happy to be fixing things.
***
Check out the Hagerty Media homepage so you don’t miss a single story, or better yet, bookmark it. To get our best stories delivered right to your inbox, subscribe to our newsletters.
“Eight Fresh Seats and Nowhere to Sit” – somehow I sense that this line has been saved in the back of your brain’s pun-files for quite some time, just waiting for this installment.
At-any-rate, this series has been informative and encouraging (encouraging others to try their hand at doing what most of us normally would pay a shop to do, I hope). I like how you compared the old you and today’s you and how you realize that both of you fit into what you were doing at the time.
He’s been drilling for puns for awhile. Now that he has cut his teeth on this one hopefully he will now get some seat time. That’s it I’m outta here.
I hope the sound of groans coming from all directions made it difficult for you to nap after writing that, Gary! 🙄
Congrats on the successful venture! Between the Canadian exchange rate buying tools and the time sink, this process just confirms that I’ll gladly pay a local machine shop to refresh the head of my OM603 when the time comes.
That’s totally fair! I won’t be doing this process for all of my projects, but will certainly do it again if the situation is right. Guess that’s a good thing considering I bought the tools! haha
I have sung Neway’s praises here in the past. If you ever find the kit you need on the used market snap it up, you’re not likely to get another chance.
I was amazed that I hadn’t heard of them before this year. When I called and chatted with the owner on the phone he was super helpful and kind. I look forward to adding a few additional cutter and pilot sizes to cover some potential future projects. Such a simple and easy to use tool.