6 tips for using jack stands
Working on cars requires a whole slew of relatively specialized tools. Often times we don’t even realize how unique those tools and practices are until we talk to someone new to the hobby. Or someone who is on the outside looking in. Just one example: How casually we discuss (and practice) the act of lifting our multi-thousand pound vehicles into the air and then supporting them with separate load-bearing apparatuses that allow us to work on, disassemble, or reach under the vehicles. It’s dangerous when done right, and deadly when done wrong.
That sounds scary, and to a point it should be. Being cautious when the risks are this high is not a bad thing. That’s why we created a quick list of tips for using jack stands: good for newbies, but it’s also a refresher for those experienced enough to have lifted up a vehicle many times, in many ways over the years.
Buy once, cry never
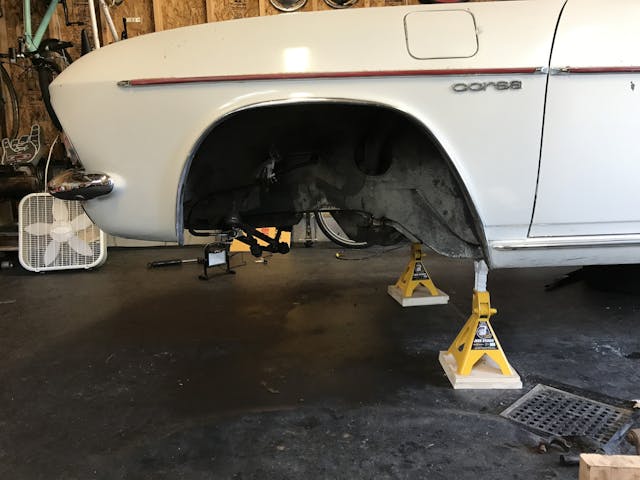
There are many factors in selecting jack stands, and price is one that many of us are forced to consider. While tools can and will be shopped based on price point, jack stands should not be one of them. These are critical safety items that should come from reputable and trustworthy sources. The Harbor Freight jack stand debacle of 2020 should be burned in our collective memory for a long time, as being crushed by your car is not the way to go. Cheaping out with jack stands is a fast track to a mere feeling of safety, rather than possessing actual safety.
Jack stands should be sturdy with a good wide base. A secondary method of locking them at the desired height is also a plus. Do not modify jack stands or otherwise compromise safety features in the name of convenience. Doing so is only making it easier to get hurt.
Size appropriately
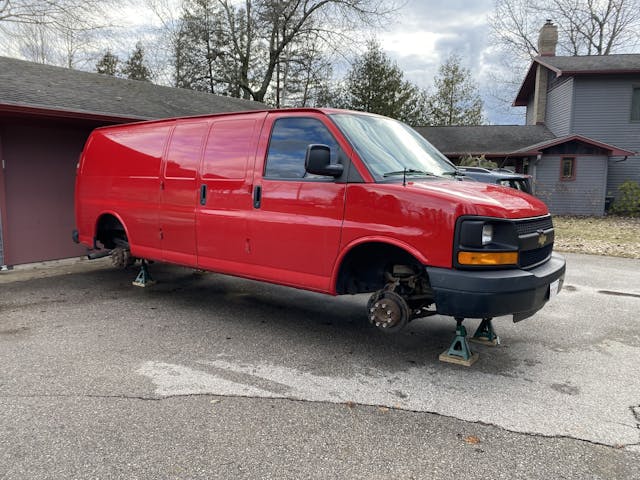
Jack stands produced after 2015 are rated as a pair. Which means if you find some at the local parts store that say they are “three-ton” jack stands, the ability to support the claimed 6000 pounds requires both stands. In reality, three-ton jack stands should be the smallest used in most home shops, as it gives a good safety margin when working on smaller cars, yet a set of four does have enough capability to hold a medium-sized truck or SUV in a pinch.
Remember that storing jack stands can be a hassle, so having one set that covers anything you’ll work on is the best way to go. That said, a small and large set of them is a nice luxury if you have the space. Inevitably something gets “stranded” on your one set of stands…and you’ll need another set shortly thereafter.
Trace the load path

Jack stand placement is as critical (if not more critical!) than proper sizing. The biggest jack stand in the world is useless if you place it in the wrong spot, letting the car fall down anyway. The service manual is the best place to look for jack points and jack stand placements. Even the owner’s manual in the glove box, a book that’s been shrinking over time and loaded with “please see dealer” language, likely still outlines the jack points for safe lifting. A quick internet search will likely reveal appropriate information too.
But sometimes that doesn’t work, or what you are doing is something the original engineer from decades past could have never imagined. That’s when a little bit of critical thinking goes a long way. Look under the car and locate a place that looks sturdy enough to place a jack stand, then follow what that is connected to. From there, imagine how it would support the load being placed on it. Supporting the rear of a car by placing stands under the rear differential makes sense because the entire weight of the car is normally supported by that part. Using a bumper or frame brace that doesn’t support and wasn’t designed for that load is a bad place to put a stand. If unsure, consult professionals.
Do the shake test

Now that your project is up in the air and supported by jack stands, there is one last step before you roll underneath: You gotta shake it. No, not the latest TikTok dance. Shake the car. Go to one of the corners and give it a good push and pull to make sure the car is stable and the stands are not going to move or shift while you are underneath. This is the same thing that mechanics in shops do when putting a car on a two post lift.
After all, now is the time to find that the ground isn’t really flat or the stands aren’t fully seated on their safety catch. Only after a good shake can you roll under the car with confidence that it will not be coming down on top of you.
Buddy system
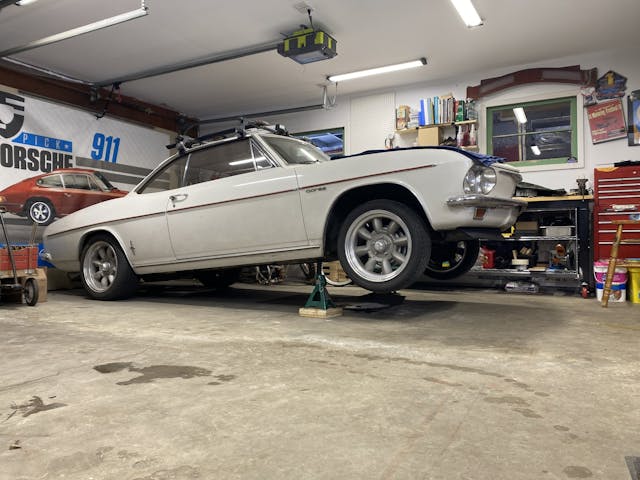
It feels strange to do when performing an innocuous task like adjusting a transmission shift cable or removing a driveshaft, but telling someone that you are working underneath a car with jack stands is a good practice. A text or call to a friend just to say “hey, I’m working on my project and am under the car for a bit” is enough of a heads up: if they don’t hear from you in awhile they know to check on your well being. Being pinned or injured under a car with no means to get help should be horrifying to you, and encourage you to whatever is necessary to prevent it.
Keeping a phone on your person is one option, as is using smart speakers or other items that require nothing more than yelling at them to activate them. I personally have a Google Home Mini above my workbench, which allows me to broadcast a message to another speaker inside my house by just yelling at it. This lets me feel safe-ish when I am working on projects while my wife is inside. (Presumably enjoying her time without me.) This practice isn’t for everyone, but it works for me. Find a system that works for you and use it.
Cribbing away that sinking feeling
Motorcyclists are familiar with the peril of asphalt: Ride somewhere on a warm day, set the bike on the kickstand, stop for a coffee, and the bike is laying on its side by the time you get back. Vandals? Inattentive drivers parking too-big SUVs? Nope. The asphalt did that.
Asphalt comes in a variety of flavors and mixtures, some of which isn’t nearly as solid as it feels under your feet. A heavy load concentrated on a small point can sink into asphalt. And the weight of that motorcycle leaning on the kickstand’s relatively small area can punch a hole into asphalt. Lo and behold, the kickstand sinks down enough that the motorcycle tilts and falls over. Bad news, but it points to a bigger problem.
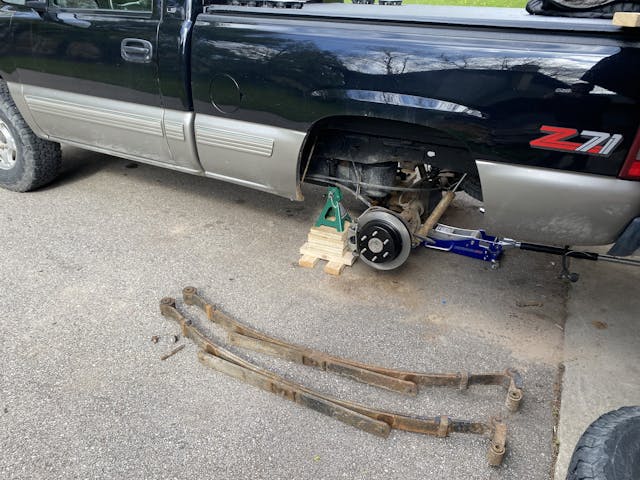
Now picture this kickstand is actually a jack stand under your project. With no warning, the car can shift as the asphalt gives way. Prevent this by using something like a chunk of wood to spread the load of the jack stand to a larger area. The same applies for any soft substrate like gravel or dirt. Cribbing is a common thing in heavy equipment transport/service, and by extension is a smart exercise to do when working on light duty vehicles as well.
Have another safety tip to add to the list? We’d love to hear it, as you can’t be too safe in these situations. So leave a comment below for everyone’s safety and well being.
***
Check out the Hagerty Media homepage so you don’t miss a single story, or better yet, bookmark it. To get our best stories delivered right to your inbox, subscribe to our newsletters.
I have a light duty set and a heavier duty set, but for the most part I use cinder blocks and wood. The one fatal flaw with jack stands is that they tip. Even if things are right when you first set them up, wrenching on cars can cause things to move around, then the next thing you know, one of your stands is sitting kind of wonky. Cinder blocks and wood give you a lot more contact surface with the ground and with the vehicle and are generally more tolerant to vehicle movement
The issue with cinder blocks is they are often used in the incorrect orientation to support the load. I wouldn’t recommend cinder blocks. Always use the right tool for the job.
I completely agree with Superduty…I’d never use cinder blocks at all… A good set of jack stands correctly placed (sometimes I’ll even place a second pair of jackstands) and a floor jack left in place just in case is how I typically work, when it comes to lifting a vehicle that I am going to crawl/work under you can’t ever be too safe… I don’t want my wife to come to my shop and find me squished!
To be honest, I’ve never understood the use of cinder blocks in place of jack stands. Cinder blocks are much more fragile than stands, unadjustable for size, often heavier, and more difficult to move and place. Add in the chance they just fracture and fail because they are being used outside of their design parameters and… what’s the positive to this again? Price? Doesn’t seem worth it when a decent pair of 3-ton stands can be had for less than $100 and last basically forever if taken care of.
A project shifting to the point that the stands are tipping over means the car is not supported properly in the first place, not the stands fault.
Stability… seriously. You put them in the correct orientation and top them with a piece (or 2 or 3) of 2×6. You cannot shove that car off of those blocks if you try. I guarantee I can rock your car off of a set of jack stands no matter how well you set them
Now if I am doing brakes or something quick I will get the stands out (or use my neighbor’s lift). The blocks generally come out for longer term projects
I’m with you. I’ve never trusted jackatands if I have to push on pull on a ratchet trying to break a bolt loose. I’ll take the block and wood any day. You are also correct about saying you could easily push a car off jack stands.
Utilizing semi-solid cinder blocks is structurally better.
In the masonry business we jacked up a forklift with tractor tires utizing regular 12 inch cinder blocks to change out one of the wheels, took the wheel off, went to a tire shop, when we returned the cinder block had failed under the weight. Even with a board on top of it. So I would strongly suggest using a semi solid cinder block
The positive comments re. cinder blocks are what is called “survivor bias”. All the unfortunate mechanics who died or have lost limbs and aren’t working on cars any more are not on this forum. Be like Kyle. Be alive to enjoy your hobby car.
CINDER BLOCKS!??? NO! NO! NO! This coming from a Hot Rod builder with 45 years experience, but also a Firefighter/Paramedic of 30 years’ experience who has had to remove a victim of failed cinder blocks used instead of jack stands.
One thing I found is that when are putting both ends up. You have to be careful to raise the vehicle incrementally on each end. Putting one end up high and then bringing the other end up can cause the initial set of stands to shift causing the vehicle to fall. My brother is a Crane operations superintendent and he says never lift heavy weight at large angles.
I once put a car on cinderblocks while I was having lunch the cinderblocks disintegrated and the car crashed to the ground. Do not use cinderblocks they are not designed to support a load.
They hold up the second story of my house
Cinder blocks were designed for home construction (properly used) but not for supporting cars. If the load is wrong, or they are struck in certain pints, they are prone to sudden failure. Unlike a jack stand that fails if properly used (which is rare), your family will have no recourse if you use something like a cinder black to support your car and it fails.
Concrete blocks or cinder blocks are meant to be filled with concrete to make the walls strong and stable
Your house is held up by four cinder blocks?
And they come apart in a storm.
but when building a house the cinderblocks are filled w/rebar and concrete
True cinder blocks are just that, made from the ash of burnt coal. In truth, they don’t compress but do shatter.
Today, when many folk call the block cinder block, it is actually made from poured concrete. Again, very heavy and prone to breaking at the holes. I’d sooner use 4×4 even better 6×6 timbers. I’ve seen building blocks of 8×8 timbers used to support homes that are being jacked
Timely article as just this afternoon I decided to replace my old starter with a new hi-torque mini-starter and do some rewiring while I was at it (rerouting starter wires further away from headers). In doing so, I dug out four jackstands and placed them so that one pair was supporting the frame rails and the other pair were under the A-arms just in case the car slipped or a stand gave way. Supporting the weight via suspension parts isn’t ideal, but as a secondary “catch” in case of a fall, I’d rather have the suspension catch the car than let it fall clear to the tires.
I’ve broken cinder blocks using them to support barn walls and storing farm implements up off the ground, so I don’t think I’d trust them when I was under a vehicle supported by them.
Never use blocks and even when using wood care must be needed as the right kind of wood is used.
Never go cheap and always go heavy/
If possible leave the jack in place under the vehicle. It can catch a car or at least make it easier to remove it off of you should you choose poorly the right stand.
Never have used jack stands. My first recommendation is to slip a mounted wheel and tire underneeth, I also use large wooden blocks with assortment of 1x or 2x’s and even keep floor jack propped up.
Kudos on the entire article Kyle, I thought I was going to get to add the shake test but you got that one too. I’d only add that on longer-term jobs perform the shake test again at the start of each new day.
Thanks! That’s a good tip on doing the shake test occasionally. Who knows what happens when we aren’t looking.
I would add that the shake test should be done BEFORE removing the wheels, not after. You really want to land on the tires if the shake test actually causes the car to fall off the stands.
DA
Never use cinder blocks! I did and nearly lost my legs when the blocks pulverized and, in a nano-second, the car slammed to the floor. Fortunately my legs were within the confines of the rear wheel well, otherwise I’d be reporting this from a wheelchair, or perhaps not reporting it at all!
Cinder blocks? These are the same guys that open champagne with a sword. It does the job sometimes, but there is grave risk. I always use a jackstand when opening champagne, personally.
🤣
Xactly!
Great article! When I was a teenager, long ago, a friend of my parents was working under a vehicle with just a jack. It shifted and dropped on him. Fortunately, his young son was nearby and rescued him. Ended up needing back surgery as I recall. So I’ve always been gun shy and extremely aware of using good jack stands, cribbing, etc before sticking any part of my body under a car or into a pinch point.
I think you forgot an imporant issue, car angle when lifting the car on one side only, particularly lifting the rear as the front wheels don’t have stationary breaks. Sounds obvious like most issues in the article but the easy things are the most dangerous as the attention level is low.
Good point! I always chock the wheels at the opposite end when lifting just the front or back.
Most of the time that I have issues with the jack stands going wonky, it’s the jacks fault. The wheels failed to roll properly for various reasons.
Surprised no one has commented on ramps. What are their pros and cons?
One ‘con’: I can think of: your vehicle must be mobile to drive up on them (and off again) – or you’d better be a really good pusher. With stands (and a jack), you can elevate something that is running or not. Of course, you could jack up a car and then put ramps under it, but where’s the sense in that?
Another ‘con’ that came to me when writing the above: ramps only really work with the tires on. So driving up on ramps to do a brake job or change out wheel bearings is pretty impractical.
Finally, as hard as it might be to store jackstands, ramps are at least twice that.
if your car is sporty and relatively low to the ground, there is a good chance that the lower fairing will hit the ramp on the way up. You have to be dead on when it comes to stopping or you will drive off the end of the ramp and do some serious damage in the process. one ramp may stay put while the other slides forward, putting your car in a very precarious position. Most ramps can’t accommodate tires with any width to them. You can only put one axle up on the ramps at a time. The ramp portion of the ramp tends to be right in the way of where you need to roll with a creeper…
Ramps are cumbersome, heavy, difficult to maneuver, and they always get in the way of where the creeper needs to be. I use ramps all the time. My ramps have a locking mechanism giving the car a solid platform that will not fail. If it is necessary to elevate the entire car, I use the ramps on one end (for solidity) and jack stands on the other. I use stands with an insertable pin rather than the ratchet type. I never risk having a ton of car (small British cars) fall on me – life is short as it is.
I about got killed using a pair of steel ramps on my son’s car. We wanted to change the exhaust system so the entire vehicle had to be up off the ground. He drove the front tires up on the ramp, put the transmission in park and turned the engine off. I went around to the back, pushed a floor jack under the differential and began to raise the vehicle up. The plan was to raise it up, then put a pair of jack stands under the rear axle. But guess what? As I was standing behind the vehicle pumping up the floor jack, the vehicle suddenly rolled backwards off the ramps when the rear tires came off the ground. Raising the back end of the car must have moved the front end just enough for the tires to roll back off the flat portion of the ramps. So I’m hanging on for dear life to the jack handle trying to stop a 4000 lbs. car from rolling backwards down the driveway and into the street. I finally had to dive to one side to avoid getting run over. The car continued to roll down the drive way, across the street and into a ditch on the other side of the street. Fortunately, there was no cross traffic on our normally busy street, and the car (and me) suffered no damage. We got rid of those ramps and would NOT recommend anyone using them unless the ramps have a means of locking the wheels in place to prevent the vehicle from rolling off.
I don’t use the same method for all circumstances. When I want both ends up I use a pair of ramps on the front and jack stands on the frame in the rear.In my garage the are slots in the concrete to prevent cracking. I use one of them to secure a 4×4 that prevent the ramps from moving when driving on them. I then secure a wood block behind each front wheel to the ramp with a ratchet tie down so the front wheels cannot move. Then I jack the car by lifting the axle to locate the jack stands under the frame. I have two jacks that I leave under two points with some load on them in case something fails. I feel pretty safe with this method.
Yikes. Was it a rear wheel drive car? If so once the back wheels were off the ground it would be free to roll and if the ground wasn’t perfectly level it would do exactly that.
If the car was rear wheel drive as soon as the rear wheels where coming off the ground ,it would be like putting the car in neutral. putting a rear wheel drive car in park only keep the rear wheels from turning. Just like putting the parking brake on only locks the rear wheels. Ramps are only meant to raise one end of the vehicle.
Actually, I have used a floor jack to lift the vehicle high enough to place my ramps under the front wheels.
That being said, I don’t like driving up the ramps due to the risk of driving over them (too far) and I don’t think it is the best thing for the integrity of the ramps.
have found using the proper size jack stands ON a set of metal ramps allows for needed clearance when working on a rear end.sturdy & no issues.
Another concept conspicuous by its absence is PRIOR to EVERY use of a jack stand one should INSPECT each stand for damage such as cracks, elongation or deformation of metal features, bending of ANY kind, etc. Rust never sleeps nor does metal fatigue. The 5 minutes you take to inspect this type of tool could save your life
One other point not really covered.
#1 Make sure if using the Frame to put the stand under it is in fit condition. I have seen frames collapse on older Chryslers in the rust belt.
#2 on todays vehicles know the jacking points and where you can support the car. People will put a jack stand in a poor spot or one that is not suited for the weight and damage a car. I have seen bent control arms and dented floors on many of todays unibody cars.
You mentioned putting the stands under the differential. I think you meant the axle as the differential is not normally a load supporting device.
Looking at the photos with the article (above), I winced at the Corvair with the front wheels on stands, however NO chocking of the rear wheels! Even ‘IF’ the car’s emergency brake was applied in that situation, I wouldn’t go ANYWHERE under that car, without chock blocks at the rear wheels – in BOTH directions..
I rarely use jack stands, but one thing I always do even when doing any kind of work with wheels off is slide the removed wheels/tires under the car. This can act as a secondary safety device so that even if the car drops while you are under it, the car will not go all the way to the ground. May be the difference between a broken rib and crushed skull.
I was just going to say that! I always shove the removed wheel under the car for a secondary catch. If the car is falling, I don’t care if the wheel is in a bad location, as long as the car is still off of me!