Hemi: How Chrysler drew a dome and forged a dynasty
Hemi is the Greek word for half. That makes a hemisphere exactly half of a perfectly round bubble. Unfortunately, the engineers who created Chrysler’s 1951 FirePower V-8 didn’t need that much bubble. In lieu of a full hemisphere, they capped each cylinder with a spherical shape whose height is significantly less than half its diameter. Prompted to explain what they had wrought, the Chrysler motor maestros must have been at a loss for words. While the shape depicted on their blueprints is best described as a spherical cap or dome, those terms lack cachet. Instead, the engineers chose the more evocative Hemi name, even though it’s not strictly correct.
DeSoto tried harder by labeling its version of this V-8 FireDome. According to Chrysler Corp. veterans we contacted, no sleep was lost worrying about the legitimacy of the Hemi name. Over the decades, these V-8s were such potent weapons in the horsepower wars that the company trademarked its vaunted nickname for the third-generation version, which arrived in 2003. Two decades later (and with no hint of a hemisphere remaining in any Chrysler engine), the Hemi thrives as one of the most beloved V-8s money can buy.
Imagine being a fly on the wall at GM headquarters in 1951 when news of Chrysler’s FirePower V-8 arrived. In many respects, this newcomer copied the Cadillac V-8 born two years earlier; the bore, stroke, and compression-ratio specs were an exact match. Yet, somehow, GM’s crosstown rival managed to squeeze 20 more horsepower, or 180, out of its 331-cubic-inch V-8.
The boardroom erupted, engineers were dispatched to their labs, and dynos howled in an earnest attempt to raise output at any cost. Motown’s horsepower war was on. The following year, Cadillac added a four-barrel carburetor to retaliate with 190 horsepower, topping Chrysler’s 180. By 1958, Chrysler had upped the ante all the way to an impressive 390 horsepower with more displacement, higher compression, larger valves, and electronic fuel injection. By then, every Detroit brand had crashed the horsepower party.
Turns out Chrysler was wielding a not-so-secret weapon in the form of a more efficient combustion chamber design. While every carmaker had modernized its engines with shorter piston strokes to boost rpm, and more compression to exploit the high-octane gasoline developed during World War II, Chrysler dusted off a technology invented at the dawn of the 20th century to build the truly better mousetrap. What Chrysler had in 1951 that competitors lacked were hemispherical combustion chambers.
During WWII, the U.S. Army Air Forces hired Chrysler to design and develop a 2220-cubic-inch, 2500-hp V-16 for use in the forthcoming P-47 Thunderbolt fighter. Like nearly every aircraft engine of the era, Chrysler’s XI-2220 featured hemispherical combustion chambers with boost provided by both a turbocharger and a supercharger. Though development wasn’t finished by war’s end (especially after it became clear that jet engines would soon replace piston power), one test flight to 20,000 feet did top 380 mph. Calculations projected that 414 mph might be achievable at 30,000 feet.
Knowledge gained from this program was instrumental in Chrysler’s use of hemispherical combustion chambers in its 1951 FirePower V-8, which was offered in a range of cars starting with the 1951 Chrysler New Yorker, identifiable by its large “V” on the hood and trunk. Barely a year later, Briggs Cunningham bolted the new Hemi (as the FirePower came to be known) into his C4R sports car because it was the most powerful domestic V-8 then available and earned a fourth-place finish at the 24 Hours of Le Mans.
Topping each cylinder with a machined dome instead of the wedge shapes used by GM and others expedited the flow of fuel and air into the combustion chamber and the exit of burned gas out of each cylinder. Engineers use the term “volumetric efficiency” to gauge this flow. Pumping 300 cubic inches of fuel-air mix into a 300-cubic-inch engine in one complete cycle constitutes 100 percent volumetric efficiency. Most engines pump less. Adding a turbo- or supercharger to overfill the cylinders is the easiest way to achieve significantly more than 100 percent volumetric efficiency, but at the price of weight, cost, and complexity.
Of all the possible combustion chamber shapes, from wedge to flat to pent-roof, a hemi provides the minimum surface area relative to the total volume of the chamber. This is a good thing in engineering because less surface area means more of the fuel’s heat energy stays in the cylinder, where it presses down on the piston to maximize the torque produced. Heat transferred out of the combustion chamber to the cooling system is simply dumped to the atmosphere by the radiator.

Using hemi chambers enabled Chrysler to arrange intake and exhaust valves in a pattern distinctly different from the contemporary Cadillac and Oldsmobile V-8s. In the GM engines, all the intake and exhaust valves stood next to each other in a line, like a rank of soldiers at attention. Chrysler instead rotated each pair of valves 90 degrees, so that the intake and exhaust valves now were opposite of each other above the cylinder. Also, both of the valves were canted at angles to align better with their ports. The resulting fluid flow was less restricted by tight corners, significantly increasing volumetric efficiency.
The third advantage of the dome shape is that it allows positioning the spark plug closer to the geometric center of the combustion chamber to minimize flame travel during ignition.

Of course, there are always a few downsides. The Chrysler V-8’s cylinder head width and weight were significantly greater than those of the Cadillac and Oldsmobile V-8s. Also, centering the spark plugs in the combustion chambers required long tubes through the valve covers, which created sealing challenges. Operating valves that were splayed 58.5 degrees apart were another challenge; instead of the single long shaft supporting eight rocker arms that GM used, Chrysler V-8s required two such shafts per head. In addition, the long pushrods and rocker arms needed to open exhaust valves positioned far from the camshaft added weight to the valve-train that hampered high-rpm operation. To address these issues, Chrysler introduced lighter, simpler, and lower-cost V-8s for several 1955 models with what engineers dubbed “polyspherical” combustion chambers.
That same year, Chrysler commenced a four-year run of 300 “letter” cars powered by Hemi V-8s with two four-barrel carburetors and 300 or more horsepower—what some historians consider the first true muscle car.

Marine magnate Carl Kiekhaefer built NASCAR’s first truly professional stock car team around an armada of C300 super coupes. His star driver, Tim Flock, won 18 races and the championship in 1955, followed by Buck Baker with 14 wins and season laurels in ’56. In only its second year, this team scored an amazing 16 straight wins. The clever Kiekhaefer also invented dry-paper air filters for his race engine, which remain in use today. In 1956, drag racer Don Garlits bolted a Hemi he found in a salvage yard into his slingshot dragster.
Chrysler supplied only advice and spare parts because Kiekhaefer had deep pockets and sponsorship from his lucrative outboard-motor business, which became Mercury Marine. But early in the third season of Kiekhaefer’s campaign, GM president Harlow Curtice waved a red flag. At a 1957 meeting of the Automobile Manufacturers Association, Curtice urged Detroit execs to cease their direct motorsports participation out of fear that the federal government might step in with regulations that would make their lives miserable. Whether this was a clever ploy on his part or a truly valid concern isn’t clear, but by June of that year, every car company had signed on to the AMA ban.
Satisfied with its achievements on and off the track, Chrysler sent its first-generation Hemis to the retirement home after the 1958 model year. Their 361-426-cubic-inch replacements all had wedge-shaped combustion chambers similar to GM’s designs. But, like distant thunder, the racing rumble never subsided.
Gen II: Race and Street Hemis
Instead of overt racing participation, Chevy and Pontiac soon created low-profile ways to grab checkered flags while Chrysler and Ford watched and waited. After five years of suffering, Chrysler had a belly full of defeat. As the company’s chief engine engineer, Willem Weertman, noted in a technical paper, “In December 1962, engineering staff was requested to develop an engine and vehicle combination capable of winning stock car competitive closed-circuit track events. In addition, a version of this engine was desired for use in timed vehicle acceleration drag events.”
With only 15 months between the above memo and NASCAR’s 1964 Daytona 500 race, Chrysler engineers had no time to dither. The decision was quickly made to retain the existing Chrysler 426 V-8 block. To better support the crankshaft, the block’s side skirts were extended 3 inches and cross-bolted main bearings were added. When cracks appeared in the cylinder walls, their material thickness was increased to 0.30 inches.
The new Hemi head designs—first cast iron, then aluminum—developed from the previous lessons learned. Like Gen I, the Gen II design lacked a truly hemispherical combustion chamber. Weertman listed a dome diameter of 4.84 inches with a center depth of 1.34 inches. However, were it a true hemisphere, the depth would have equaled the dome’s radius, or 2.42 inches.
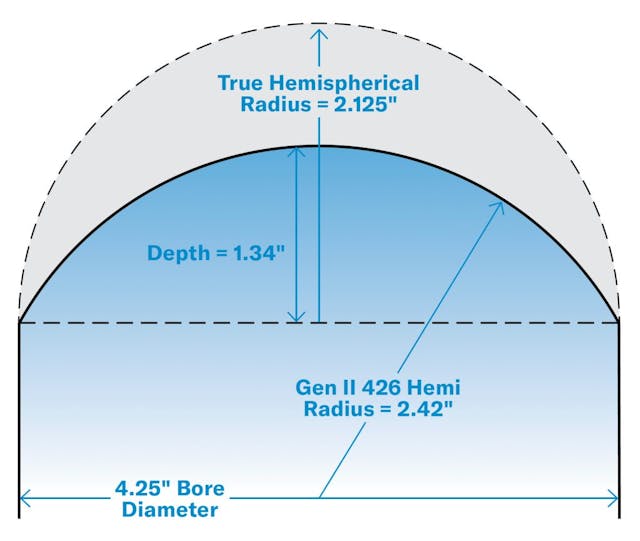
The previous 58.5-degree angle between each intake and exhaust valve was retained, and volumetric efficiency was improved by straightening the intake ports. They were as large as possible—a full 3 square inches in cross-section—while a cross-section of the exhaust ports had an area of 2.24 square inches. Spark plugs were spotted as close as possible to each combustion chamber’s center.
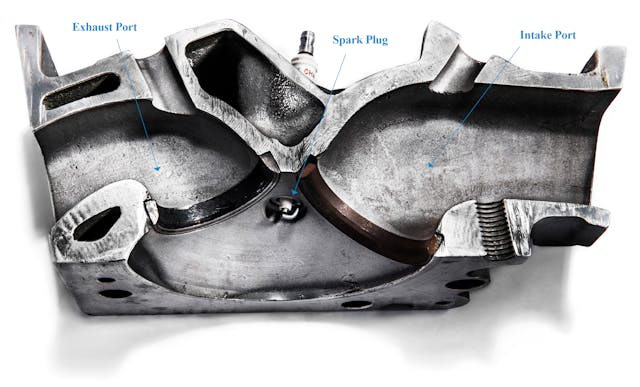
A creative measure used to improve head retention with five instead of the previous four fasteners per cylinder necessitated screwing a stud into the floor of every intake port. That stud extended down through the block’s deck into its center valley, where a nut was added and tightened.

To comply with rules, a 426-cubic-inch displacement (with a 4.25-inch bore and 3.75-inch stroke) was selected along with single four-barrel induction for NASCAR events and two four-barrels for drag-racing. Experimental engines were running by December 1963, and plans were laid to produce a few hundred of the new Hemis for the 1964 and ’65 racing seasons.
Weertman recalled witnessing the new engine’s trial by fire at Daytona: “I was one of the few Chrysler people present aware of a disastrous failure that occurred during durability testing.” Likely the failure was the previously mentioned cylinder-wall cracking. Unfortunately, the engineers lacked the time to prove that the fix was totally effective, “so it was a huge relief when three Mopars finished the 500-mile race one, two, and three.” Richard Petty won with an engine block that had been cast only 13 days before the race, Weertman said.
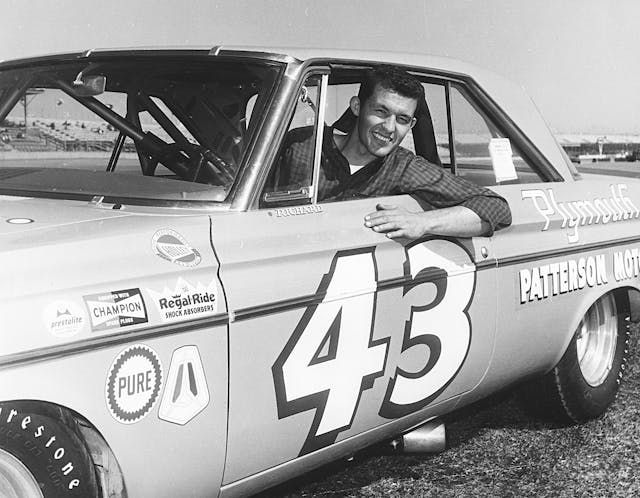
Naturally, the race engines were loaded with premium materials. The rocker arms and crankshaft were steel forgings, the cranks heat-treated and shot-peened. After machining, a dip in a nitride solution hardened the working surfaces. Finally, the crank journals were hand-lapped. Camshafts were made of heat-treated cast iron and the aluminum pistons were impact-extruded.
The twin-rocker-shaft valvetrain actuated 2.25-inch-diameter intake valves and 1.94-inch exhaust valves. A special fixture that spun that hardware to 8000 rpm used a stroboscope to freeze motion so that natural frequencies, vibration, and surge characteristics could be studied.
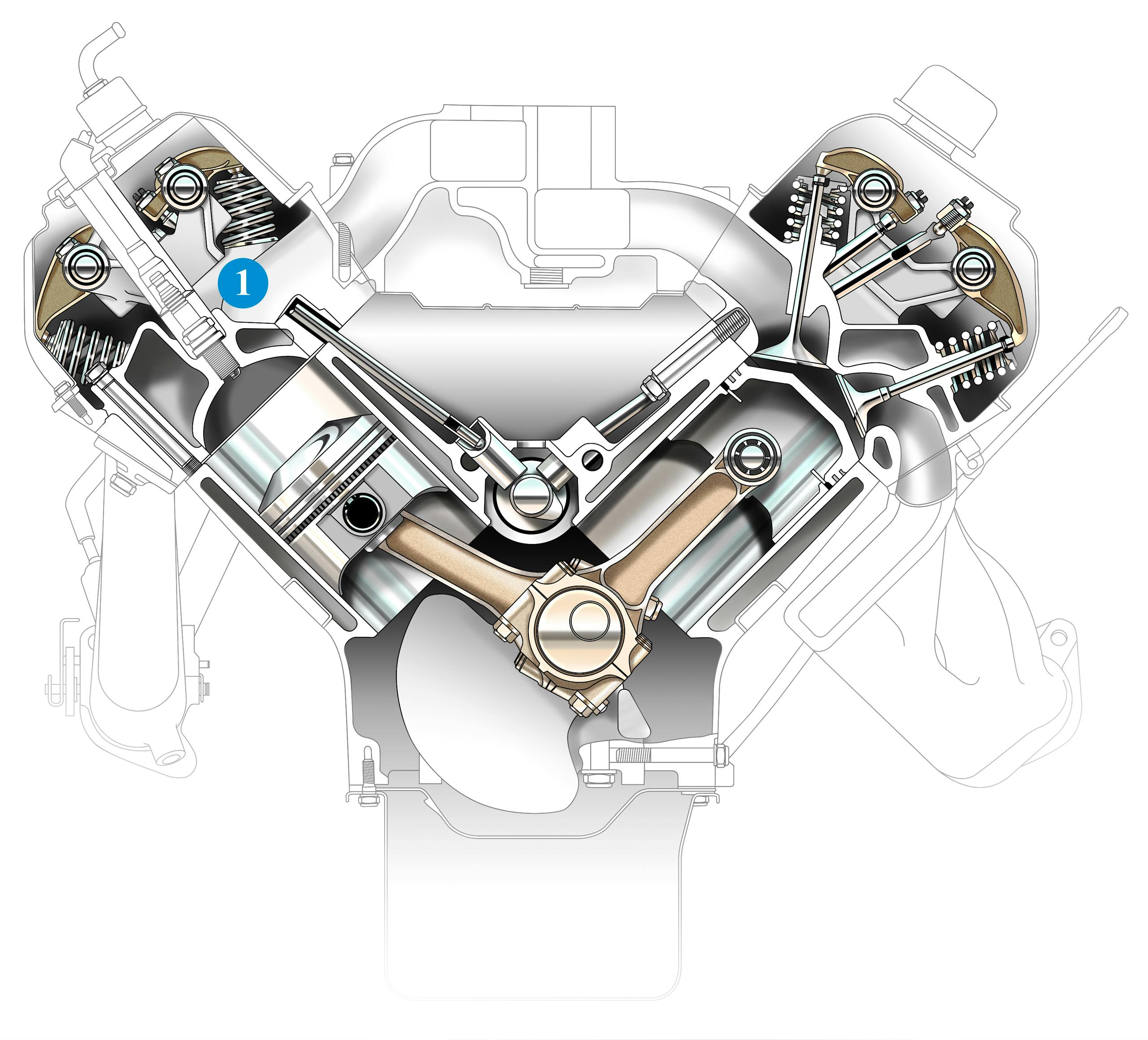
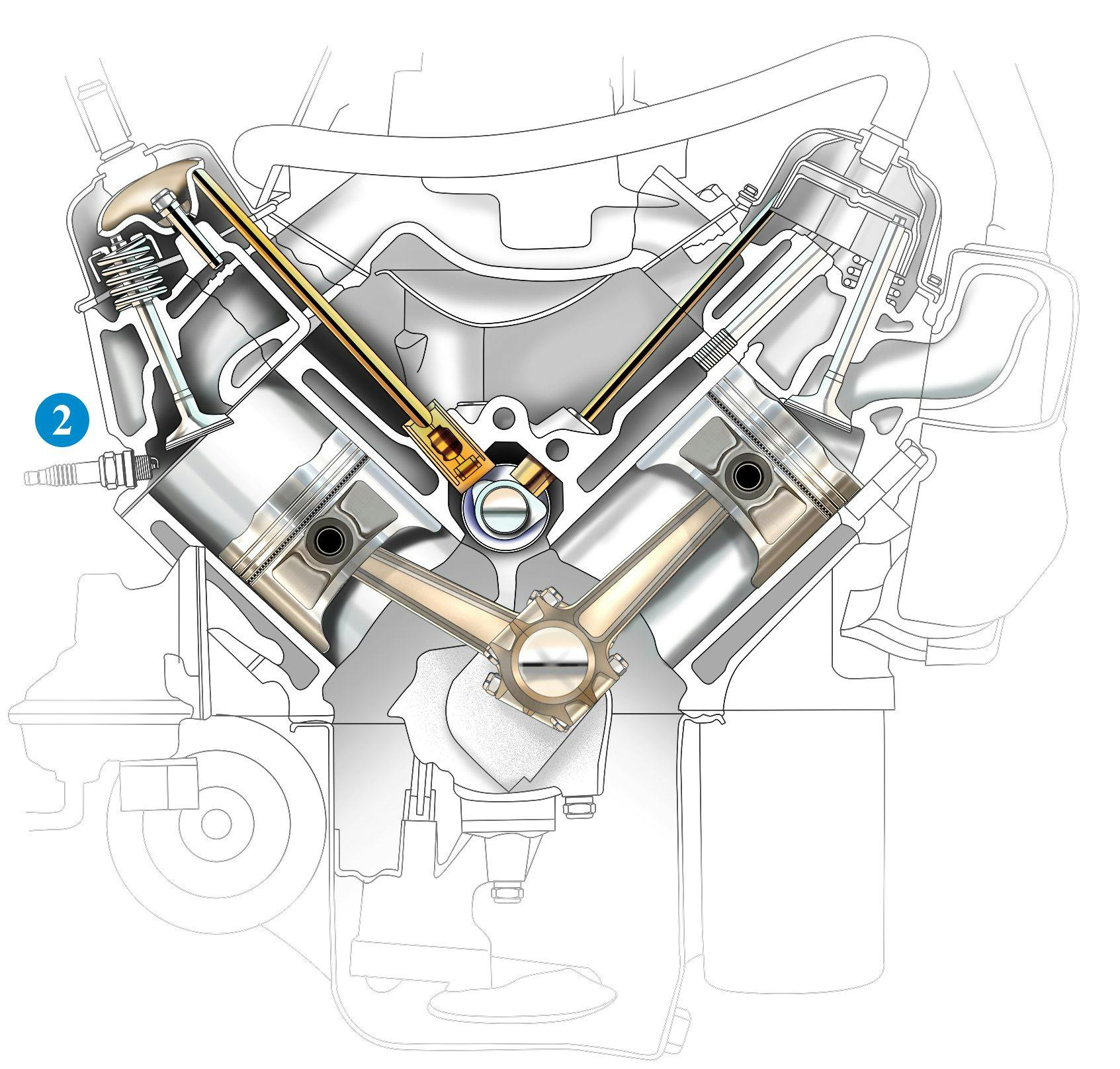
According to Weertman, the open-plenum single four-barrel intake manifold used in NASCAR achieved an impressive 102 percent volumetric efficiency at 5600 rpm, meaning that cylinders were nicely overfilled during the intake stroke. A transistor ignition system triggered by a dual-point distributor fired the spark plugs.
Fed by two Carter four-barrel carburetors atop a dual-plane aluminum intake manifold, the Street Hemi achieved 90 percent volumetric efficiency to deliver 425 horsepower at 5000 rpm and 490 lb-ft of torque at 4000 rpm in 1965 model-year Dodge and Plymouth intermediates. The single four-barrel oval track engine produced 550 horsepower at 6800 rpm. Revving to 6400 rpm, the two four-barrel drag Hemi delivered 600 horsepower.
To support a 1965 speed record attempt by the Summers brothers of Ontario, California, Chrysler engineering equipped four Hemi V-8s with fuel injection, low-profile intake manifolds, and shallow oil pans to fit inside the Goldenrod’s 23-inch-high streamlined body. Tested in the Caltech wind tunnel, this bullet boasted a modest 8.5-square-foot frontal area and an extremely slick 0.1165 drag coefficient. Each Hemi V-8 was tuned to 600 horsepower, and two of them powered each axle. On November 12, 1965, driver Bob Summers averaged 409.3 mph across the Bonneville Salt Flats to bring the wheel-driven land speed record home to America.
As with its predecessor, the second-gen Hemi lasted eight years (1964–71). Tightening emissions controls and rising insurance premiums finally retired this Mighty Misnomer mighty warrior after nearly 11,000 of them—far more than anticipated—had been sold.
Gen III 5.7-Liter “HEMI” V-8
Midway through the ill-fated DaimlerChrysler marriage (1998–2007), the need for a fresh, affordable, and efficient V-8 cropped up. Even though everything associated with Hemis was oh-so-last-century, some unsung Chrysler hero had the bright idea of trademarking America’s most prestigious engine nameplate.
So, the new 5.7-liter V-8 manufactured in Saltillo, Mexico, initially for 2003 Dodge Ram pickups (before they became RAMs under their own brand), rolled forth as a HEMI®. Forgive us for not honoring the all-caps style plus registered trademark symbol from here on.
This new V-8 was another shrewd design but not enough to prevent Chrysler’s 2009 bankruptcy. It did uphold one long-standing tradition: As in its ancestors, the third-gen combustion chamber is anything but a hemisphere. In fact, close examination reveals a very shallow bowl with two sides partially filled in to encourage quench. The term refers to the tight squeeze between a rising piston and the cylinder head that generates mixture turbulence and speedy combustion after ignition. Twin plugs fired simultaneously lit the flame. The chamber volume is barely half that of the Gen II Hemi.
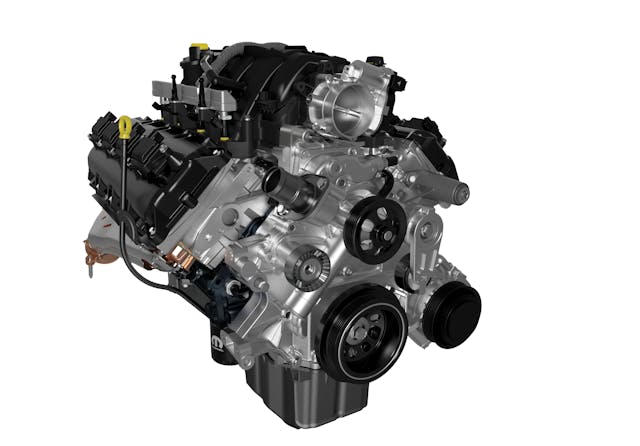
Other carryover artifacts in the new Hemi include pushrods, two rocker shafts per head, and splayed valves lying in planes perpendicular to the crankshaft. In the new compressed combustion chamber design, the angle between the valves is a modest 34.5 degrees (versus the 58.5 degrees used previously). This new Hemi followed in-depth examination of two-, three-, and four-valve-per-cylinder designs operated by pushrods and overhead cams (including Porsche’s flat-six!). Advanced computer-aided design and engineering tools were extensively employed.
The cast-iron block has a so-called “dry valley” between the cylinder banks, meaning no oil passes through here to the crankcase. Its cam is elevated above the crank by a greater than normal distance to shorten pushrod and rocker arm lengths to reduce the valvetrain weight. For manufacturing simplicity, a single aluminum casting is used for the heads of both sides of the block, with machining operations employed to modify the casting into left- and right-hand parts. The tunnels through the aluminum die-cast valve covers for the spark plug leads are cast in place to avoid oil leakage. Cast-iron exhaust manifolds, which resemble headers, were carefully tuned to optimize flow efficiency. Forged powdered-metal connecting rods tie the cast-aluminum pistons to the crankshaft. The camshaft is an assembly of forged-steel lobes and powdered-metal journals. The oil pan consists of two laminated steel sheets sandwiching an inner plastic layer to cut noise, vibration, and harshness (NVH). A tray skims oil off the crankshaft to minimize windage losses.
What Chrysler calls “an integrated air-fuel module” tops this V-8. This complex part is composed of seven chunks of injection-molded nylon plastic welded together. The savings over an aluminum intake manifold are an impressive 13.7 pounds. A built-in three-chamber Helmholtz resonator reduces NVH. The throttle is electronically controlled.
Delivering 345 horsepower at 5300 rpm, Chrysler’s new 5.7-liter V-8 topped the outgoing 5.9-liter engine’s output by a fruitful 41 percent. The torque plot was even more impressive: The new engine peaked at 375 lb-ft at 4100 rpm, a 12 percent gain, while its torque curve whipped the retired engine soundly from 1500 rpm. Compared with the 5.9 engine’s molehill, the 5.7’s torque mountain soars much higher to 5800 rpm. The best news: This was only the beginning for an engine that’s still thriving today.
Over the next three model years (2004–2006), this Hemi began powering more trucks, Jeep’s Grand Cherokee, and large Chrysler and Dodge sedans. Tech changes started arriving in 2005 when some applications began using a multi-displacement system (MDS) which switched from eight- to four-cylinder operation in only 1/25-second for improved light-load efficiency. Early durability issues were addressed and more changes came in a 2009 V-8 code-named Eagle: new cylinder heads with improved flow, plus variable valve timing and a dual-mode intake manifold to boost torque. Revised output ratings ranged from 360 to 399 horsepower, and torque peaked between 390 and 410 lb-ft depending on the application.
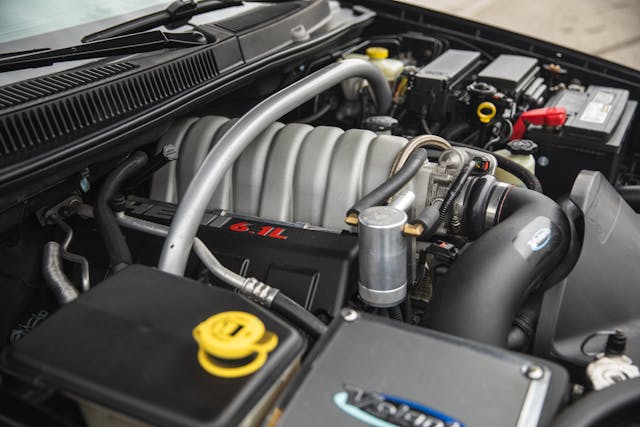
A new 6.1-liter edition with a larger bore, revised cooling, a forged-steel crankshaft, stronger rods, and lighter pistons cooled by oil jets came in 2005 for SRT8 applications. The plastic intake manifold and MDS were both omitted here. Power climbed to 425 horses at 6200 rpm and the torque peak was 420 lb-ft at 4800 rpm. Marcus Braun of Vancouver, British Columbia, Canada, won Chrysler’s “What Can You Hemi?” contest by building a Big Wheel powered by a Hemi V-8.
To salute the original Hemi of the 1950s, a new 392 V-8 was introduced in 2011 for the Dodge Challenger SRT8 and subsequent Charger SRT8, Chrysler 300C, and Jeep Grand Cherokee models. With a 4.09-inch bore and 3.72-inch stroke, the actual displacement was 391 cubic inches (6.4 liters) yielding 470 to 485 horsepower and 470 to 475 lb-ft of torque. Cylinder deactivation and variable cam valve timing were used only in models equipped with an automatic transmission. Code-named Apache, this Hemi was also sold as a crate engine.
Hell Yes! Cat
Chrysler’s now-we’re-talkin’ move for 2015 was the 6.2-liter V-8 appropriately named Hellcat, with a nod toward the WWII-era Grumman F6F fighter of the same name. Combining the Apache’s bore with the Eagle’s stroke and adding an intercooled IHI-brand supercharger inflated output to 707 horses at 6000 rpm while hiking torque to a stout 650 lb-ft at 4000 rpm. The power peak topped the 2015 Chevrolet Corvette Z06 by 57 horses thanks to 11.6 psi of maximum boost.
Hellcat applications included the Dodge Challenger and Charger SRTs and the Jeep Grand Cherokee’s SRT Trackhawk. A crate version of this engine came in 2018.
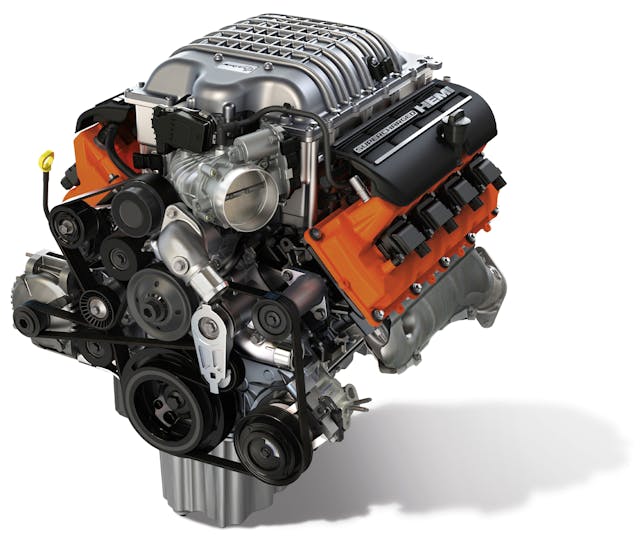
And there’s more: For 2018, Dodge rolled forth its mean Demon edition of the Challenger SRT with a 15 percent larger huffer, recalibrated valve timing, and tougher internal components. Pump the tank full of 100-octane fuel and you’ve got 840 horsepower on tap according to Dodge—or 808 horsepower if you can only afford 91-octane premium. Either way, bragging rights over the 755-hp 2019 C7 Corvette ZR1 are yours. Only 3300 cars were built and sold with a $1 kit of wheels and tires intended solely for drag strip use. Guinness World Records certified this beast’s ability to wheelie during launch. Without ever testing one, Car and Driver guessed this Dodge would clock 60 mph in about 2.5 seconds and the quarter-mile in less than 10 seconds. The manufacturer claimed launch acceleration of 1.8 g’s while a YouTube video whisked you down the Kennedy Space Center’s 3-mile straightaway to 211 mph. We’re talking Porsche 918 Spyder performance for one-tenth the price.
Whether or not you believe the hemi designation is valid for any of these engines, what Chrysler achieved beginning in 1951 and continuing well into the 21st century is astonishing. These race-winning, tire-burning, and grocery-getting V-8s power cars that mere mortals can afford. It’s not Greek to us that the Hemi deserves everyone’s respect and adulation.