The good kluge that fixed the bad kluge
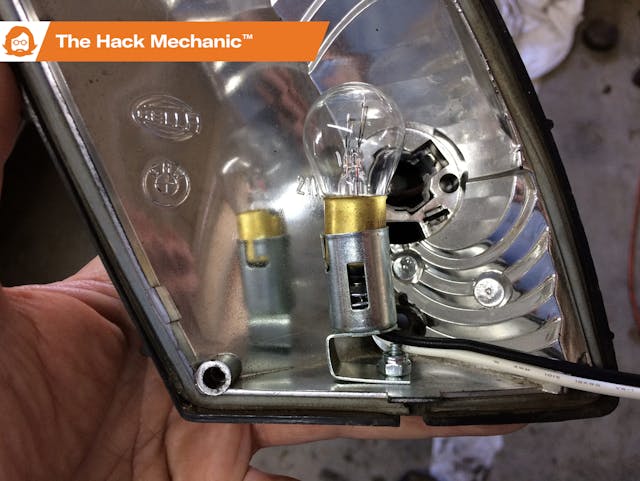
A few weeks ago, I wrote about troubleshooting a hard-start problem in my 1972 BMW 2002tii and referred to a modification that I performed—installing a push-button that manually fires the cold start valve. This kind of mod is sometimes referred to as a “kluge.” To the uninitiated, a “kluge” (pronounce klooj) is a repair that’s intended to save money, often by using a part that’s different than what the manufacturer intended. By itself, the term doesn’t necessarily have a positive connotation. I mean, welding a piece of rebar in place of a rusty trailing arm is definitely a kluge, but not a good one.
So, over the years, I’ve put forward the concept of the “good kluge.” This is one that a) fixes the problem; b) saves money; c) is safe, and d) is easily undone. The push-button cold start I wrote about was an example of a “good kluge.” I’d thought I’d give another one.
I have a Euro ’79 BMW 635CSi. European cars which were individually imported during the heyday of the “gray market” (when German manufacturers kept their best highest-performance models from American consumers) had to be federalized to meet EPA and DOT specs, and the quality of this compliance work varied enormously. Some gray market importers/converters installed genuine OE parts that were used on the American versions of the cars, whereas others saved money wherever possible, including by modifying the existing parts. One of the more trivial conversion issues was that the Euro cars usually didn’t have dedicated front “parking lights” or side-marker lights. Instead, they often had a little extra bulb inside the headlight assembly that acted as a front parking light. The degree to which, 40 years later, anyone cares about these compliance issues is generally pretty low—even in Massachusetts with its reputation for red tape, no inspection station as ever hassled me because neither the 635 nor the ’73 3.0CSi (also a gray market car) has corner markers. However, they will fail me if the front parking lights don’t work.
One day last year, after I pulled the 635CSi out of storage, I noticed that its inspection sticker had expired. I put the car through its pre-inspection paces and found that the left front directional wasn’t working. I wasn’t terribly surprised by this, as it had always been intermittent, but whereas I could usually bang and poke it into submission, this time I couldn’t.
As I said, this is a Euro car and, as was the case with other 1970s-era BMWs, the European version didn’t have front parking lights integrated into the directionals. Therefore, the bulbs in the European front corner light assemblies were single-filament bulbs and were used for the directionals only. In order to have the front corner light assemblies do double duty as both directionals and parking lights, they either need two-filament bulbs or an additional bulb. I looked in RealOEM (the online BMW parts manual) and verified that the U.S.-spec version of the car (a 633CSi) does indeed have two bulbs. I looked through the amber lenses on the car and didn’t see a second bulb. So how the hell did I ever have working front directionals and front parking lights?
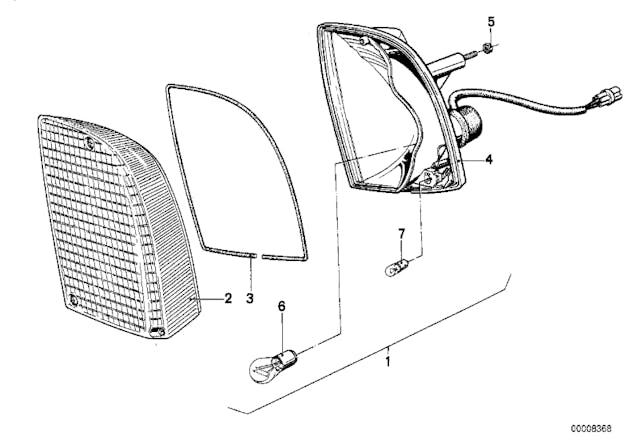
I removed the outer cover of the driver’s side corner assembly and saw something that the Euro-spec car shouldn’t have—a two-filament bulb. If that’s the case, I thought, how is it wired? I looked in the fender cavity behind the assembly and found the original, round, two-pin connector with a pigtail that headed into a rubber dust boot. But I also saw a clearly non-original yellow wire that went into the back of the assembly. I traced the other end of the yellow wire, and it vanished into a bundle of wires and electrical tape near the headlights. Like, yuck.
From the front of the assembly, I twisted the bulb to pull it out of its socket, but there was unexpected resistance when I tried pulling it forward. When I pulled it out far enough to see what was holding it back, I laughed out loud.
The yellow wire was literally soldered to the bottom of the bulb. And about half of its strands of wire were broken.
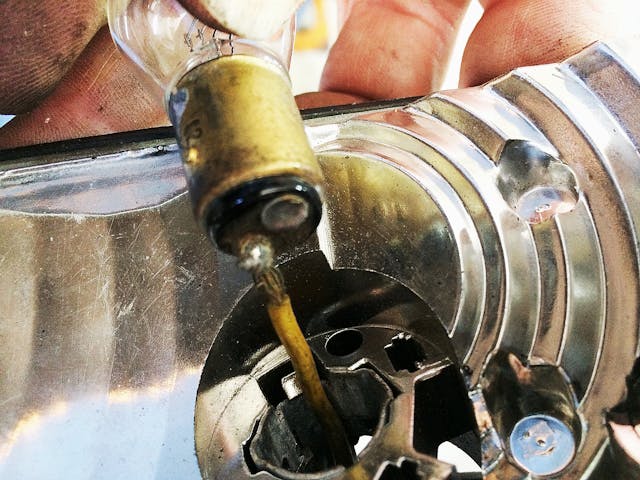
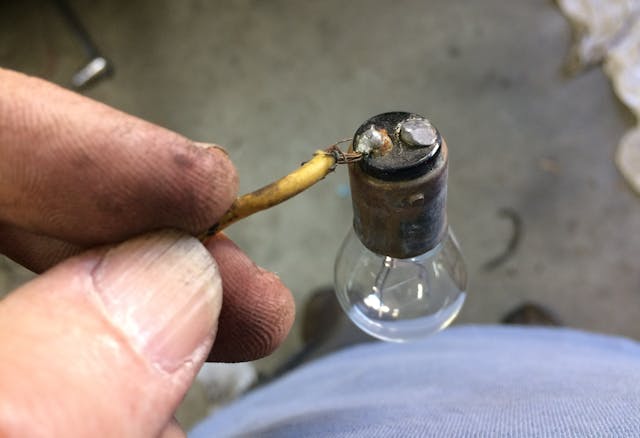
I removed the corner light assembly from the car so I could look at the back. In the picture below, you can see that the socket has two wired-in connectors. The blue and brown wires leading to them are meant for a single-filament bulb. However, this socket was holding a two-filament bulb.
Really … what the … ?
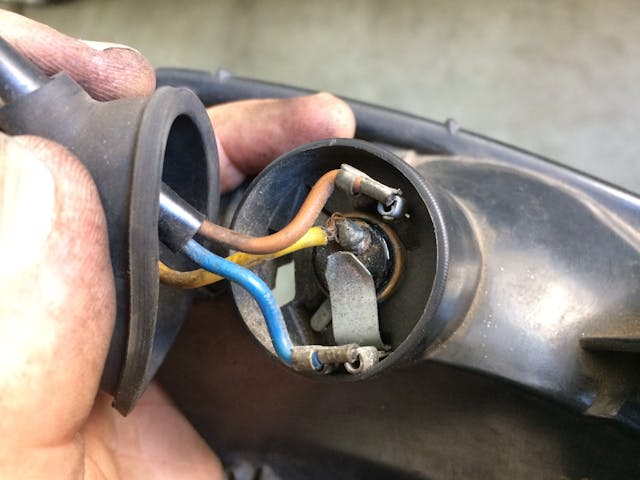
It took me a minute or two to figure it out. The blue and brown wires were the signal and ground for the directional—the stock configuration for a ’79 Euro car. The yellow wire that’s soldered in place was for the parking light. The other end of the yellow wire—the end that vanished into a mass of electrical tape—was connected to the headlights so it came on with them. I was thrown by the fact that the kluge—the soldered-in yellow-wire—was actually the part that was still working. It was the stock part (the directional) that wasn’t.
The fact that, for years, this had been more or less functional was surprising. A single-filament bulb has its contact point in the middle of the bottom. The bent-over tab that the blue wire is connected to is supposed to touch it. However, a two-filament bulb has two round contacts on the bottom instead of one, so neither of them are in the middle. It turned out that this worked, sort of, because the tab for the blue directional wire was touching the contact point for one of the filaments, even though it wasn’t in the center of the bottom of the bulb like it would be for a single-filament bulb. If you look in the photo showing the soldered wire above, you can see that the round contact on the bottom of the bulb (the one without the wire soldered to it) is worn away. This is why it was making poor contact, which is certainly why it had been intermittent for all these years.
So, was this a “good kluge?” Well, it did allow someone to federalize the car and pass annual inspection without paying for and swapping in U.S.-spec corner light assemblies. But, considering that, to replace the bulb, I’d need to solder a new one in place, I’d call that a big no.
There appeared to be three ways I could solve the problem. If I wanted to live with the existing kluge and just get the car through another inspection, I could either bend the tab forward to make better contact with the existing bulb, or solder in a new bulb. Or I could buy the proper U.S.-spec corner assemblies. They showed up in BMW’s parts catalog as no longer available (NLA). There was a set on eBay in Latvia for about $150 per side. There were some used sets on eBay as well, but they appeared to be in poor condition. Or I could buy a pair of small inexpensive LED bulbs, run their wires out the back, splice them in, and use them for parking lights.
But then I had an idea—I wondered if I could simply install a proper socket for a two-element bulb. Not surprisingly, there’s a standard associated with this size bulb and its bayonet-style twist-lock socket. The form-factor is called “BA15D.” I looked on Amazon and saw a dizzying array of them, but eventually I found a two-contact BA15D socket with integrated pigtail wires and a little surface-mount bracket, and so I bought two.
When they arrived, I was initially thrown by the fact that the sockets had two wires, not three—that is, they had no ground wire and needed to make their ground contact through the bracket. I drilled one small hole in each of the assemblies for a little bolt and Nyloc nut to hold the bracket and the ring terminal, crimped a ground wire to a little ring terminal that went on the bolt, built a mini-harness that let me pull the spade connectors off the original socket and mate them to connectors on the ends of the new socket’s wires, and put a fresh two-filament bulb in the socket.

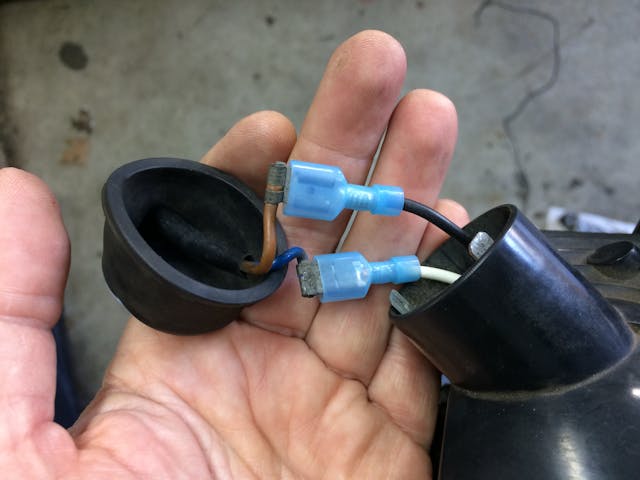
It worked perfectly. The front corner assemblies now have two-filament bulbs that work reliably and can be changed without de-soldering them.
So. Fixed the problem? Totally. Is it safe? Yes, and certainly way safer than the way it was. Easily undone? The new sockets that hold the bulbs are each held in place by a single small bolt and Nyloc nut. No original wires or connectors were cut. The original single-filament sockets are still there and can be reconnected at any time. Saved money? It cost me 13 bucks.
Now that’s a “good kluge.”
***
Rob Siegel’s newest book, The Best of the Hack MechanicTM: 35 years of hacks, kluges, and assorted automotive mayhem, is available on Amazon. His other seven books are available here, or you can order personally inscribed copies through his website, www.robsiegel.com.