FCA patent hints at cylinder head and turbocharger cast as one piece
CarBuzz noticed an interesting patent filed by FCA earlier this month. The document contains several photos and explanations of how the automaker, now known as Stellantis, could cast an engine’s cylinder head and a turbocharger as one piece.
The patent abstract describes, “A cylinder head assembly for an internal combustion engine includes a cast cylinder head, a turbocharger housing including a compressor housing and turbine housing integrally cast with the cylinder head, and a turbocharger cartridge assembly configured to be inserted into the turbocharger housing and including a shaft coupled between a compressor wheel and a turbine wheel.”
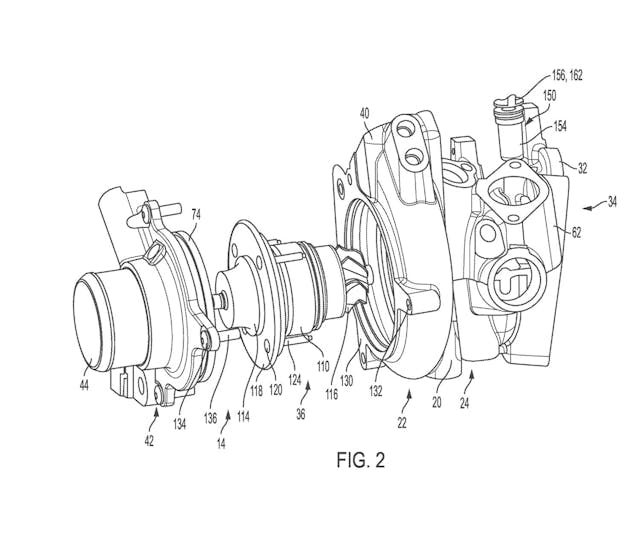
The design has the potential to streamline the manufacturing and assembly of an engine, with the turbocharger’s turbine and compressor installed as a cartridge after final machining.
Several engine families have moved to designs that incorporate the exhaust manifold with the cylinder head. For example, General Motors began integrating the exhaust manifold into the cylinder head of its DOHC V-6 engine family at least as early as 2010, and the current lineup of naturally aspirated and turbocharged V-6s continues to use a similar design. Stellantis has been incorporating the exhaust manifold into the cylinder head of its own Pentastar V-6 (below) since the engine debuted for the 2011 model year. Ford’s EcoBoost engines are similar as well.
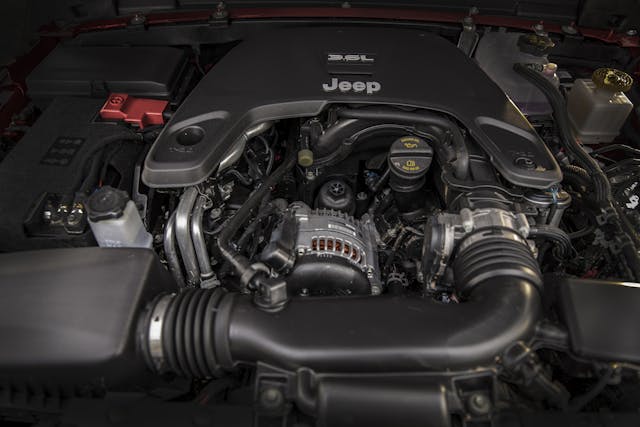
Including the manifold and cylinder head in one casting brings the turbocharger and/or exhaust catalyst closer to the combustion chamber, helping reduce emissions by lighting off the catalyst sooner. It also removes several bolts and a gasket surface, eliminating a potential exhaust leak.
Casting the turbocharger onto the cylinder head, as the patent entails, would offer the same benefits. It would place the turbine wheel closer to the combustion chamber where it could capture more of the exhaust’s heat energy and transfer it to the compressor wheel and provide boost more efficiently. It removes yet another gasket surface and another potential for exhaust leaks.
The patent also notes that the oil passages for the turbo would be cast into the turbo housing, allowing oil to drain back to the engine’s sump without requiring any additional lines and fittings eliminating yet another potential point for a fitting to fail and/or leak.
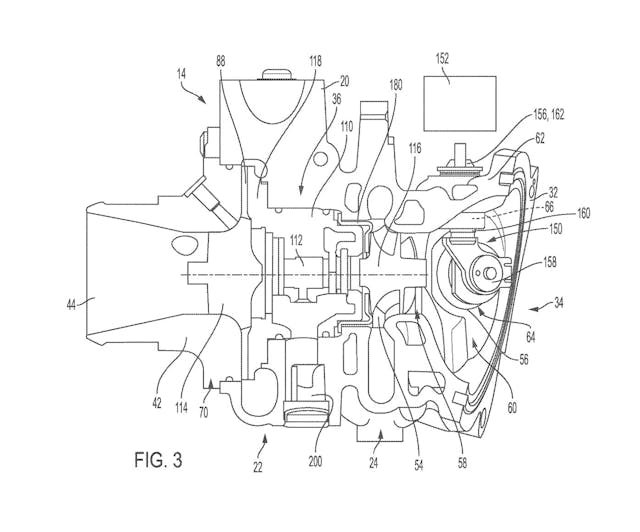
We’ve seen tremendous strides made in casting and machining in the last 30 years. The core shift common in ’60s and ’70s engine blocks that was apparent to the naked eye is a thing of the past, but there are pitfalls in making such an intricate part serve so many roles. That integrated oil passage keeping the turbo bearing cool is critical, and of course machining the deck surface, valve guides, and turbocharger cartridge mounting are all precise operations. We’re also concerned that a problem in the vehicle’s life 100,000 miles down the road might mean the whole piece could lead to an expensive repair or replacement.
Clearly, Stellantis sees the benefit in putting all of the efforts into creating such a complex casting. As enthusiasts, we’re going to miss the artistry of a perfectly routed set of exhaust primaries. Meanwhile, tuners and aftermarket manufacturers will have to get creative to improve on turbochargers if they’re hemmed in by the location and size of a fixed casting. What are your thoughts on this complex and ambitious patent?
Check out the Hagerty Media homepage so you don’t miss a single story, or better yet, bookmark it.
So when the turbo fails you have to replace the head? Sounds expensive.
I don’t think this would require replacement of the head. It would require replacement of the turbo cartridge and possibly machining the turbo housing if it was damaged. Now, if the turbo failure completely destroyed the housing, then yes, you’d have to replace the head. But if the turbo fails that spectacularly, you likely are rebuilding the whole engine.
No, Just the insert
I don’t understand the obsession with slapping turbos on every new engine. I understand that the government is forcing manufacturers to build smaller displacement engines. But they could also use superchargers and get nearly as good horsepower gains, with better reliability.
A supercharger comes with higher parasitic loss compared to a turbocharger though. Also factor in the belt to drive a supercharger and adding one more item to already cluttered serpentine belt systems. Conversely turbos often only need an oil feed and drain which can be routed all kinds of ways and the compressor itself can be moved and shifted based on chassis design. I’m not an engineer, but the more I think about it the more I see why turbochargers win out on modern production engines.
Here is what is going on.
The main reason is that superchargers take power to make power and with the Turbo exhaust gas makes power and takes no power. If you were supercharging a V8 you can afford to give up 120 HP to drive the supercharger but with 2.0 liters you can’t afford that power loss.
Also the Turbo can really make a of torque on a flat torque curve today with DI and higher compression and boost.
Also todays turbo charged engines are very reliable when built properly. I ran a 2.0 Turbo Ecotec GM engine for 10 years at 23 PSI of boost and never had a failure. The better materials and oils have made them reliable unlike the past.
The failures today are more due to design issues or part failures. The Ford RS has many issues as they installed the wrong head gasket.
I used to hate turbo engines but after my 300 HP marvel I can say I really miss it today. Yes it is still running well for the present owner.
The key too is not so much just the smaller engine but the higher boost makes for a cleaner burn and combustion. Combine that with a smaller engine it makes them very clean.
Other than by abuse, hasn’t every failure been and continue to be from design issue or part failure?
US Automakers are the only ones left advancing casting technology in the US as far as I know. The rest of the industry went offshore–along with my 20 year career in the industry–about 20 years ago. That’s a ‘spendy’ head casting you got there. The pattern technology they would have to use was aerospace use back in my day, way too expensive for automotive then. Cheap Mexican labor can overcome quite a bit of that. Wonder how they deal with the differential of water cooled head temp and very high temps in the turbo scroll? That usually spells problems for cast irons.
I agree I see a host of issues for exactly that. Cracks broken bolts warping heads. I for my part would avoid them for many years.
I would not be in favor of this as it would prove to be more expensive for the consumer.
Actually it will be just the opposite. That’s the whole point
You mean like CVTs? Cheaper to build for the manufacturer. Outrageous to replace for the consumer.
Same thing here.
Where are you getting anything that says less expensive for the consumer with this?
When the unit blows: $$$$$s.
The heat of the turbo could create a localized hot spot on the head area of the casting potentially. I would also like to see how this pattern is fed and risered for good metal flow and grain structure. If this is done wrong I could see plenty of potentials for failure just from metal flow and porosity issues. On the other side of the coin, simulation software has improved since my days too….
I’m curious about the patentability of the idea. Is it really a new idea, process or material that wouldn’t come independently to an average designer? If so, isn’t every new feature (like an accessory boss) added to an existing casting patent worthy?
It’s no surprise that FCA is leading the way in this ground breaking technology.
Molded in the finest of plastic, I’m sure.
/sarc