The Secrets of a Transaxle Built for 550 MPH
There are seemingly endless secrets in land-speed racing, which makes sense considering we have been running cars as fast as possible in a straight line for over a century. Beyond the obvious wisdom about adjusting for the environment (temperature, air pressure, race surface) and minimizing aerodynamic drag, there seems to be a very deep well of knowledge filled with solutions to other problems unique to land-speed racing. Case in point is the video below, which dropped into my feed a few days ago.
Sometimes the YouTube algorithm is terrifying. It knows me better than I know myself, and I see the proof when it serves up a video with just a few thousand views from a channel that has only posted that single video. I won’t pretend I haven’t wasted a lot of time-consuming piles of content on the internet, but low-view videos aren’t typically what draw me. But the thumbnail image of a massive chunk of billet aluminum with the text “555mph” sang a siren song. I clicked, expecting the video to be clickbait.
It wasn’t.
The video was posted by Traction Products, a business started in 1963 by Peter and Albert Weismann to engineer and produce solutions for high-performance drivetrains. One such problem is the transaxle for a car that is about to attempt a land-speed record. That component is exactly what is discussed here, from the mechanical sequential shifter to the extremely narrow axles to the fascinating reason Traction Products chose not to use a ring-and-pinion setup to turn the power 90 degrees.
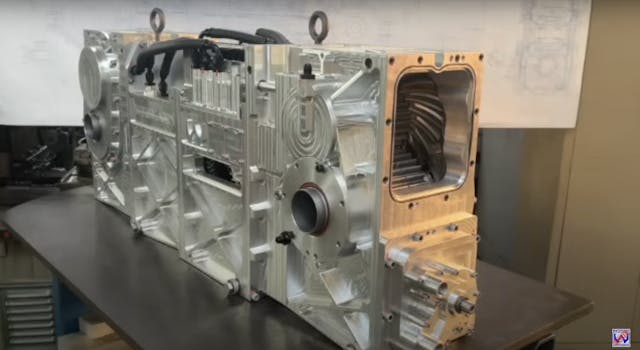
The common solutions for multiplying torque and transferring power work really well up to a point, and that point is well under the sort of output and top speeds that this team is working with: 500 mph and thousands, not hundreds, of horsepower. No, that wasn’t a typo: It takes big power to get a vehicle most of the way to Mach 1 on the ground. Multiplying that power through a dozen gears that can be power-shifted is an interesting solution in itself, but even more interesting is that the gearbox serves as the mount for the steering rack, which does not transfer power ring-and-pinion style to the axles.
A ring and pinion setup creates a lot of force and, as I learned from this video, that force is transferred to the chassis of the land-speed race car. That means the car would be fighting itself just as much as the conditions of the race course. So the Weismann transaxle uses a bevel drive to turn the thousands of horsepower, a decision that keeps the twisting force inside the billet case of the transaxle. Voilà: the chassis works like it should rather than fighting itself.
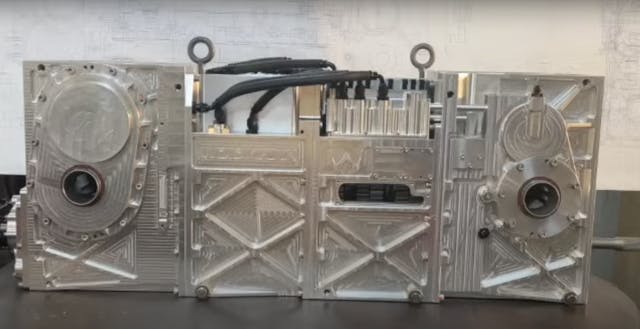
There are all kinds of problems in racing, yet few people get to chase solutions with the mad scientist minds that Traction Products does. It’s fascinating to see a company share its ideas and experiences so freely and we can only hope for more videos and stories from this shop in the future.
***
Check out the Hagerty Media homepage so you don’t miss a single story, or better yet, bookmark it. To get our best stories delivered right to your inbox, subscribe to our newsletters.
Amazing machine work. ..
I recall Don Garlits tried to put a Top Fuel engine in side ways to use the torque to push down on the rear of the car. He used the power take off from a tractor pull tractor. But he kept breaking them.
The transfer of power is difficult as while the engine holds the reast of the car pausys the price.
“…reast of the car pausys the price.”
Uh… WHAT?
Turning the engine sideways was tried even before Garlits. I remember a dragster called Sidewinder that did this and I think even Chris Karamisins (spelling?) drove it or maybe a different car, hard for this almost 80 year old to remember all those experiments that were tried back then.
The Sidewinder got a few pages in HRM rotogravure, those greenish center pages, and was a neat piece of work! It, as I recall, was a chain-drive from the rear hemi to a solid-shaft rear axle. Seems like they had the traction with that weight transfer, but were plagued with a hopping problem, and coudn’t exploit it. Also almost 79…
Fascinating! We have been tasked with engineering and developing a working prototype final drive for off-road and our first choice was… bevel gears. The housing is being designed and hopefully we will have a working model by the end of the year. This application won’t be dealing with thousands of HP, but should be overkill for what it will see.
That thing is a work of art. So shiny too! :^)
I too recall reading about the Sidewinder. Wasn’t it Cadillac powered?
Pretty sure it was a hemi. Never saw it run, tho. Our local strip (Shasta Roadsters, Redding CA) often had a ’34 Ford coupe with a rear hemi (as I recall) providing the oomph, but he never sorted out his traction control problems. Prob. had solid mounted axle, but I don’t know. Bounced such a series — almost out of control — from the start so hard that his trunk-lid flew off, and littered the strip with an embarrassing amount of Bondo bits! Pretty cool, tho, for out in the sticks!
Transaxles are fascinating, and have a looong history in automobiles, back to the very beginning! My fave is a factory race car Pontiac Engineering built for John DeLorean from the 1963 Tempest, the so-called ‘Super-Duty’ or ‘Powershift’ racers that used two ‘TempesTorque’ (aka Corvair Powerglide) automatics to make a 4-speed transaxle for drag racing. That is a long sentence!!
The year previous, Mickey Thompson had built two ‘Super Factory Experimental’ Tempest coupes for NHRA, with the nominally 405-hp 421 engines, but he gutted the drive-trains and put in B-W T-10s with 9.3-in rear ends from the big cars; saved almost half-a-ton of weight. Won top stock times at the ’63 Nationals (Hayden Proffitt, I think, driving). The ’63’s used a regular racing clutch for first-gear engagement and out of the traps, but then shifted ‘automatically’ three more times. It was very well documented in the car mags, but then GM pulled Pontiac and Chevy out of racing. No more money, no more parts, period. One S-D Tempest was set up for oval and road-course work by Ray Nichels garage, race 50; it ran USAC so the 421 used two AFB four-barrels on the famed ‘bathtub’ manifold, and won the Daytona Challenge Cup 250 against Ferrari GTO of Pedro Rodriguez, and GS Corvette of AJ Foyt; Paul Goldsmith was driving the Poncho. It got featured in TIME Magazine for the upset, and won by five miles! Urban legend says MBZ bought it right there, and it was never seen again! Amazing lash-up of dual transmissions, but it was indeed built in PMD shops! Some were later converted to regular Hotchiss drive axles, and had their wheelbases altered; probably the genesis of the ‘funny car’! Wick formerly contributor to SPECIAL INTEREST AUTOS Magazine, Old Cars, etc.