Is this the next great leap for internal combustion?
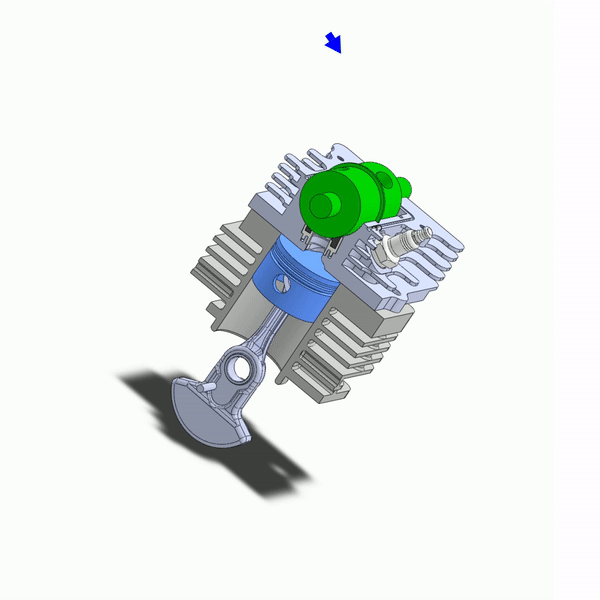
We may have been doing this wrong all along. With cylinder heads, that is.
Back when it all began, steam was the start—how we first captured heat energy from fuel and put it to work. More than a century ago, steam powerplants formed the basis for the design of the first internal-combustion (IC) engines. Moving the combustion from an external source (a steam boiler) to the inside of the drive cylinder was a major step forward in power and efficiency.
Since steam engines were laying around all over the place, many parts were carried over. Components like pistons, connecting rods, and cranks were near-enough correct to make a gasoline engine sort of run, and things evolved from there. The sliding sleeves and popular barrel valves used to control the flow of high-pressure steam, however, did not make the cut. They leaked.
Leaking a little high-pressure steam here and there is not of major consequence in the grand scheme of a locomotive. Because cylinder leakage carries real drawbacks with an IC engine, sleeve valves and barrel valves were abandoned, replaced by a kind of valve called the poppet. The type of valve now found in almost every four-stroke IC engine on earth.
Poppet valves were and are a decent fit for a four-stroke’s high internal pressures and combustion temperatures. Mated with a countersunk seat, the poppet’s chamfered face forms a positive seal, and that seal improves as pressure on the valve face increases. Although they require complex drive and support systems (cams, keepers, springs, lubricated guides, etc.) poppets have been developed into a reliable solution.
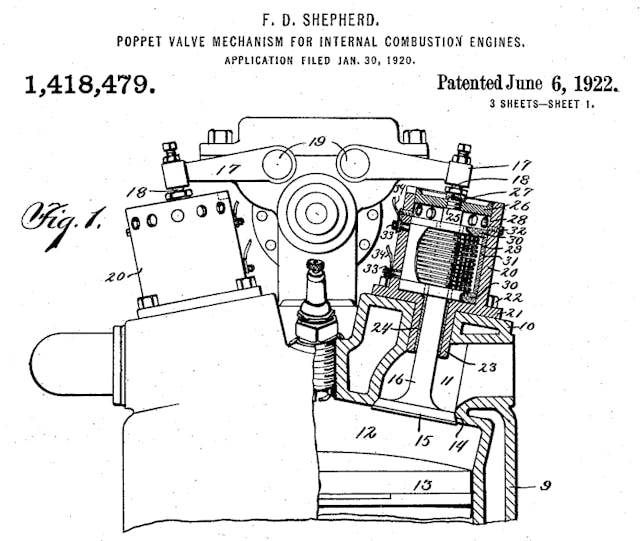
What we gained in reliable sealing, though, we lost in flow. A poppet valve’s head is always in the way. On the intake stroke, a poppet valve’s head blocks about 20 percent of the air trying to fill the cylinder. With the exhaust stroke, the valve is essentially attempting to evacuate a crowded theater through a door that won’t fully open. The piston is rising, pushing combustion byproducts out the exhaust port, but the valve’s head is in the way.
In the case of the intake valve, we’ve evolved to a sweet spot where a poppet can flow more than 100-percent capacity—more air can be moved past the valve and into the cylinder than the dimensions of the intake path and cylinder would suggest. But that’s due to the velocity of the incoming airstream, the air “ramming” itself past the valve’s head. (For an exaggerated illustration of this effect, see the now-outdated Japanese “subway stuffers”—they were literally ram effect personified.
This is no small issue. Every engine is, in essence, a dumb air pump, limited in its ability to bring in air. Burning gasoline and exhausting high-pressure gases are pretty easy tasks by comparison.
Cylinder filling has been the problem for two centuries, since we began moving away from steam. The column of air sitting over the earth weighs only enough to create around 14.5 psi of ambient pressure at sea level. When it comes to pushing air into a vacuum—like the one created by a piston moving down a cylinder—that pressure isn’t much. It’s even less at altitude, like on Pikes Peak, where the mountain’s height leaves the air column above short enough to give less than 9 psi. (Ever wondered why turbo- and superchargers predominate on race cars run at altitude? Now you know.)
After 100 years of being fussed with, the poppet valve is, in a sense, grandfathered in. It is now highly functional but not optimal. We have band-aided the poppet’s poor performance partly by increasing the number of valves—some cylinder heads have four or more per piston. Over the last century, however, the inventive human mind has tried to revive certain steam-engine concepts, to take advantage of their superior flow ability.
During World War II, when air power was the ultimate arms race, engine designers on both sides dusted off the concept of sleeve valves. By configuring those valves around pistons, they found tremendous power improvements. (While also making massive progress in the development of things like high-octane fuels, superchargers, turbochargers, and nitrous-oxide injection—all over the span of about five summers.) The power increases came mostly from the airflow made possible by those sleeve valves, a clean and unobstructed path from intake port to cylinder, no poppet head in the way.

This improved air flow was put to good use: A fighter plane that can out-climb or outrun an opponent can easily turn and shoot them down. For all the benefits brought by their improved flow, though, sleeve valves leaked oil, they wore out too quickly, and they required monkey-motion levers in the crankcase in order to work correctly. The technology never made it to automotive production in any significant form.
Still, the siren song of full flow capacity is hard to resist. And like the sleeve valve, the barrel valve—a type of rotary valve—has long captured the fascination of engine designers.

A shaft with a slot cut into it, rotating in seals, is so simple and capable that it has been tried dozens and dozens of times. Where a standard poppet valve may peak at flowing 85 percent of its intake area (and then only temporarily, when fully open), a rotary valve opens faster and can flow 100 percent of its intake area more of the time (meaning, over more of the valve’s opening duration). If you have a 5.0-liter engine that can only breathe at 85 percent of capacity, you don’t really have a 5.0-liter engine. One-hundred-percent intake-valve flow makes more power every time.
With the barrel valve, the gremlin has always been sealing. For a long time, any seal material that pressed against a barrel valve’s shaft enough to contain combustion pressure—upwards of 1500 psi at 2500 degrees Fahrenheit—would also give high friction and wear. If you loosened up the seal’s tolerance on the shaft to reduce that friction, it would leak. Either way, the high temperatures ate away at any sealing material tried.
The industry birthed prototypes, test engines, and a few production attempts, but no rotary-valve design or layout has been fit for real commercial success. Felix Wankel, the inventor of the rotary engine, started his career developing disc rotary valves that were eventually used in German torpedoes. In 2004, the Mercedes-Ilmor Formula 1 team got as close to the summit as anyone, with an adaptation of a rotary valve patented by a man named Bishop. But alas, F1’s (power-hating?) sanctioning body responded by outlawing any valve not a poppet. So much for racing promoting innovation.
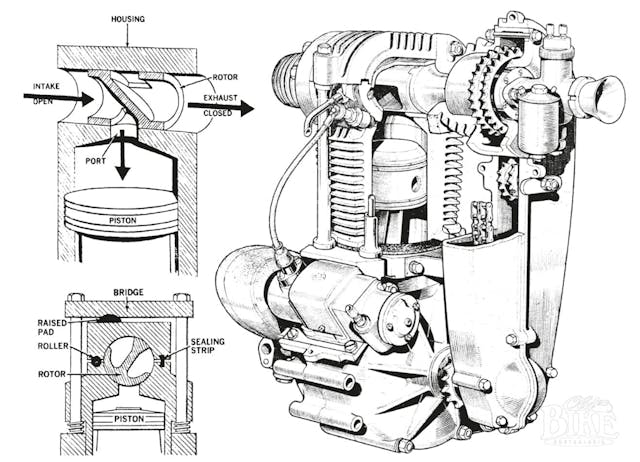
All hope is not lost. As part of my work as a professor of IC Engine Design at UNC-Charlotte, I was called to consult in “Race City, USA” (a.k.a. Mooresville, North Carolina, home of NASCAR), to assist a company that had found a way to seal a rotary valve and take advantage of the potential.
That company, Vaztec, was founded by a team of engine developers who had supported GM and Ford racing for decades, and who had grown disillusioned with how badly a poppet valve actually flows. Now six years in, they have just returned from a Society of Automotive Engineers conference in Japan, where their white-paper presentation on a successful rotary-valve design won an award.
Maybe time is nigh for a change.

Vaztec has developed and patented a dynamic, high-temperature sealing system that adapts to the shape of a rotary valve as it expands. That expansion is the true Achilles heel of a rotary-valve system. Almost all metals expand as they heat up. If your valve seal relies on a thousandth of an inch of clearance to work, as many automotive seals do, having that valve grow three times that amount as the engine warms is a recipe for failure.
As the Vaztec project advances, some interesting side benefits have appeared. One is a cooler-running valve. The poppet is a sitting duck in the combustion chamber, exposed to 2500-degree combustion gases during the piston’s power stroke. Then, during the exhaust stroke, the valve’s head gets stuck in a jet blast of 1400-degree exhaust. Milliseconds later, that head carries leftover heat into the engine’s next power cycle. Because a barrel valve is constantly turning, heat transfers more evenly into the cylinder head.
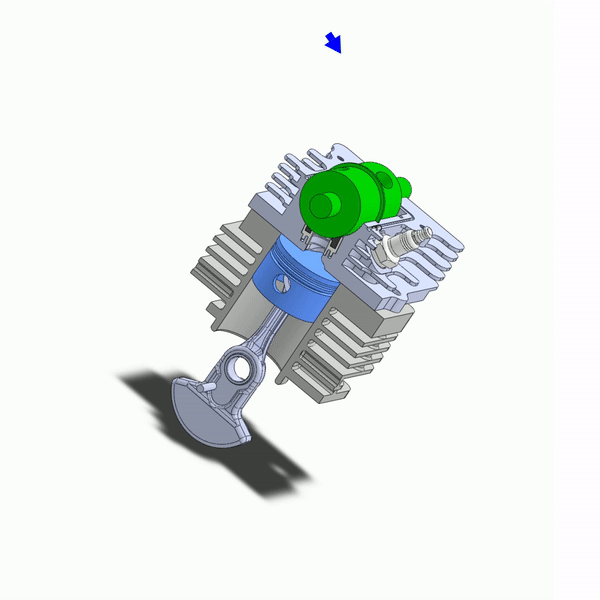
That heat transfer is helpful. At peak power, the head of a poppet exhaust valve can serve as a “glow plug,” growing so hot as to spontaneously ignite fuel and air. Lowering an engine’s static compression ratio helps alleviate this; by the same token, if you eliminate the glow-plug effect, you can make that ratio higher. All else being equal, higher compression ratios improve power and efficiency—a strong step toward keeping the IC engine alive and relevant in years to come.
Those benefits were somewhat expected. An unexpected byproduct of unobstructed intake flow was the increased, and now very high, velocity of intake air as it rushes into the combustion chamber.
Intake air gets up to crazy speed in high-load conditions—Mach 0.55, or around 450 mph. That velocity is what drives the aforementioned “ram effect,” the jamming of a combustible air-fuel mixture into a cylinder. That velocity generally produces turbulence, which stirs up and quickens the combustion process, aiding power.
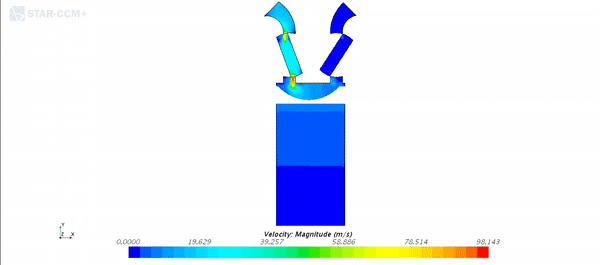
Interesting side note: A few decades ago, I had a fascinating conversation about intake velocity with former Car and Driver editor Gordon Jennings. He proposed Mach 0.9 as the actual goal—near-sonic airflow. Even then, however, things would still be greatly disturbed by the poppet valve’s head, which hangs out at the end of the intake port like a bouncer at the entrance to a party. With the bouncer gone, things change. Rather than an orderly “deflagration” (picture of a sheet of paper lit by a match at one corner, the flame moving slowly to engulf the page), we get flame-folding and combustion that takes place much more quickly.
This is a different type of cylinder process than we are used to, one highly efficient, very rapid, and very useful. A telltale is how Vaztec’s development engines have required roughly half as much ignition-timing advance as they would with poppet valves. Because the fuel-air mixture burns quicker, these engines can fire their spark plugs later in the compression stroke, which lets them make more power—the force of the cylinder’s burn is no longer trying to shove the rising piston back down. (With slower combustion rates, this is a very real “taxation” cost of advanced ignition timing.) The greater turbulence also sweeps lazy end-gases into the combustion party, giving less time for detonation sites to emerge in the chamber.
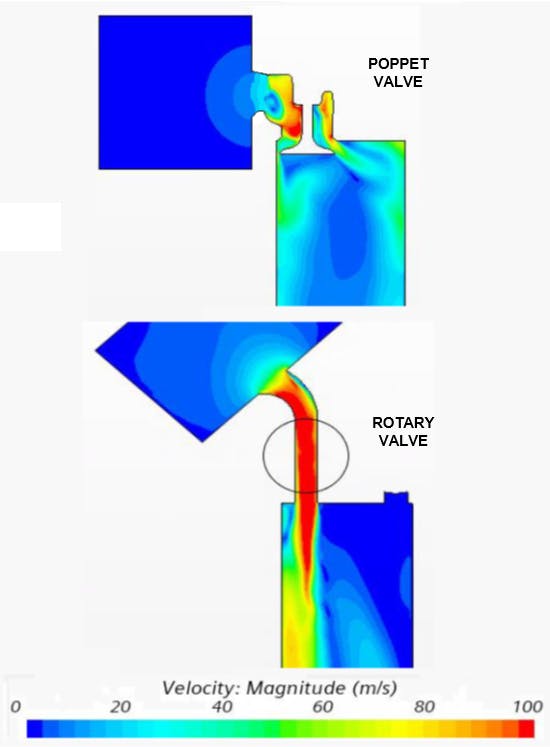
Designing a new engine system is one thing. Actually getting it to run is another. Six years ago, Vaztec began developing its rotary valve inside, of all things, a diesel engine. Diesels use extremely high combustion pressures, up to 2500 psi, so this was a tall bar, but also a fine way to prove the idea. Next, the company set its sights on the power kings of the engine world: two-strokes.
A two-stroke cylinder has a firing cycle every crankshaft rotation. A four-stroke fires only every second rotation, half as many power pulses for a given rpm. Although two-strokes excel in power output per cubic inch, they offer relatively poor control of incoming and outgoing gases, and that serves as an upper limit for output. (My ’72 Bultaco 250-cc two-stroke motocross bike made 144 hp per liter when I raced it 45 years ago, and Honda’s two-stroke, 500-cc NSR 500 grand-prix bike made 400 hp per liter in the 1990s. Compare these to the laudable 5.5-liter V-8 in the current Corvette Z06, which makes 122 hp per liter. What two-strokes don’t do well is run cleanly, which is why federal emissions regulators are eyeing them for eventual banishment.)
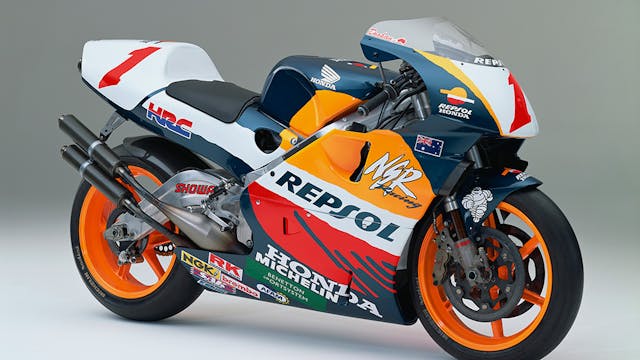
As a test, Vaztec set its sights on making a high-power, clean-emissions replacement for a 50-cc two-stroke, in the form of a rotary-valve four-stroke. This was the topic of the award-winning SAE presentation mentioned earlier. Vaztec’s rotary-valve, 45-cc single matches the power of a production 45-cc two-stroke chainsaw/weed-trimmer engine, and it can rev just as high (more than 12,000 rpm). It also made 50 percent more power than a similar, 48-cc four-stroke poppet engine currently on the market.

About that rpm peak: Poppet valves give an engine an upper speed limit by nature. At extremely high rpm, a spring-closed poppet valve will float—hover off its seat, unable to fully close and seal before the cam that controls the valve forces it open again. Since a rotary valve spins like a shaft, supported by bearings (imagine a camshaft without lobes or loads), it lacks that traditional limit. That Mercedes-Ilmor F1 engine easily spun above 20,000 rpm, limited primarily by the strength of its crankshaft and connecting rods.
For a more automotive-scale test, Vaztec has developed a one-cylinder engine with two rotary valves, one each for intake and exhaust. This engine uses a 90-mm bore and a 70-mm stroke, which makes it comparable in size to one cylinder of a 1.8-liter in-line four. It currently makes 50 percent more power at 4000 rpm than the similarly sized poppet-valve engine that Vaztec chose as a baseline. Very promising.
On the endurance front, Vaztec has built ten prototype engines over the past six years, from a 28-cc single to a 5.3-liter version of GM’s LS1 V-8. The company’s engineers have hundreds of hours of durability tests showing scalability and strong results. The valve itself is simple, with very little to deteriorate. Even at these early stages of development, wear rates of these prototypes extrapolate to an engine life exceeding 5000 hours.
At the moment, Vaztec is working with engine manufacturers to scale the technology into powersports, and eventually automotive-production applications, including hybrids. The greater power density, improved combustion, and increased efficiency are coupled with reduced noise, reduced vibration, and reduced wear. On top of that, those benefits are brought by a system that uses 33 percent fewer parts than a traditional poppet arrangement, that requires no special materials or processes to create, and that costs less to make and assemble.
An added bonus? No valve adjustments for the life of the engine. And we get to keep our pistons and crankshafts.
While most of the advances in engines in the past three decades have related to controls like direct fuel-injection and variable valve timing, it seems we’ve found a way to improve the fundamentals once more.
Could the poppet valve go the way of the choke lever and dashboard cassette player, into the dustbin of history? Perhaps, just as carburetors have been largely replaced by fuel injection, rotary valves will take over. We shall see.
***
Full Disclosure: Norman Garrett is an engineering consultant for Vaztec and has helped develop the company’s rotary-valve technology. He is a freelance contributor to Hagerty and was paid for this story.
Check out the Hagerty Media homepage so you don’t miss a single story, or better yet, bookmark it.
This is some real engine-nerd stuff and I for one and here for it. Extremely promising tech for us ICE enthusiasts if it can be scaled and licensed (or whatever the final intention may be for business case). One question that pops to mind is I am wondering if the rotary valve have an impact on the aural qualities of an ICE engine. Does the rotary-valve LS sound the same as a poppet-valve LS when running?
It all comes down to “Vaztec has developed and patented a dynamic, high-temperature sealing system that adapts to the shape of a rotary valve as it expands.”
As discussed, there is nothing new here, just a team saying they have solved the valve sealing issue.
The question that comes to my mind is;
“Have they solved this sealing issue, and how?”
My thoughts exactly….
That is the “secret sauce” that the company must protect as proprietary technology until they can patent protect it. Until the concept is patented, anyone can use whatever information is published for their own ends, including “reverse engineering” the concept. The author is employed by the company, so he is naturally on the horns of a dilemma. He must publicize the idea, to get funding and support for the product, but not give away so much information that he gives any potential competitors an advantage.
I have the same question. My thoughts are that sounds “under the hood” would change with the absence of valve train “clatter”. As to the exhaust I imagine that higher flow velocities result in a different “pitch” as air moves more efficiently out of the ports and down stream. I would love to see/hear such technology as I imagine it would sound glorious as rpm builds.
From the few power curves shown in the article it looks like the operational RPM range is going to be much higher. That will certainly change both the pitch and ring of the exhaust note. It makes me think about the difference sounds between a 250cc Honda CB from the 60s and a 250cc Yamaha TD from the same era.
It does not sound the same. No mechanical clicking or lifter noise.
The same can be said of most of the hot rod crowd. They want a “lopey” sounding idle. I’m constantly telling people to just pull one spark plug wire on their stock V-8 — they will get the sound they want. “Yeah, but that affects power and how it runs”. SO DOES THAT “LOPEY” IDLING CAM!! The engine isn’t running very good at low speeds, that’s why it sounds that way. Fine for a race car that needs to make power at 5000 rpm, but not for a street car that you’re going to be running in the 2000-3000 rpm range most of the time.
Kevin, remember the rotary Mazda RX2, 3, and 4 from the late 60’s early 70’s? The engine was so silent you could rev it up into the teens and blow it up while it sounded lik a high whine at a little faster than corvair idle.ultimately Mazda tuned the exhaust system to make the noises we all love as the engine turns up. I’m sure this noise technology can be brought back.
When you get rid of the valve noise, assuming the rotating part is well balanced, the only thing generating noise is the combustion. There is a heck of a lot of clacking you don’t normally hear over the combustion noise, but it is there generating vibration.
Interesting that they’re investing in a new kind of ICE engine design when we’re all supposed to be moving to electric. And GM is investing a billion dollars to develop a new small block? Hmmm. Maybe whoever is really running the world knows this E-car fad isn’t going to stick. Maybe Big Oil is still in charge… Remember how they blocked the development of and engine that runs on water? (Just kidding. Kind of…)
I think there is room for both. I’m a huge fan of electrics, which is a good thing, since the manufacturers are all heavily invested in them, so that horse is out of the barn. They provide a pathway–admittedly an imperfect one–to greener energy that our ever-more-obvious climate crisis demands. They are the answer to a lot of questions. But they don’t threaten my collection of old German cars from the 80s and 90s in the slightest.
I agree!!
Once we can’t get enough of rare earth metals the EV world will likely get its comeuppance.
Slave labor gets those rare minerals for about a whole dollar per day. Now that’s living.
Remember “Chicken Little”. That principal can be applied climate, disease or anything as long as the public panics and cowers to their government master.
Yep, we should not let facts get in the way. When we opened the Trans Alaska Pipeline in 1977 we pumped 112 million bbls. By 1988 when we had the wells at full throttle we got up to 744 million bbls. Since 1988 it has been in a steady decline to 176 million bbls in 2022. Oil is not a renewable resource. Yes we may find more pockets around the world but we will exhaust the supply. No government interference here, just man’s depletion of a finite resource.
Hasn’t COATES produced industrial engines with these identical claims (including having solved sealing and durability) for at least a couple decades now?
Where do you get your info? sources are important.
Umm… okay.
Coates International has been working on rotary valve heads for more than a couple decades…
https://www.coatesengine.com/csrv-system.html
I don’t think the issue is so much that the e-car thing is a fad. I’ll buy one when my daily driver wears out but it still can’t replace my truck.
It’s just that the energy density of hydrocarbon fuels still can’t be beat! There are lots of applications for engines where ICE may still be the best way to go. I’m thinking standby-by power, temporary power, ships and so forth. Not to mention in my truck for pulling the toy-hauler to the river! There may come a time when an e-truck will be usable for hauling a 8,000 pound trailer 150 miles each way but that day is not here yet.
I’ll start by saying I’m an old school ICE devotee. IMO E power is evolving from a “fad” to an accepted tech that will continue to grow. BUT, we as a species are resistant to change. ICE Power will remain as the primary driver of our vehicles for at least another 30/50 years. If there are technologies that make ICE more efficient and cleaner that could further expand the ICE lifespan.
I agree – this sounds intriguing, but I think the timing is off. Maybe 20-30 yrs ago but like you said, we are moving to EVs – maybe there is a niche for this application?
You mean Deuterium or Hydrogen , works great in ICE’s we even raced on 99.9% Alcohol!!
Cheers.
Cool stuff to think about the possibilities. Much higher rpm potential. No excessive spring forces trying to flatten tappets or destroy roller bearings. I could envision a longitudinally sliding mechanism to control the opening size, thus providing a form of variable valve timing. Neat article!
Variable valve timing can be done by using an electric motor to drive the rotary valves instead of it being crank driven.
When I first saw the headline for the article I thought some breakthrough had been made for a cam-less engine. Fiat and others have been using solenoid driven poppet valves in production engines for a few years to create variable valve timing all driven by the onboard engine control unit. First there was the removal of the distributor by Ford and now the camshaft is obsolete.
Not mentioned here, but in my opinion important, no valve clearance issues (interference vs non-interference engine designs) so no trashed engines from a blown timing chain or belt. In fact, a blown chain or belt in this case would have minimal impact other than the engine shutting off.
Its a lovely idea on paper and even as a “one off” but the sealing of the rotary valve as it rotates is the same issue we had with the NSU and even Mazda wankel engines, sealing the gases, and high temp exhaust gases is incredibly troublesome. The biggest difficulty was starting from cold, once it was running and up to temp all was fine! Would love to see and hear a modern version though.
The other issue I anticipate is lubrication. Keeping that valve lubricated, and keeping the oil out of the combustion process. This is why all we pretty much have these days are reciprocating piston engines with poppet valves. I also suspect that the significant amount of rotating mass will have some measurable impact on engine performance. Exactly how tolerant are those massive camshafts going to be to rapid changes in RPMs?
The wankel issue is due to the cross-seal and side seal problem of the trochoid(?) combustion chamber(s) on the motor. This appears to be a rotary motion seal that has many decades of seal development experience…the actual port seal is no worse than a two-stroke. I like the idea.
Really interesting piece–and excellent descriptions of how the various valves work.
Yes, this is a really interesting take on improving ICE. I hope the R&D enables us to come up with something viable. Thanks for the story, Norman – well writ! 🙂
Similar systems have been looked at and passed over.
I look to F1 who try anything and everything for an advantage and they never resorted to this. We saw pneumatic valves and all sorts of other things.
As for those who think EV is a fad it is not. It is coming no matter what due to regulations. As to when and how the changes come they can be a bit variable.
Like the GM V8 that is coming, They will keep ICE alive as long as they can in the models they can afford to do so. The Corvette and larger trucks will be the prime movers of these while half ton will see mostly EV production at some point.
Regulations are different for specific weight classes.
Trust me the MFGs are not spending billions on EV programs to not use it.
The ICE that we will have in the future will be limited to specific needs and models. Also expect penalties to be paid to have one much like the gas guzzler taxes.
Most companies will be doing as GM is doing. Marketing EV models but selling ICE models beside them. We already have two Blazers and soon Equinox will have a ICE and EV model. The Colorado will soon follow and we already have a Silverado EV but the ICE one is not going away for at least a decade.
The trouble is regulations are difficult now and the laws that are coming in some states and countries will prohibit the sale of ICE in most classes no matter the emissions.
While EV is not the end of the world I just wish they would let this all happen on its own and not force the public to change until they want to.
PV on F1 engines were a great solution until rpm limited and boost a thing that overpowered high rpm (pun intended).
Like I have always said, you can pass a law that says all major cities must have starship ports by 2035. When 2034 rolls around and there are no starships… guess what. Now the electric car has been more successful that I thought it would be, and there are a lot of folks who can fit them in their lifestyle, but we are already seeing some of the pretty obvious flaws in the system, and I suspect fairly strongly that ICE cars are going to be with us for quite some time.
They don’t care if it’s feasible. They probably know it isn’t. You can’t afford to drive or can’t charge the car because we keep shutting off the power? That’s too bad. Stay inside and eat your bugs, peasant.
Failure isn’t a bug. It’s the feature
Cool article! Hope this innovation makes it onto BMW’s in-line sixes and the company also decides to go back to its more standard and more estheticly pleasing grill designs. Would make for a fun three series!
When are the engineers going to quit using that stinking stupid problematic belt drive in their designs? I don’t even like seeing drawings including it.
Not sure I understand. If this technology solves the complexity of conventional valves and the lubrication issue at startup and when cold, why doesn’t the rotary engine benefit from similar technology. Mazda has re introduced the rotary engine as part of their new hybrid package..seems to be best of all worlds..Compact, smooth running, no reciprocating mass energy consumption and electric drive to keep in optimum range. Imagine an F1 power unit which has one shaft for ED, IC and turbo boost.
For all that love engines that run on fuel, myself included, remember this please. Car companies will make the most inexpensive engine they can as long as it meets government requirements. Remember the absolute garbage they were pushing in the late 70’s and most of the 80’s? Car makers hate us, if you want proof, look at a new fuel injected 4 cylinder, they put out as much or more power as a V8 from the 1960’s, it got worse in the 1980’s. Car makers knew about fuel injection computers in the 1970’s but those would have reduced profits.
Bosch had fuel injection in the 1960s, just not much computer control.
I think by your remark you are a youngster. Bosch had direct fuel injection on their bf109 Messerschmitt Daimler-Benz 601 and 605 engines during WWII. This enabled these aircraft to pull negative G in a dog-fight giving them an edge. The allies never did employ the technology during that war. They did however develop pressure carburetors which was a step in the right direction.
You are right on computer control but Bosch did have barometric compensation at least. There were many computers during WWII, it’s just that they were analog not digital.
The “Big Three” were behind the innovation curve because they were selling all the cars they could make at an obscene profit, and with gas at $0.30 per gallon, fuel economy was a non-issue. The Europeans had to invest in technologies that gave better fuel efficiency, because fuel was so much more expensive in Europe. Then OPEC shut off the oil spigot, and everything changed, literally overnight. When gas went from $0.30 per gallon to over $1.00 per gallon in six months, fuel economy suddenly became VERY important! I knew that Detroit was behind the technology curve when the VW Beetle got Bosch fuel injection before Detroit could even spell fuel injection!
The author mentioned that F1 disallowed anything but a poppet valve after introduction of the Mercedes-Ilmor design in 2004.
It all comes down to “Vaztec has developed and patented a dynamic, high-temperature sealing system that adapts to the shape of a rotary valve as it expands.”
As discussed, there is nothing new here, just a team saying they have solved the valve sealing issue.
The question that comes to my mind is;
“Have they solved this sealing issue, and how?”
BUT……..It is still a Four Stroke engine and the highest efficiency it can achieve is 50%. 50%! Half the time reciprocating parts are being pushed around by the other half of the reciprocating parts.
That’s true for ANY heat engine: gasoline, Diesel, two-stroke, four-stroke, gas turbines, they all have lousy efficiency because more than half of the energy in the fuel goes out the tailpipe or into the air as heat! That’s where technologies like electric motors and fuel cells really shine, the thermodynamic efficiency is much higher. A typical electric motor is over 90% efficient at converting electrical energy into useful work. Electric cars have other advantages, such as maximum torque available at zero rpm, if we can ever find a way to store the energy they use more efficiently.
The new all-electric MG Cyberster has comparable range (350 miles) to my Miata, but weighs twice as much as the Miata 4376 pounds versus 2341 pounds), just because of the weight of the batteries required to get that 350 mile range. It also costs almost twice as much as my Miata. The MG starts at $70k, the Miata costs between $30k and $40k. At least part of the efficiency gains of the electric motor are offset by the tremendous weight of the batteries that they must constantly haul around! See the Autoweek article about the MG in the link below:
https://www.autoweek.com/news/green-cars/a44532320/mg-cyberster-electric-roadster-goodwood-reveal/?source=nl&utm_source=nl_aut&utm_medium=email&date=071323&utm_campaign=nl32073378&user_email=87d5cb0eae37e01ac8b283ab5e58a771767744912367e7636433e9cb91597df5&GID=87d5cb0eae37e01ac8b283ab5e58a771767744912367e7636433e9cb91597df5&utm_term=TEST-%20NEW%20TEST%20-%20Sending%20List%20-%20AM%20180D%20Clicks%2C%20NON%20AM%2090D%20Opens%2C%20Both%20Subbed%20Last%2030D