How Wilwood turns aluminum chunks into brake calipers
When it comes to upgrading your vehicle’s brakes, only a few names in the aftermarket-parts business come to mind. Wilwood is probably one of them. What goes into making the components of an aftermarket brake system? We wanted to find out, so we took a trip to Wilwood’s complex in Camarillo, California, which houses R&D, sales, marketing, manufacturing, and QC in a few very large buildings. In total, the location employs almost 400 workers. Two shifts keep Wilwood operating 16 hours a day, six days per week. We stopped by to see how the company builds brake systems, starting virtually from scratch.
To begin our tour, we met Mike Hamrick, events and promotions manager at Wilwood Disc Brakes. He told us that while Wilwood is known for its brake systems for performance cars and off-road trucks, almost half of its total business is in OEM (original equipment manufacturer) products, including heavy armored vehicles produced under military contracts. Wilwood’s research for one feeds the other.
Hamrick explained that while it’s not too difficult to improve the braking performance of a classic car or truck, increasing the track performance of a modern Mustang or Corvette is another matter. The factory brakes are often very well sorted and perform admirably. However, once a buyer adds a set of wider, stickier rubber to their car and pushes it on the track lap after lap, the factory rotors and calipers will eventually show their limitations.
Wilwood’s goal isn’t to just add braking power but to improve upon repeatability. “We’re trying to make [the vehicle] stop 10 feet shorter, 20 times,” Hamrick explained. Sometimes, especially with heavier vehicles, the way to get prolonged brake performance is to add mass to the rotors. That’s often the case with trucks to which a customer has added taller, heavier tires. Other times, braking can be improved while reducing weight. Reducing rotating mass and adding long-lasting braking is a huge win-win for track performance.
We asked Hamrick how Wilwood develops a brake kit for a specific car. It all starts in the R&D department. That is where vehicles get measured and engineers design the brackets and determine which calipers would be the best fit, or if a new caliper design is warranted.
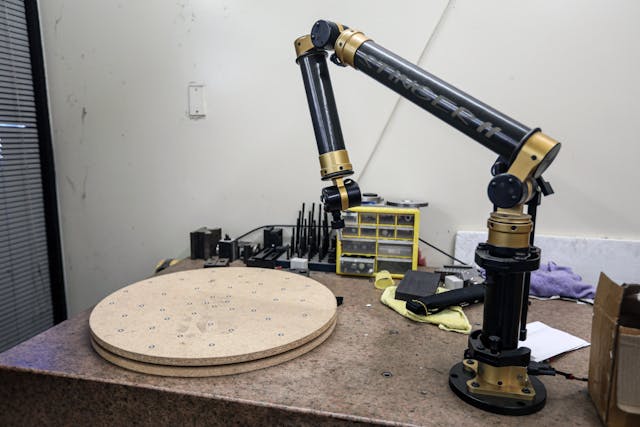
This Stinger II measuring arm can pinpoint critical mounting locations to create a digital model. Engineers at Wilwood develop not only the brake components but also the fixtures for CNC machining. That helps streamline production, as fixtures can be designed for tooling to reach all areas that need to be machined, in as few operations as possible.
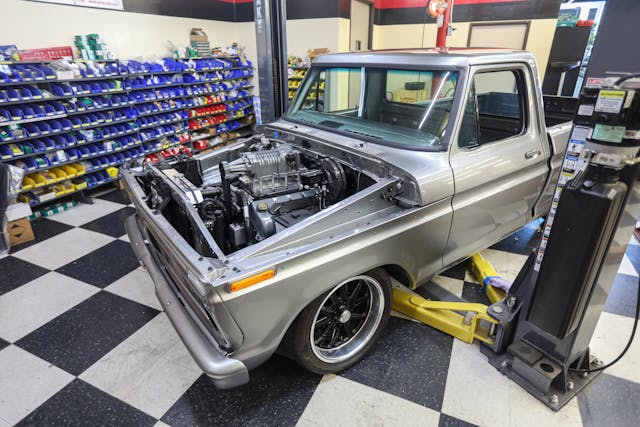
Company founder Bill Wood’s ’75 Ford and a Chevy C10 shop truck were in R&D when we stopped by. Wilwood bought the Chevy simply to get into that particular pickup truck market.
The R&D department includes all the equipment needed to machine a mounting bracket or caliper, including founder Bill Wood’s original Bridgeport mill that he used to make his first calipers back in the 1970s.
Not far from R&D, Wilwood operates two devices that put its parts to the test. This Chevy small-block-powered dyno runs on natural gas and puts all of its power into a heavy steel flywheel. A rotor and caliper mounted to the flywheel can be used to bed brakes for race teams looking to save time at the track.
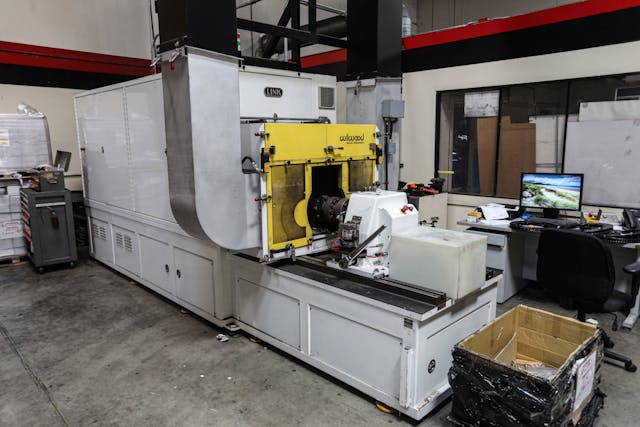
Right next to that is another dyno. This one can simulate vehicle weight up to 30,000 pounds and even simulate laps at tracks to see how friction would change over the course of a race. Removing variables helps make A/B comparisons of pads and rotors much more useful.
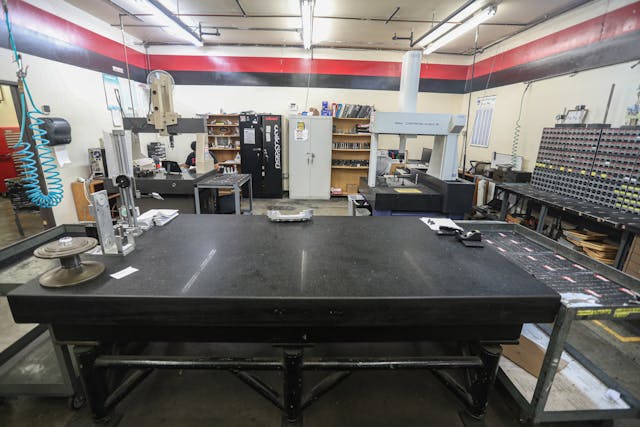
Before a shipment of raw materials can start the process of becoming calipers, it gets inspected and vetted. That material, of course, includes caliper forgings, but even bar stock gets scrutinized on precision-ground tables, shown above, that serve as flat references.
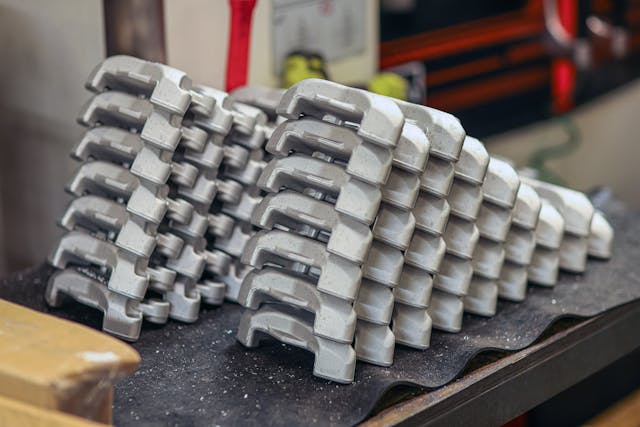
About 90 percent of Wilwood’s calipers are made from 6061 aluminum forgings; the remainder are pretty evenly split between aluminum castings and billet aluminum. The forgings are sourced from across the United States as well as abroad.
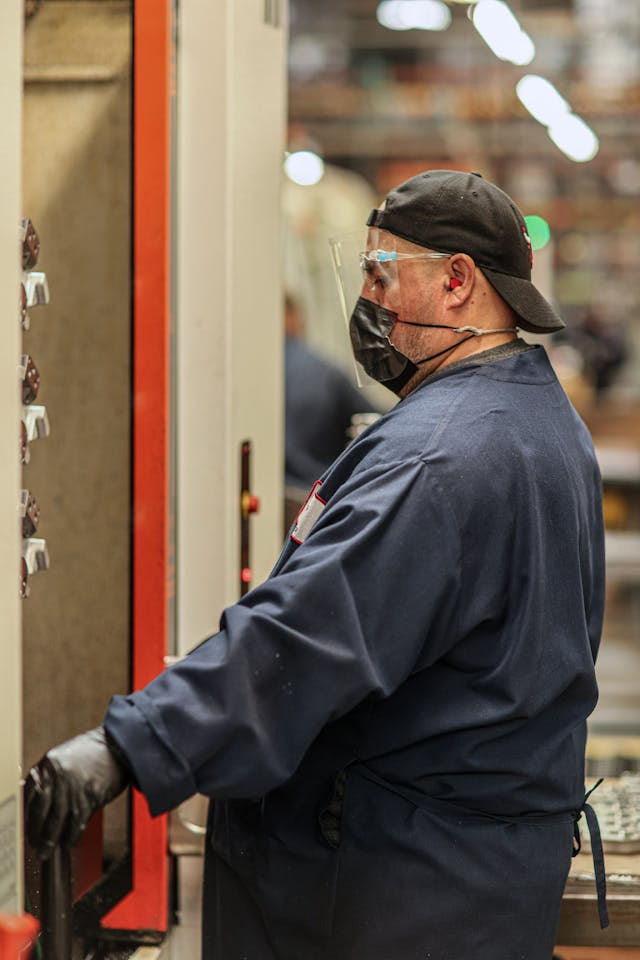
A set of 14 CNC machines churn out the two halves that make up a caliper. Each machine uses a pair of four-sided “tombstone” fixtures that secure the raw forgings. Wilwood doesn’t want to share exactly how it makes its fixtures, but each one for this operation is about 12 inches square and 18 inches tall, and each holds several forgings on each of its vertical planes, held in place by pneumatic clamps. The machine mills each part on one tombstone while the operator loads the other.
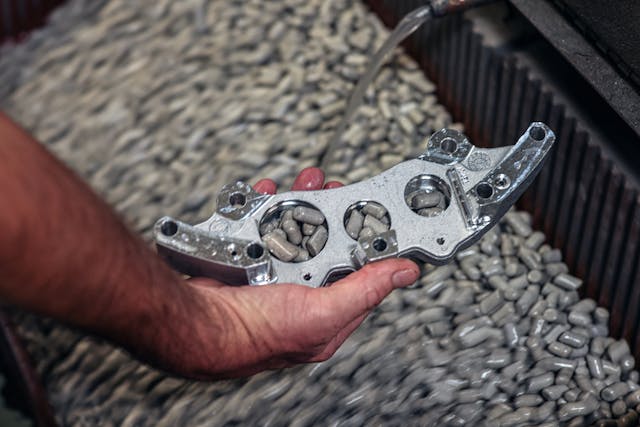
Once the parts come off the CNC machine, they go into an abrasive tumbler for a few minutes to take off the sharp edges. In an eight-hour shift, each CNC operator will complete about 250 inboard and outboard caliper halves.
Three employees per shift tend the machines and keep them running cool and smooth. One task is to collect the aluminum chips from each machine and dump them into a hopper that turns the chips into compressed logs about three and a half inches in diameter. This step serves two purposes. First, it greatly reduces the volume of aluminum chips, helping make transport more efficient. It also squeezes out the coolant, which is recycled. When new shipments of raw aluminum are dropped off, those truckers pick up the scrap for recycling.
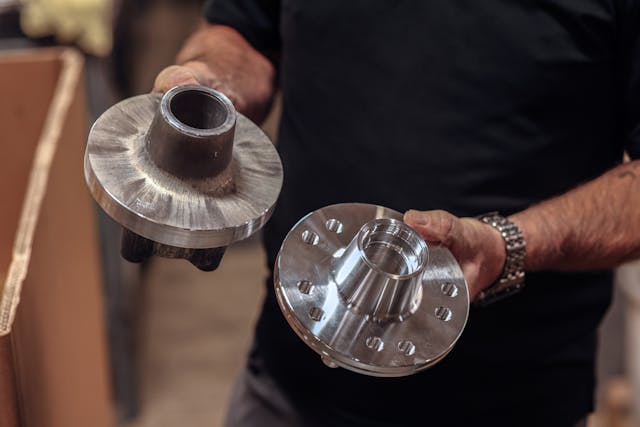
In addition to calipers, Wilwood also makes mounting brackets, rotor hats, and hubs. This single hub forging covers 130 different part numbers, depending on how it is machined. These complex parts used to require five separate machining operations. Now, two multi-tasking Mazak machines incorporate turning and milling to turn a hub forging into a finished part in just two operations. Each machine and operator can complete 250 hubs per shift.
To ensure top-notch quality, Wilwood moved all of its finishing and coating processes in-house. All Wilwood calipers get hard-anodized to give their surfaces a durable finish. This room is where it happens. Parts get washed to remove coolant from the machining process, then are dried off before going into an acid bath and getting charged with electricity to build a tough skin of aluminum oxide. The portion of the racks to which the parts get mounted are made of titanium.
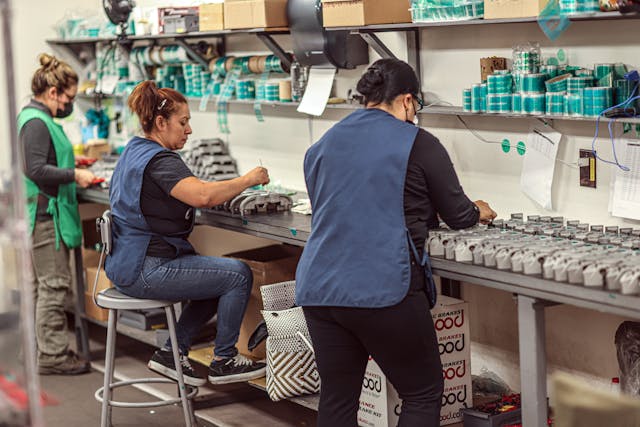
After anodizing, race calipers are ready for assembly, but lots of aftermarket calipers get powder-coated. These women are responsible for carefully applying high-temp masking to the areas that won’t need coating.
Masked calipers are placed on racks, electrically charged, and sprayed with powder before heading into an oven to cure.
Once powder-coated, Wilwood can laser-etch or, in the case of this caliper, apply a logo using a screen-printing process.
Batches of completed parts are stored on pallets until it is time to begin assembly. Once a set of calipers is ready for assembly, workers pull all the necessary parts from the pallets, like the pistons, seals, and hardware.
Four lines of benches are filled with workers who assemble and test each part prior to packaging. These electric parking brakes are cycled to ensure they operate properly when voltage is applied. Completed calipers are then boxed and placed in the warehouse.
Wilwood sources its rotors from a number of manufacturers, and these components go through the same quality control process as the caliper materials. The worker at this station is applying E-coat, an electrically charged paint that will protect the rotor from corrosion.
Once an order is placed, staff vets it to make sure all of the right components have been selected. Workers then assemble each order from the inventory in the warehouse onto a cart and box it for shipping. Wilwood dropships orders for companies like Jegs, Summit, and Turn 14, from which the brakes will make their way to customers’ race cars, hot rods, and pre-runners.
***
Check out the Hagerty Media homepage so you don’t miss a single story, or better yet, bookmark it. To get our best stories delivered right to your inbox, subscribe to our newsletters.
I wish that they would make a complete four wheel set for a Triumph TR-6. They already seem to have a front set.
Hello. Just a heads up, I’ve looked into upgrading the brakes on my all original 45k mile TR6. There is information out there on how to use better common calipers that can be found cheaply in a salvage yard.
The problem is, when these cars were raced back in the day by winning teams, they had problems with the brake pedal going soft to the point where the brakes would have to be pumped entering a turn, not an ideal situation for a car with upgraded brakes.
The problem was traced to flexing axles on the spindles. The axles would flex, causing the rotor to in turn wobble or move enough to push the brake pad back into the caliper so that when the brakes were applied going into the the turn, the initial stab on the brake pedal was wasted pushing the pad back against the rotor. A second push on the brake pedal was needed to then gave a firm clamping force on the rotor.
The fix was to upgrade the front spindle and axle unit to a stiffer one.
So, be aware that if you plan on upgrading your brake calipers plan on upgrading the spindles as well, otherwise you may spend your hard earned money and be disappointed, not because of a fault of the brakes.
Great info!
I wish that they would make a four wheel conversion for a Triumph TR-6.
Top Notch! Been running and loving a set of 6-piston Wilwood calipers, 14 x 1 1/4″” rotors and big bearing hubs on my ’65 Mustang Fastback street legal weekend road coarse warrior for years with no issues. Thanks for taking us behind the scenes of a true USA company!
*course
Great article, Brian! I’m amazed at the amount of parts that are available for our collector vehicles — places like this make older car ownership possible. Thanks for sharing — steve
I upgraded my 68 Firebird 350HO with Wilwood kits. The hubs particularly are machine Art! Great products and fairly easy to install. The tech help available is also top notch; I needed advice on the correct master cylinder for a non-boosted application. they were right on the system is well balanced and did not need a proportioning valve. I asked the rep what they did with machining seconds – the hubs would make great shop decorations! He agreed but for liability reasons said no way. Great articles thank you.
Great story about Wilwood. I’ve been running their parts on my track day car and have been very pleased with the quality/fitment/instructions, etc. I will also throw a “kudos” in for their EXCELLENT Customer Service. Each time I’ve been on the phone with them, they are both knowledgeable and friendly.
Very cool story. Wilwood brakes have been a part of various projects with friends over the years.
I’ve been running a four wheel Wilwood setup on my 99 BMW M3. They are absolutely fantastic brakes and were half of the cost of the OEM replacement calipers. As a bonus they look fantastic and are easy to swap pads on without taking off the caliper.
I threw a set of their smaller rotors on my ’07 Silverado 1500 that got driven like a race car, and towed cars on a flatbed for 100k miles plus. Had to use the smaller rotors so my 18″ winter wheels would still fit. Pads aren’t even noticeably worn yet!! AMAZING stuff they make. Been through a couple road salt baths up here in MA, too. A little rust on the steel / iron parts, but no worse than what we normally see. With the braided steel brake lines that came with the set, that pedal only has to move a fraction of an inch to get solid, mush-free braking. Best upgrade I ever did!
I used the 6 piston calipers with the drilled and slotted 13″ rotors on my MINI Cooper S and the difference was night and day !! The feedback you get from the pedal was incredible , the stopping power was superb and not that it matters but they did look very nice as well . I HIGHLY recommend Wilwood’s for a daily driver or a track machine. You will NOT be disappointed.
Upgraded my ‘66 Fairlane from 4 wheel drum/single chamber master cylinder to non-boosted front discs with dual chamber master cylinder. They had all the parts to implement & helped me with getting all the correct pieces. With help of a friend with brake line tools & experience, install turned out great! What a difference they made in vehicle stopping confidence! No more leaving 50 car lengths between me and car in front!