5 Drill Press Tips and Tricks
Adding tools to a home shop is a never ending affair. There are staples though and a drill press is one of them. It’s handy for a whole host of reasons other than just being more convenient to use for drilling compared to a hand drill, and if you follow these five tips you will find that you might use your drill press even more.
Not just for making holes

Jacobs chucks and the spindle bearings in a drill press are not designed for the kinds of side loads encountered when attempting to mill with a drill press. Even with the limitations, chucking a wire brush into your drill press can be very helpful in cleaning up small parts and hardware. This has gotten me by without owning a bench grinder with a wire wheel for years, though a wire wheel in a drill press is slower and less efficient.
Check your table for square
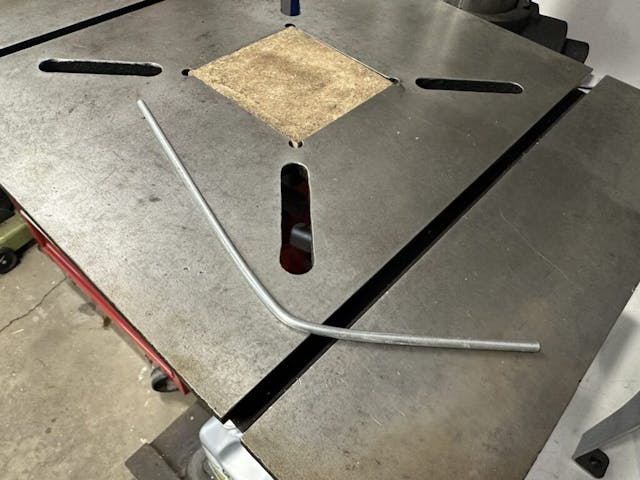
Drill presses are great in the way they eliminate the human error that creates wonky holes when drilling with cordless or corded drills. Well, it should. If you haven’t taken the time to adjust the table and ensure all the parts of your drill press are correct it’s likely not much of a step up from hand drilling.
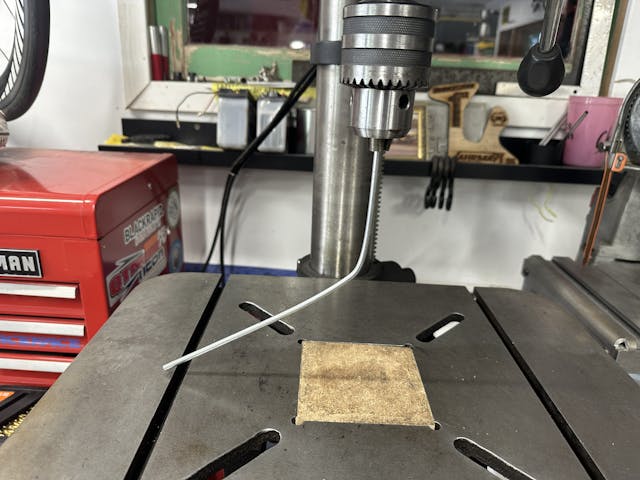
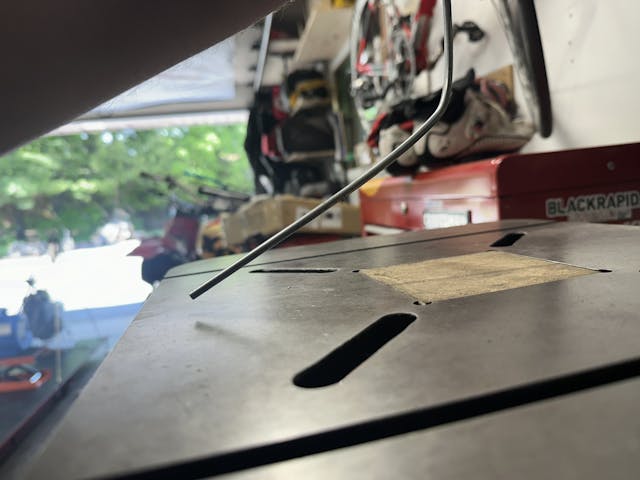
It’s easy to check that the chuck is square to the work table is with a short section of round stock. Bend the stock into a pointer and hold it in the chunk then rotate it by hand to check where it does and does not contact the table. Adjust until even. It might be tempting to use a bubble level or similar, but the key here is that the chuck and table are positioned properly to each other, which a bubble level cannot tell you.
Get used to changing speeds
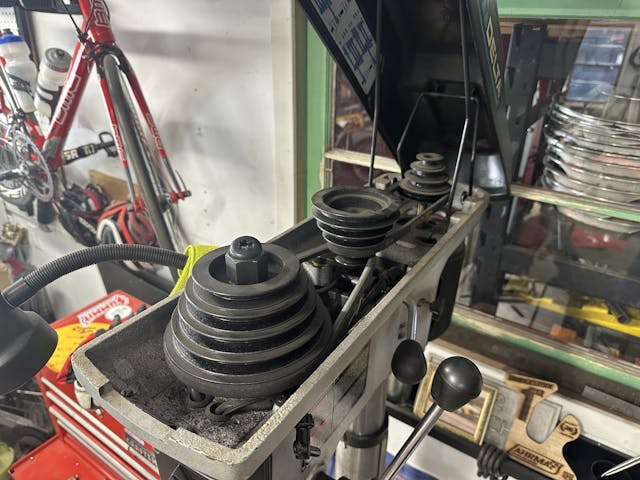
We know most people put the belts on the spindle to set the speed in the middle of it’s range and use that speed for everything from 1/8″ holes in aluminum to using large Forstner bits in wood. Does it work? Kind of, but proper speeds and feeds make for better and safer results. Maybe you shelled out big bucks for a variable speed machine, but most of us are getting by with a well-maintained vintage piece that has a belt and pulley system for changing the spindle speed.
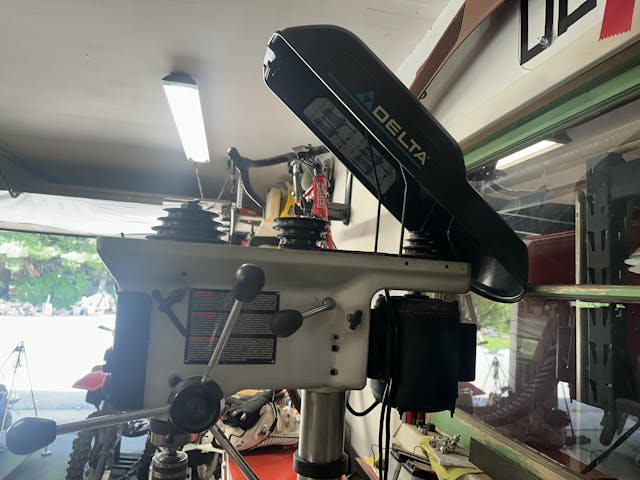
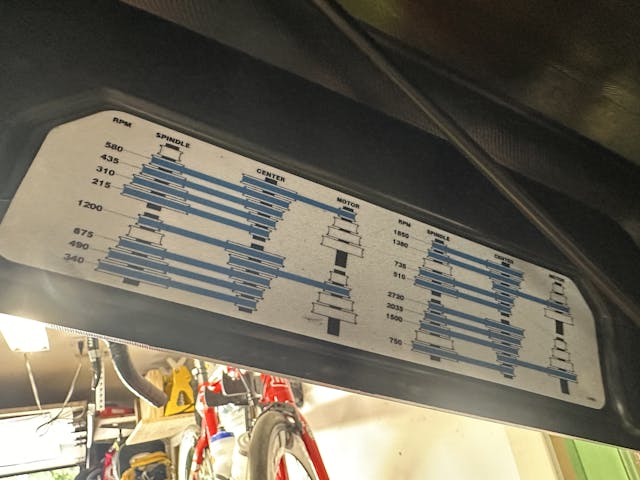
It can be slightly cumbersome to swap out the belts and shuffle everything just to drill one or two holes and switch the belts again. That’s why it’s best to practice a few times on how to do the switch and make sure you keep the space avaliable to make the swap easier.
Get a decent vise and use it
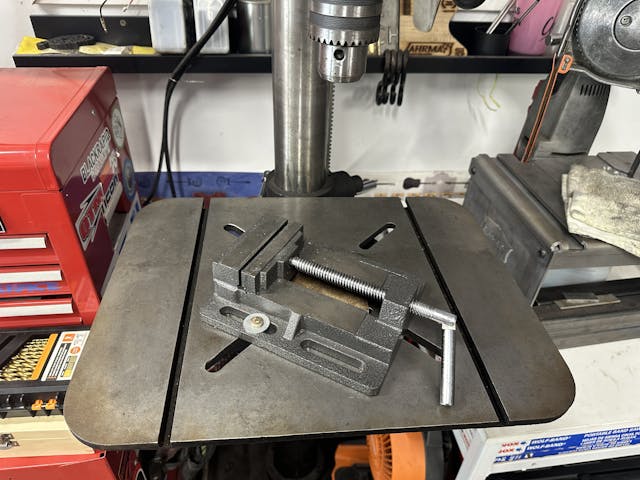
As tempting as it is to leverage the “constantly set up” nature of a drill press by just putting a bit in the chuck and making a hole in your project, that comes with a surprising amount of risk. Bits can and will grab workpieces which can whip them out of hand and cause damage to the drill press, the stuff around it, and you. A simple vise will make drilling precision holes easier and safer. Even cheap import vises like this one are better than nothing if you are still searching for the right vintage one.
Consider upgrading chucks
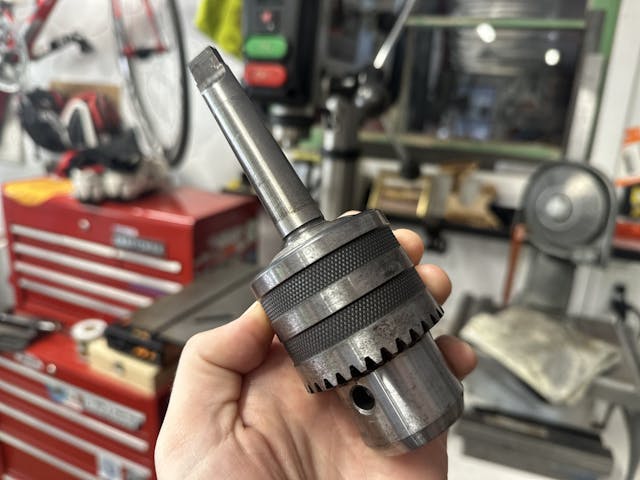
The Jacobs chuck is all but ubiquitous for drilling, especially on vintage equipement. The design makes grabbing tooling quite easy but the need for a special key can be annoying while also opening up safety risk when users leave the key inserted in the chuck. Accidentally power up the machine with that key hanging on the chuck and it’s going to be a bad day.

Think about upgrading to a keyless chuck. Most drill presses use a Morse taper to hold the chuck in place, meaning swapping the chuck out for a keyless one that is easily tightened and loosened by hand take no more effort than knocking the keyed one out and matching the machine’s taper to a new chuck. No key to lose or forget, plus ease of use.
***
Check out the Hagerty Media homepage so you don’t miss a single story, or better yet, bookmark it. To get our best stories delivered right to your inbox, subscribe to our newsletters.
I have an old dinosaur drill press that is probably older than all my cars. One thing I do with it is leave the belt on the loose side. if the bit fetches, the belt slips and I don’t break a drill bit or an arm
Tip #2 for checking table is great and easy to do.
Thanks Kyle
Son of a, that bit is hot! How many times ? When will I ever learn?
Enjoyed the comments
I have passed up getting a drill press due to space limitations. I use them at work and see the wisdom of the tips in this post.
I bought a Porter-Cable table-top model because of space reasons. Much better than nothing.
Indispensable !
Thanks for the photo of your vise. I’ve been trying to secure mine all wrong.
Good stuff, Kyle! Especially for squaring the table.
Retired Toolmaker here….
The bent rod to ”square the table” is a good start… we put dial indicators on the rod…..
Jacobs keyed chucks were the gold standard for decades…. the keyless ones are about like the one on your battery drill… Once you spin a larger drill, the jaws are galled… same is true of a keyed chuck, but the key really tightens it. A hobbyist’s chuck should last a lifetime.
Rather than bolt the vise to the table, which makes lining the center punch mark near impossible… find a way to block it in to keep it from turning. You’ll develop an eye for doing this.
Use the correct rpm…. or as close as possible. and a small amount of cutting oil or Tap Magic.
When I was a wee lad, machinists had a saying: “Machining is 5% cutting and 95% work holding.” Wise words for anyone using a drill press, lathe, milling machine or saw. For a drill press at the very least you’ll need some c-clamps and wood blocks, in addition to a good vise or two (I have a cheap one, plus a good square corner Palmgren one). Another good addition is a cheap hold-down kit with some step blocks, studs and clamping dogs for holding irregular shapes (that comes in handy for a welding table, too). Also, don’t forget the obvious: Good drill bits, in Fractional / Letter / Number sizes, plus Metric. If you work with sheet metal a lot invest in some good-quality step drills as well.
One last thing: I have found that taking a chunk of aluminum plate and tapping a bunch of holes in it for holding down small parts comes in handy. Consider it a consumable; just drill right through it. I have had to make special washers before and making a small “finger plate” like this makes it a whole lot easier and safer to hold them and drill them out to size. I have several fixtures like this laying around. Like I said…..95% work holding……
I’ve had my drill press for years and finally bought a vise for it this year. Also picked up a one arm type vise grip from china freight. Has an eye bolt that goes through the table and clamps work piece. About $10 American
(ps) Shopsmith….miss the Shopsmith
I always put the chuck key in the jaws of the chuck and hand tighten it so I don’t lose it
I have a large flat magnet cable tied to the column just below the head to hold the key, bits I’m using, ect. Works great.