This track-ready C10 has Group 5 racing flavor and a Corvette soul
A lot of our favorite production vehicles have come to fruition after asking a simple “What if?”
“What if we drop a 389 V-8 into a midsize Pontiac Tempest?” led to the GTO. “What if we put an American pushrod V-8 into a gorgeous, low-slung Italian body?” led to the De Tomaso Pantera, the Bizzarrini 5300 GT, the Iso Grifo … You get the idea. Cameron Bishop, owner of Cutting Edge Hot Rods in Phoenix, Arizona, used a similar thought experiment to drive the creation of one of our favorite custom pickups in recent memory: “What if Chevrolet built a truck for Group 5 sports car racing?”

Bishop has a background in off-road vehicle fabrication and parlayed that experience into starting his own custom shop, which has built several customer cars. He was wrapping up a customer’s Holman-Moody-built Mustang a few years ago and was surrounded by vintage ’70s racing equipment when inspiration struck: Bishop wondered what it would have looked like if Group 5 had a truck class.

“I’ve always loved ’70s-era race cars. The Group 5 class in particular,” Bishop said. Group 5 evolved quite a bit from its inception in the ’60s until its demise in the 1980s, but for a good portion of its time, the class represented production-based road racing at its most exaggerated, with insane levels of power and wild flares covering massive tires. The Zakspeed Ford Capri and the slant-nose Porsche 935K stood out to Bishop in particular. His son, Carson, had just turned 3 and was beginning to play with toy cars, so Bishop decided it was time to build a rolling business card for his fabrication shop—something he could get his son involved in while hopefully sparking an appreciation for restoration, fabrication, and competition.
“Once I had the style, I had it built in my head,” Bishop said. “I worked with an artist in Canada (Chris at Rendered Rides), who helped shape the proportion and how it was all going to work.” He was able to find a 1972 Chevrolet C10 posted for sale and soon the project was underway, with little Carson helping on the teardown.
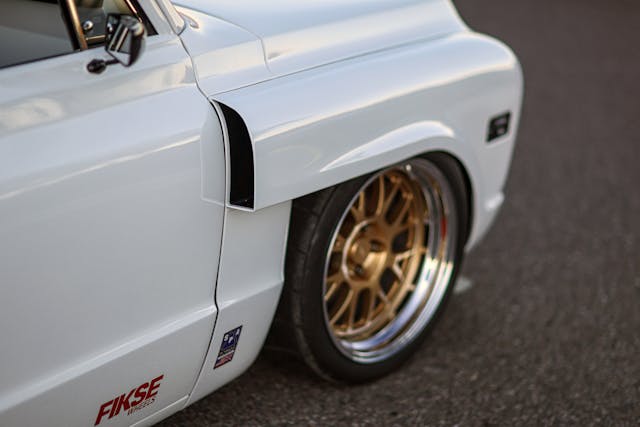
One of Bishop’s previous builds had been based on C5 Corvette suspension, and he appreciated that layout’s performance potential combined with low maintenance and easy-to-find parts. After asking around, Bishop learned that one of his friends had a wrecked 2012 Corvette Grand Sport with just 40,000 miles on the odometer. The previous owner had lost control of the C6 Corvette on the highway and the car suffered severe body damage, but the chassis and drivetrain were fine. It would be the perfect donor for his ambitious project.
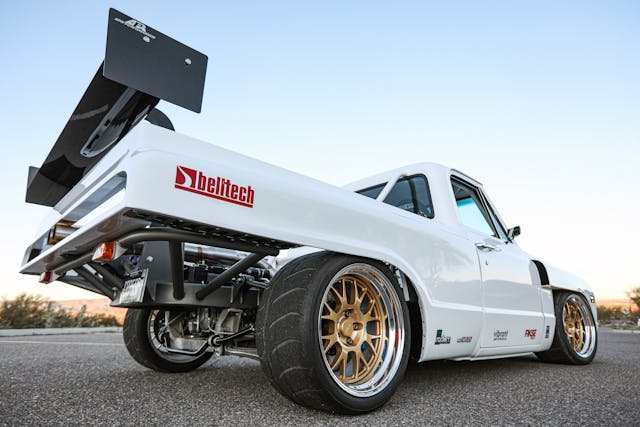
With C6 suspension in mind, Bishop designed a new chassis using 3D modeling and tweaked the geometry to work with the truck’s longer wheelbase. The chassis is made from a pair of mandrel-bent 2×4-inch steel frame rails. Once set up on his chassis table, Bishop built the crossmembers in 4130 chromoly steel and bolted the Corvette suspension into place.
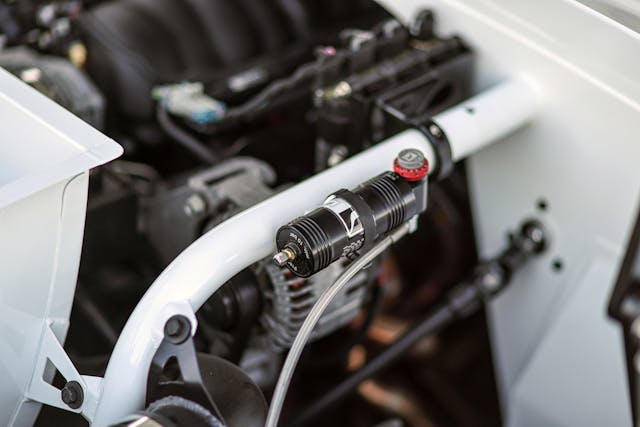
C5, C6, and C7 Corvettes use transverse leaf springs, but that makes tuning the suspension difficult. Instead, Bishop chose triple adjustable coilovers with a hydraulic nose-lift function for clearing speed bumps and other awkward obstacles that the low suspension would otherwise encounter. The system is from KW Suspension and engineered for Belltech, and this truck is one of the first applications.
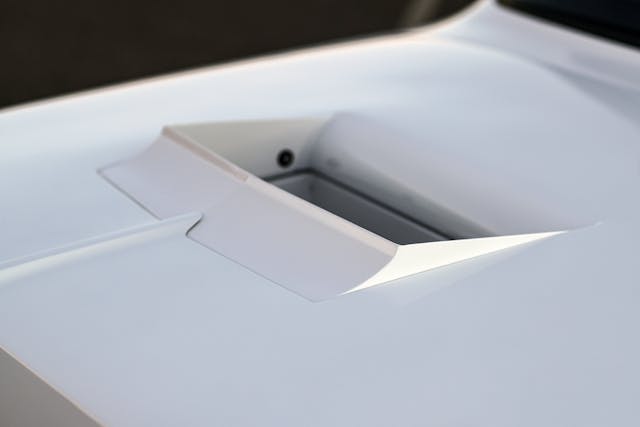
Starting with a Grand Sport as a donor meant that the LS3 was already equipped with a dry-sump oiling system, which keeps the engine supplied with plenty of oil pressure even during long, high-speed turns that might push oil away from a traditional wet-sump pickup. The LS3 runs on Holley Terminator EFI and uses a Holley 12.3-inch pro dash. Bishop tuned the V-8 himself. “I’ve always tinkered with them, but I’m not a tuner per se. If you have a basic understanding of what an engine should do, you can figure it out.”
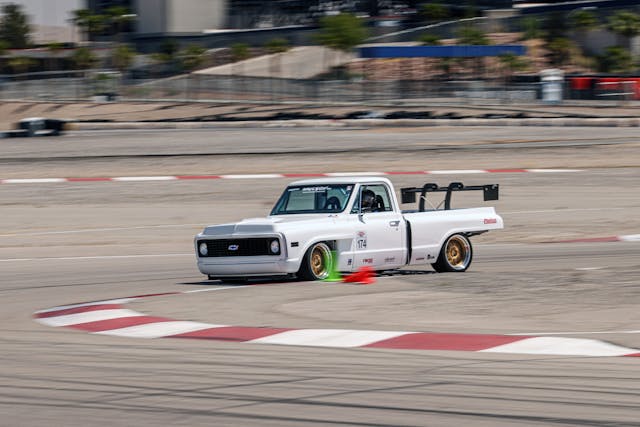
Despite their strong performance as built from the factory, LS engines are known for having almost criminally conservative camshafts. A rather mild bumpstick was chosen to wake up the 6.2-liter V-8 a bit, along with a custom set of long-tube headers with equal-length primaries using Vibrant tubing. Thanks to its improved breathing, the LS3 now produces about 525 hp. The engine is a bit of a placeholder as Bishop puts some track miles on the truck and gets the chassis sorted out. An LS7 build is planned for high-rpm naturally aspirated track fun, but for now, the LS3 is doing just fine. “Sometimes I want more torque in some spots, but everyone does,” Bishop joked as he praised the LS V-8. “You can bounce them off the rev limiter all day long and they don’t care.”
“I used styling cues from a lot of companies that raced in that era. I wanted ’70s flavor, but to still have something that handles.” — Cameron Bishop
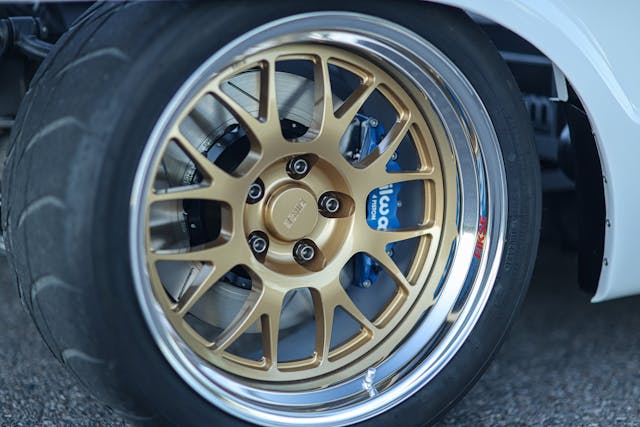
The pickup uses C6 Corvette control arms and knuckles with Wilwood brakes. Bishop used the biggest 6-piston brakes he could fit up front and used an equally large 14-inch rotor in the rear, this time paired with a four-piston caliper. He selected a set of 19×12-inch Fikse wheels due to their lightweight, strong construction, which should hold up well under the strain of racing. All four tires are 325/30R19 so they can be rotated to any position to get the most track mileage possible.
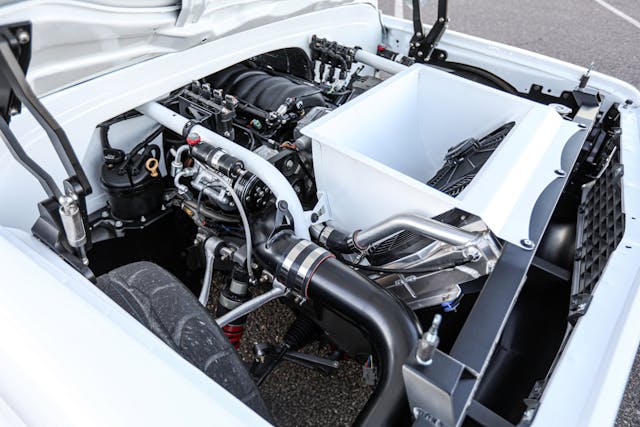
Fitting all of the Corvette parts into the C10’s proportions wouldn’t be easy, but the plan was to run off-the-shelf parts as the truck was meant to be a track performer and would be driven hard. Exotic pieces could leave it sidelined for weeks because of one broken component. The most difficult part about packaging the Corvette drivetrain into the truck was the torque tube. For the C5, C6, and C7 generations, Corvette used a rear-mounted transmission connected to the engine with a torque tube. In a Corvette, with the driver’s seat just in front of the rear tire and a 105.6-inch wheelbase, the torque tube is much shorter than it would have been on a C10 with its 112-inch wheelbase. The engine would have to come back, and not just a little bit. Bishop determined that to keep the proportions right, even after cheating the dimensions a bit here and there, the engine would need to move back 14 inches.
Moving the engine back that far meant cutting out the C10’s firewall and quite a bit of the floor. The location placed the back of the cylinder head well into the dash. To get the proper driving position, Bishop moved the steering column outboard and down and did the same with the seating position. Bishop, who is more than six feet tall, has no problem fitting in the cab, even with the engine intruding a bit. He described the challenges of packaging the truck around the Corvette components: “They were difficult to deal with, but they were largely beneficial. It just meant a lot of fabrication.”
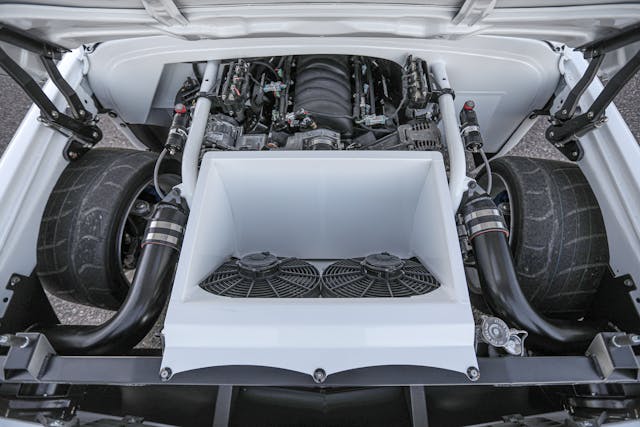
“With the engine so far back, I didn’t want to pack all that hot air into the firewall,” Bishop said. Thankfully he had plenty of real estate to work with and the radiator, which is laid back 30 degrees, has a direct path to push air out of the engine bay. He tested the position of the reverse scoop in the hood, which he formed out of aluminum, by running strings across the gap with streamers tied on perpendicularly. When driving, air clearly flows straight up and out of the engine bay.
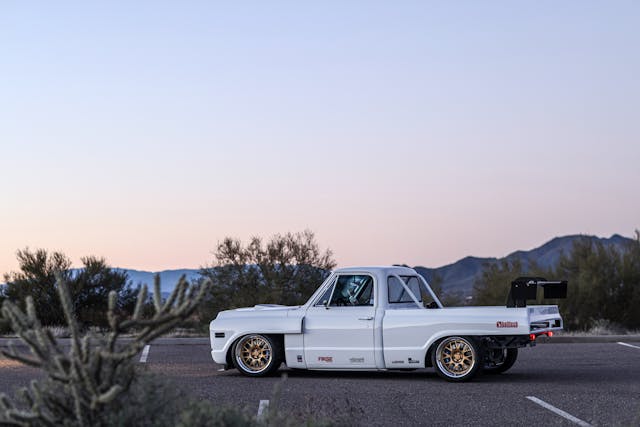
There were a lot of small modifications made to the profile of the truck that are hard to notice when your attention is drawn to the flares, the bedsides, and the wing. Bishop slid the cab and fenders back an inch, pushing the front wheels forward in the fender opening and closing the gap between the bed. The rear wheel opening was moved forward a bit, and three inches were cut off the end of the bed.

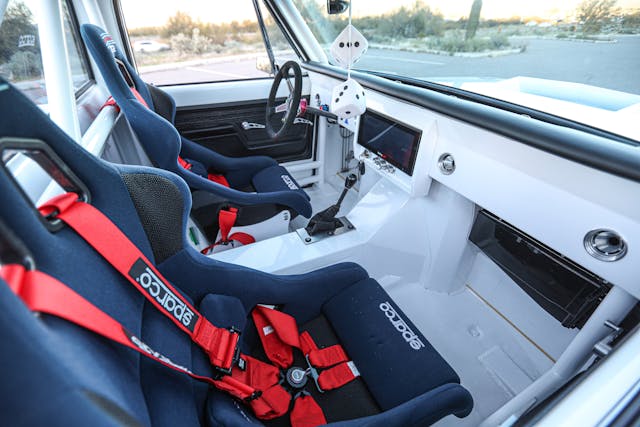
The finished truck weighs 3600 pounds when fully topped off with fuel, which is a bit heavier than Bishop had hoped. However, it’s not much heavier than a 2012 Corvette Grand Sport, which has the benefit of a composite body and doesn’t have a roll cage, so we’d say he did just fine in keeping the mass down. The position of the engine also resulted in all that mass being balanced quite nicely, with 53 percent carried on the front tires and 47 on the rear.

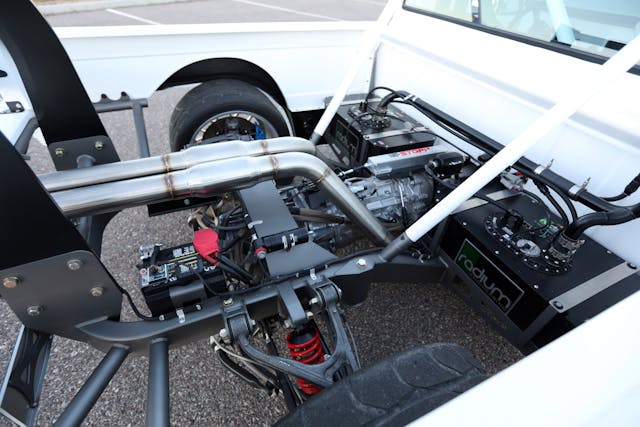
The Grand Sport donor also meant the C10 got a great transmission for the track, a rear-mounted TR-6060. That should hold up to any kind of abuse the future LS7 build can dish out, although a stronger differential might be in the pipeline to handle the extra power.
Bishop noted that he grew up watching TV shows that highlighted fabrication and transforming vehicles, shows like Monster Garage. Without as many examples to show his son, Bishop decided that this C10 transformation could fill that void and perhaps open the boy’s eyes to what’s possible with the right skills and proper planning. “If he doesn’t want to do that, it’s fine, but I wanted him to experience it.” It seems that the venture has paid off, as the truck is getting a lot of attention, and events like LS Fest West have proven to be a hit with his family, with Carson taking every opportunity to ride along in the track-tuned truck. Holley awarded the C10 its top classic truck of the meet at the event, and Carson took the award to school to show it off. “It’s his now if you ask him,” Bishop added, speaking not about the award, but about the whole truck. Considering he’s got another 10 years or so before Carson can take the wheel, maybe the LS7 upgrade can wait a while.
***
Check out the Hagerty Media homepage so you don’t miss a single story, or better yet, bookmark it. To get our best stories delivered right to your inbox, subscribe to our newsletters.
Just brilliant both in design and execution.
This is what happens when you answer a question no sane person ever asked. A beautiful C10 design gets cut up and made into something you wish you had never seen.
I’m with you on the overall appearance of this but the fabrication work is gorgeous.
Fantastic build and well written Brandan. Although I miss the C10 taillights, I can appreciate the nod to the 917 in that department…lots of subtle changes to absorb in this build!
Whatever floats your boat. I would prefer to be able to haul a load of mulch.
Race to the sale of the day on mulch!
A lot of time and (high quality) effort trying to turn a truck into a car. You end up with neither. Great workmanship, but I just don’t get it. Whatever…
About as aerodynamic as a corrugated tin cow shed.
If power to weight is low enough, it will overcome areo. Thus the fun of whipping up on aerodynamic super cars in a box.
There is one of these that makes the cruse night circuit in Western Connecticut, I think it is out of Danbury and it is a C4 with a black primer body. The one in Connecticut is not as clean as this one, but every bit as interesting.
I’m by no means a truck guy and I like it. Intellegently designed if a bit low for real-world streets. The (air?) adjustable suspension apparently helps.
It’s a crazy build. Love those wheels!
Ok, so some hate and some want to haul manure instead who gives a rats ass! The whole point is it’s provocative and it gets people going. Bravo to the builder, if it wasn’t for people like him pushing the envelope we wouldn’t have some of the hot rod designs we have today.
I just cracked myself up with this one… The subject lines on my emails tend to be a bit cryptic sometimes and I admit that I don’t always read them all that carefully. So when I read the headline for this one, I immediately thought, “Geez, the C8 has only been out for what – a year and a half now? I haven’t heard ANYTHING at all about a C9, and Chevy’s already got a C10 prototype on a track somewhere?” Ha-ha…
No build is a thing of beauty to all beholders, so it’s not fair to criticize the thought, effort and time that went into someone’s project just because you have some other standard by which you measure.
I would never take an Impala and make into a low-rider but I have no problem talking to the owners about how they solved this problem or that problem and congratulating them on a job well done.
Personally, I think this truck was well laid out and well executed. It’s mission is not to haul mulch, it’s mission is to attract gawkers and to fly around the track and both of those it can do quite well.
Kudos to Bishop and may his son grow up to love building things as well!
If you are a hater, you are not a builder. Excellent quality and wormanship. Good job mr. bishop.
workmanship
This is not my kind of truck, but I applaud the builder for his planning and attention to detail. This is not a C10 with patina and a 350 dropped in. It took knowledge, ability, and cash, which most of us don’t have, to carry out this build. My one suggestion would be to chop the top a couple of inches.
Just WOW !!
What else can you say !