Homegrown: HyperRocket autocycle is retired Ford engineer’s “crotchless” creation
Welcome to Homegrown—a new limited series about homebuilt cars and the ingenuity, diligence, and craftsmanship of their visionary creators. Know of a killer Homegrown car that fits the bill? Send us an email at tips@hagerty.com with the subject line HOMEGROWN: in all caps. Enjoy, fellow tinkerers! -Eric Weiner
Every now and again, from across the lake where I reside, the captivating sound of a Rotax aircraft engine powering a small seaplane reaches my ears. This is my cue to cease what I’m doing to witness the tidy water-and-air craft slip Earth’s surly bonds. This week I met the man behind the machine, 62-year-old retired Ford engineer John Hickey, who combined Kitfox aircraft components with floats thirty years ago.
Imagine my delight when this new neighbor friend also presented six of the eight three-wheeled HyperRocket “autocycles” he’s built at home in his pristine southeast Michigan shop.
Hickey spent 30 years at Ford specializing in fuel economy development—a worthy cause in the current moment of $5 gasoline and the industry’s transition toward electric propulsion. It was the unlikely combination of his professional expertise and his experience building the seaplane that led to his creation of the HyperRocket. Combining lightweight aircraft aerodynamics with the performance of a sport motorcycle produces what Hickey calls a “crotchless rocket,” named so because no frame or fuel tank resides between the driver’s knees.

For each HyperRocket he produces, Hickey spends approximately six months on design and analysis, followed by six months of fabrication. The gas-powered versions boast a wide front track, handlebars and controls from a Suzuki motorcycle, a single rear drive wheel, and room for the driver and one passenger. Hickey sought to optimize performance while minimizing fuel consumption, focusing on ample stability, accurate control, and light weight.
How light? One version creatively combines a Suzuki Hayabusa 1340-cc inline-four motorcycle engine with turbocharging and intercooling to achieve a phenomenal 500 horsepower in a 585-pound, ready-to-rumble package. That machine has topped 200 mph on Hickey’s secret test track.
“While my job at Ford maximizing fuel efficiency provided much of the expertise required for this project, there were significant engineering gaps that had to be filled,” Hickey explains. “The most notable was every aspect of vehicle dynamics—how the suspension design interacts with the physics of motion to determine stability. A software called Wishbone was instrumental in laying out the front suspension.
“Aerodynamics is the second performance concern. Here, JavaFoil software helped optimize drag, lift, and directional stability. A third software obtained from Performance Trends predicted engine output considering bore, stroke, and boost pressure parameters.”
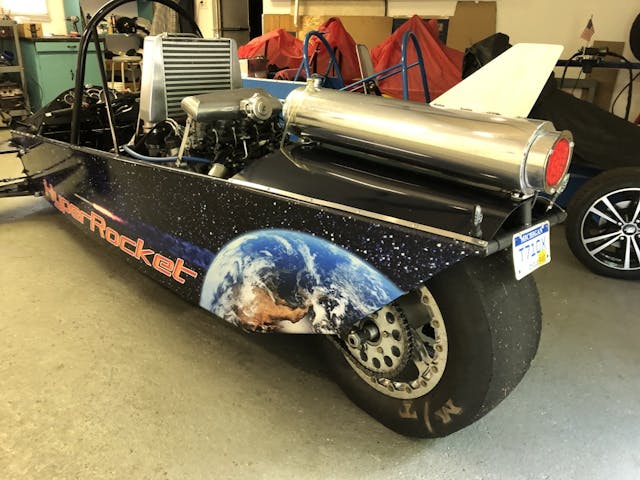
The complete suite of Computer Aided Design (CAD) and physics-based analysis software helps optimize all aspects of the design including performance, fuel efficiency/range, stiffness/stress, aerodynamics, suspension dynamics, and braking ability.
“Using software to model and predict performance is standard OE car-manufacturing methodology,” says Hickey. “You start early—long before production commences—to assure that essential safety and performance goals are achieved in your final design.
The high-strength-steel chassis tubing is cut on a purpose built CNC machine to exacting tolerances. Borrowing a page from historic aircraft manufacturing procedures, Hickey covers his structures with ultralight polyester fabric drawn taut with heat. Paint and/or a wrap gives each HyperRocket constructed thus far a unique appearance. The nosepiece is made of thin fiberglass molded locally by a shop using a form created by Hickey. Two options are available to minimize the ill effects of cockpit buffeting: wear a helmet or add the optional windshield shown here. One such HyperRocket entered in the Vetters Fuel Economy Challenge achieved 140 mpg.
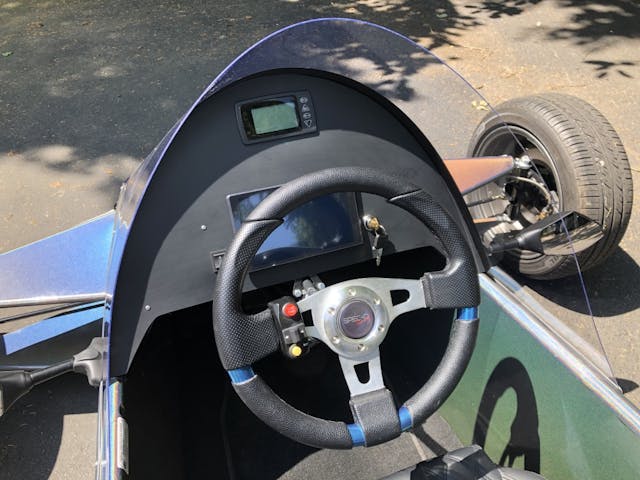

“My goals were light weight, low aerodynamic drag, and minimal frontal area,” explains Hickey. “What I ultimately achieved in the HyperRocket an 0.27 drag coefficient, and a frontal area below one square meter. For reference, the drag coefficient for un-faired motorcycle and rider typically tops 0.75.
“Achieving suitable stability became a development effort. My first two HyperRockets demonstrated less than perfect stability in crosswinds, gusts, and while passing other vehicles on the road. Anything this light can become a kite in certain circumstances, so I fine-tuned steering, suspension, and external shape details to remedy those issues.”
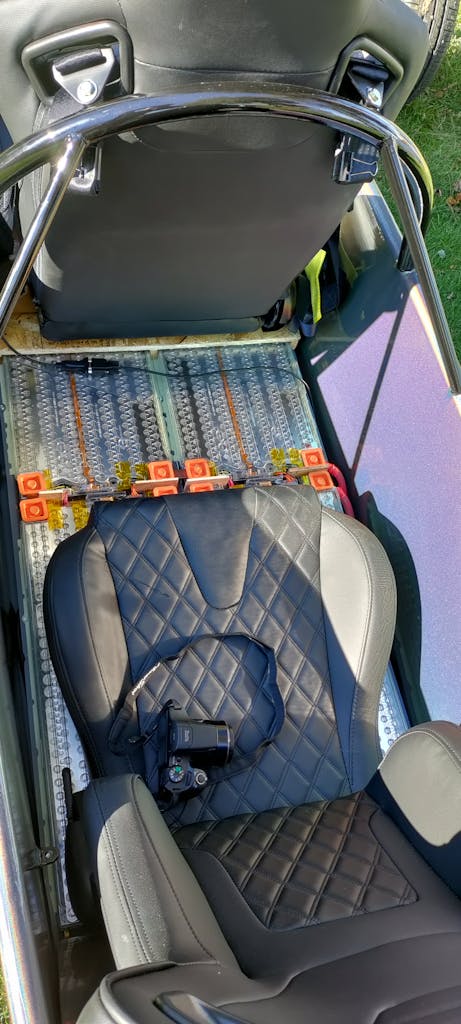
Hickey’s crowning achievement is the pearlescent-painted, fully electric tandem-seat HyperRocket featured here. Combining Tesla Model S battery cells with a Netgain HyPer9 AC motor and direct drive yields a machine that’s simultaneously zero-emission, quiet, and the arch enemy of inertia.
I know that’s true because Hickey (foolishly) allowed me to terrorize a nearby neighborhood in his stealthy electric HyperRocket. While the chain-drive noise produces a soundtrack that is louder than he’d like, the most noise I heard came from the Toyo Proxes R888 205/45ZR-17 rear tire scratching the asphalt beneath its tread. I found the three-wheeler to be an ideally quiet means of scooting to 60 mph in less than five seconds, and adjustable brake regeneration makes this a true single-pedal machine for most situations. There’s some feedback from the road through the rack-and-pinion steering that guides the Federal 14/7 low rolling resistance front tires.
The streamlined shape and 780-pound curb weight for the HyperRocket EV yields 260 miles of around-town range and 150 miles of highway range. The front seat slides fore-and-aft to accommodate various body builds, and a sleek windscreen serves nicely as a wind deflector Bringing a companion requires removal of the clear plastic cover over the second seat. Alternatively, that rear space can accommodate up to 500 pounds of cargo.
Hickey adds, “The relatively easy part of this project was achieving good correlation between simulated and real-world results. Once my engineering models were perfected, I used them to predict the performance of rockets, Teslas, and electric motorcycles … with excellent correlation.”
The mainstream auto industry’s move to BEVs should advance the home-built cause, because electric motors are easier to integrate than combustion engines with their fuel, intake, and exhaust systems. At last year’s SEMA show, Ford introduced its Eluminator crate motor, essentially the same 281-horsepower AC motor and gear reducer that drives the Mustang Mach-E. That $3900 propulsion package weighs but 205 pounds. As you might imagine, neither batteries nor electronics controls are included.
Exposure to his HyperRockets convinced me Hickey’s ambitions are practically unlimited. At present, he is examining means of integrating the electric motor within the rear wheel’s hub to provide additional seating space while also eliminating drive chain noise. A more long-view goal is to explore the feasibility of selling his homebuilt three-wheelers in higher volume, which would require a deep-pocketed backer in the Elon Musk or Henrik Fisker vein. We wish him nothing but good luck and great success.
Any reader (or investor) anxious to learn more about Hickey’s gas and electric-powered creations can reach this modern-day Orville Wright at: HyperRocket1@gmail.com
Great job John. It is hard to keep a good engineer down.